If you’re wondering what the different types of warehouses are, you’re in the right place.
Because in this guide, you’ll learn not only about the different types but also:
-
The chief characteristics of each warehouse type
-
Their pros and cons
-
Plenty of examples of warehousing
-
Tips for choosing the right type of warehouse
-
Answers to common warehouse questions
Let’s dive in!
13 Types of Warehouses
To the average person, a warehouse is a warehouse.
But, there are actually many different types of warehouse storage in logistics and supply chains.
Let’s go into more detail about 13 specific types.
1. Government Warehouses
The United States Federal government leases or owns 90 million square feet of warehousing space across 19,000 buildings.
This accounts for 15% of the total warehousing industry in the US.
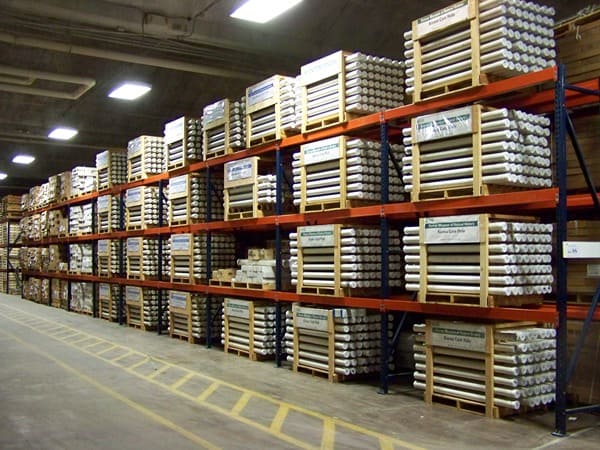
Government warehouses are mainly used to store supplies for local government offices, schools, and hospitals.
They also hold things like emergency kits for fires and natural disasters.
Moreover, some government warehouses (called “municipal warehouses”) store salt for winter roads, street sweepers, wheel loaders, and garbage trucks.
Some of the top users of government warehousing include the:
-
U.S. General Services Administration
-
U.S. Department of Interior
-
U.S. Department of Energy
-
U.S. Geological Survey
-
U.S. Department of Homeland Security
2. Private Warehouses
Looking for a private warehousing definition?
Also called a “proprietary warehouse,” private warehouses are owned by the same companies that produce the goods they store.
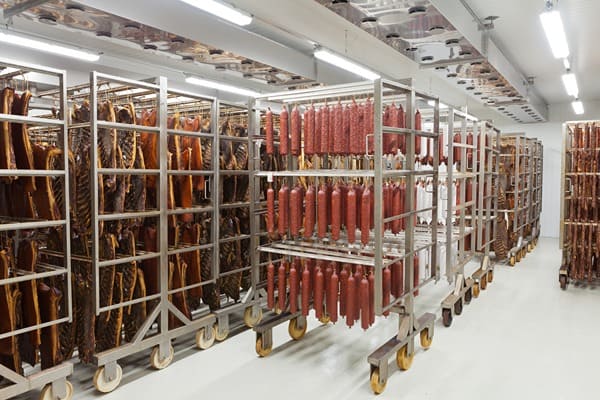
Companies often choose private warehouses because of the high degree of control that they confer over the handling and storage of goods.
This allows companies to keep a closer eye on inventory levels, product flows, and shipping.
Additionally, some businesses that own private warehouses adopt a hybrid model, wherein they lease extra open space to other companies to store their goods.
This means they act as third-party logistics (3PLs) and may even offer value-added fulfillment services to help subsidize the costs of running the warehouse.
Pros of Private Warehouses
-
A higher degree of control over inventory management, such as space utilization, inventory tracking, and team management
-
More insight into inventory levels and better control over goods
-
Provides a higher return on investment (ROI) for companies that need long-term storage compared to leasing warehousing space
-
Less product damage and better brand experience for customers because there’s no intermingling between one company’s goods and another’s
Cons of Private Warehouses
-
High capital and operating costs make private warehouses a realistic option only for large, established businesses
-
Owners/operators are responsible for the full setup and operation, including building design and construction, registration, hiring, and ongoing maintenance
-
Less-than-ideal for businesses with cash flow issues since achieving a positive ROI can take a long time
-
Difficult and expensive to create more space to account for spikes in demand, seasonal changes, supply chain disruptions, or handling multiple SKUs
Want to build your own private warehouse but don’t know where to start?
Find your way with our full-service warehouse design and consulting services. Contact us today to learn more.
3. Public Warehouses
Now that we’ve covered private warehouses, let’s give a public warehouse definition.
Also called third-party logistics (3PL) warehouses, public warehouses are owned and operated by companies that lease the space to other companies.
In essence, public warehouses function as outsourced logistics operations wherein other businesses or individuals can receive, hold/store, and ship their goods.
Most warehouses of this type operate on a pallet in/pallet out model where billing usually occurs monthly or yearly and is calculated by the pallet or the square footage used.
Overall, public warehouses are cheaper than private warehouses.
This makes them ideal for newly-established or small businesses like startups and those that operate on a seasonal basis.
Pros of Public Warehousing
-
No need to pay for warehouse design, equipment sourcing, or ongoing operating costs
-
No need to hire, train, and manage staff as the warehouse owner is responsible for these
-
Flexibility to store goods for short or long terms
-
Lower transportation costs and faster order fulfillment with the ability to choose warehouses by their closeness to customer bases
-
Many offer value-added services such as billing, scheduling, managing orders, packing, assembling, and shipping stored goods
-
Lower freight costs since these warehouses often negotiate favorable rates with freight companies based on their volume of clients and order throughput
Cons of Public Warehouses
-
Less control and insight into inventory levels, product flows, and product handling since the items are out of the client’s supervision
-
More costly in the long run than private warehousing, making it a less attractive option for companies that need long-term storage
-
Greater potential for errors as public warehouses handle many clients and SKUs and may not always have a lot of information on them
-
Fewer value-added services compared to fulfillment centers and contract warehousing
4. Fulfillment Centers
Technically a type of public warehouse, fulfillment centers are a popular warehousing solution for E-commerce companies looking for “turnkey” order fulfillment services.
This is because a fulfillment center encompasses all aspects of logistics – from receiving, storage, processing, and filling customer orders, to picking, packing, and shipping.
And for some companies, such as start-up E-commerce businesses, having these activities done on their behalf is very important.
Here’s how it works:
- Goods are sent to the fulfillment center either directly from the business’s stock or the manufacturer to the fulfillment center
- The fulfillment center stores, processes, and ships the stock to the end-user using specialized material handling equipment, automation, and robotics
Perhaps the most prominent fulfillment center example is Amazon’s fulfillment centers.
These warehouses hold products for a variety of businesses that are independent of Amazon but also sell on the Amazon platform.
When a customer orders, Amazon – via their “Fulfillment By Amazon” (FBA) service – picks, packages, and ships their products to the customer.
Thus, the actual seller doesn’t have to bother with any of the logistics of fulfilling the order.
Pros of Fulfillment Centers
-
No need to handle the logistics of selling: You send them all your stock and they inventory, pick, assemble, package, and ship to your customers when they buy
-
Flexibility to handle processing returned orders (technically called “reverse logistics”)
-
Suitable for both business-to-consumer (B2C) and business-to-business (B2B) goods
-
It eliminates the need for separate warehousing or another facility for storage
-
Allows companies to focus their resources and energy on more important tasks like customer service, marketing, and product development
-
Many fulfillment centers offer national and international services so businesses can extend their market reach while still being able to quickly reach core customer bases
-
Fulfillment centers often have advanced software that offers better insight into inventory levels along with the ability to track clients’ inventory levels and movement
Cons of Fulfillment Centers
-
Costs can add up quickly, especially if making extensive use of their value-added services
-
Little control over how your items are handled and shipped, which can risk product damage and unhappy customers
-
Best suited for storing items on a short-term basis, such as those with a quick turnaround
-
May not offer bulk shipping, making it less ideal for storing and processing large quantities of goods
5. Contract Warehouses
Like fulfillment centers, contract warehouses are a subtype of public warehouses.
The difference is that, instead of operating on a first-come, first-serve basis like a basic public warehouse, contract warehouses guarantee storage space whenever it’s needed.
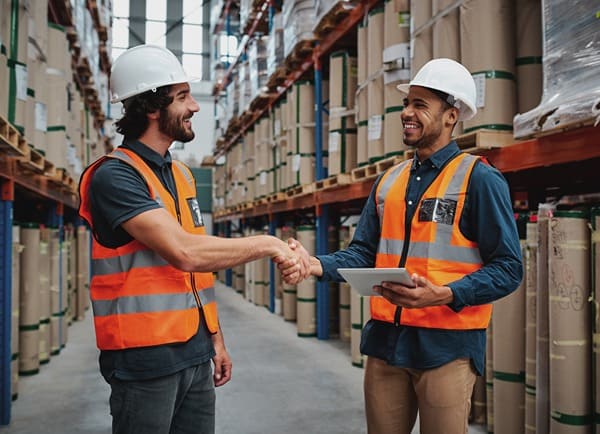
Essentially, contract warehousing is on-demand warehousing that connects businesses that need storage with warehouses that have free space, and often in real-time.
Pros of Contract Warehouses
-
Provides guaranteed storage space when businesses need it, such as during seasonal peaks, unexpected demand, or disruptions in production
-
Allow businesses to take a “hands-off” approach to storing, handling, and transporting their goods
-
Some provide value-added services like kitting, branding, and quality inspections
-
No need to train employees on equipment or software since the warehouse provides management services
Cons of Contract Warehouses
-
They’re more difficult to come by compared to public warehouses
-
Clients have little control over how their products are handled since it’s outsourced to the warehouse operator
-
More expensive over long periods than owning your own warehouse
6. Bonded Warehouses
Also called “customs warehouses,” bonded warehouses are used to store imported goods – for up to 5 years per U.S. customs – before duty payments come due.
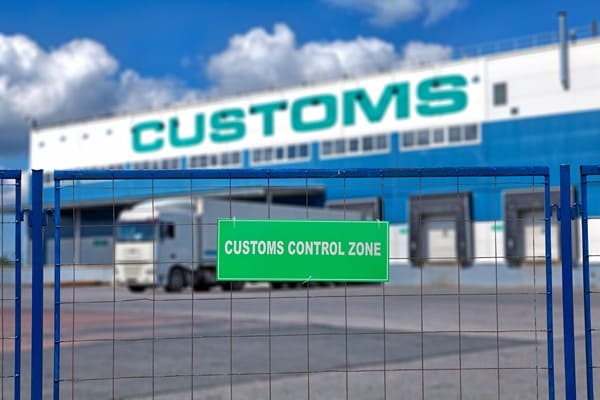
Here’s how bonded service warehouses work:
-
A business contracts with the bonded warehouse proprietor to store their goods
-
The liability for the stored, bonded goods transfers to the warehouse proprietor
-
The proprietor pays the duties when the goods are sold from the warehouse
-
If the goods or items are not sold or end up being distributed internationally, the proprietor liability and duty tax don’t apply
Bonded warehouses are generally used by companies engaged in import/export and cross-border trade.
And because customs officials are often at national borders, these warehouses are usually also close to borders, such as in seaports and airports.
Types of Bonded Warehouses
The U.S. Customs and Border Protection agency lists 11 different classes of bonded warehouses.
Here’s their bonded warehouse list (which has been edited and condensed for simplicity):
- Government-owned or leased bonded warehouses (used to store goods as they’re processed through customs temporarily)
- Private bonded warehouses (the goods stored are owned by or consigned to the warehouse proprietor)
- Public bonded warehouses for storing imported merchandise
- Bonded yards and sheds for oversized goods or animals
- Bonded bins, buildings, or elevators used for grain storage
- Bonded import/export manufacturing warehouses (for storing goods composed of imported or taxed materials)
- Bonded warehouses used for smelting and refining imported metals
- Bonded refinement warehouses (where imported goods are processed but not manufactured)
- Duty-free warehouses where goods that will be exported can be stored
- Bonded warehouses for items sold during international travel (like beverages sold on an international flight)
- Bonded warehouses for storing unclaimed imported goods
Pros of Bonded Warehouses
-
Distributors can preserve cash flow by delaying import/export duty fees until the product is sold
-
Goods that don’t sell may be exempt from duty fees, thereby reducing the inherent financial risks involved in importing/exporting
-
Can hold a wide variety of items, products, and materials
-
Allow international goods to be moved closer to customer bases
-
Expedited cargo and lower costs on account of their close location to ports and borders
Cons of Bonded Warehouses
-
Can be complex, challenging, and expensive to arrange cross-border cargo, including passing customs permits, license requirements, compliance, and other permissions
7. Distribution Centers
Many people ask “what is ‘DC’ in warehousing?”
The answer is that “DC” stands for “distribution center.”
What is the difference between a warehouse and a distribution center?
Explaining how distribution centers work may help clear things up:
Warehouses typically store goods for longer periods, whereas warehouse distribution centers temporarily store goods while they are prepared for routing to the retailer.
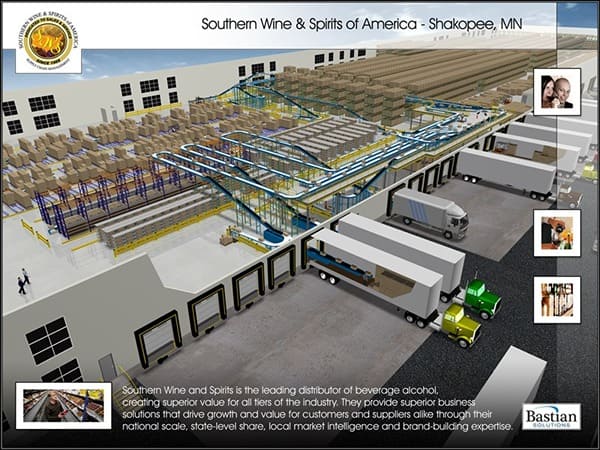
In effect, distribution centers serve as an intermediate stage between a manufacturer and the retailer who actually sells the product to the end-user.
Pros of Distribution Centers
-
Ability to quickly process many SKUs and large order volumes while keeping out-the-door times low for better customer satisfaction
-
Offer faster delivery as they’re often located close to customer areas
-
Better quality control with heavily-computerized systems and automation to manage their operations
-
Generally cheaper than fulfillment centers
Cons of Distribution Centers
-
Compared to fulfillment centers, distribution centers offer fewer value-added services like kitting, cross-docking, and pick-and-pack services
-
Not applicable to most businesses, as it’s an end-of-line process best suited for large distributors like Amazon, Walmart, and Target
8. Cross-Docking Warehouses
A cross-docking warehouse is where goods from inbound trucks are sorted and routed to outbound trucks for final delivery to the end-user.
Why exactly are cross-docking warehouses important?
Because they help reduce waste by consolidating all items going to specific geographic areas.
Doing it this way, a single truck can deliver to multiple places in one area instead of multiple trucks delivering to the same delivery area.
Here’s how it works:
- Goods come into the warehouse from various inbound trucks
- They’re sorted and distributed among outbound trucks assigned to particular routes
- The trucks go door-to-door or business-to-business delivering that day’s goods
Pros of Cross-Docking Warehouses
-
Lower fuel usage and emissions by not having multiple trucks stop at multiple locations
-
Less handling reduces delivery/material handling costs and chances of product damage
Cons of Cross-Docking Warehouses
-
Not applicable to most businesses, as it’s an end-of-line process best suited for large parcel carriers like UPS, FedEx, and DHL
-
It’s only financially viable where there are more extensive inventories
9. Cooperative Warehouses
Cooperative warehouses are owned, run by, and mostly service co-ops such as farmers, wineries, retail, and natural food stores.
For example, take Co-op Partners Warehouse in St. Paul, Minnesota.
As noted on their website, they serve “Midwestern co-ops & natural grocers, restaurants, coffee shops, educational institutions” with their warehousing and distribution needs.
The advantage of cooperative warehouses is that members pool their resources together so that each can get incentives like reduced rates.
It’s a combined investment, which makes it easier for businesses to get storage if they don’t have all the capital to construct a warehouse.
And although co-ops get the best pricing, some cooperative warehouses do allow non-cooperative businesses to store their goods.
Pros of Cooperative Warehouses
-
A more cost-effective storage option for cooperative businesses than public warehousing
-
Designed to distribute local goods to markets beyond what many individual co-ops would be able to reach on their own
-
May offer more advanced services, like drop shipping, local delivery, or interstate delivery
Cons of Cooperative Warehouses
-
Not as common as other types of warehousing
-
The pricing advantage benefits cooperative businesses over non-cooperative businesses
10. Climate-Controlled Warehouses
Many people wonder: “What are climate-controlled warehouses?”
Climate-controlled warehouses store perishable or other sensitive items that require specific temperatures and/or moisture ranges.
They use specialized HVAC systems, dehumidifiers, thermostats, and insulation to maintain internal airflow, temperature, and moisture levels.
These systems and controls help limit the loss of integrity when storing items like produce, meat, artwork, and pharmaceuticals.
Pros of Climate-Controlled Warehouses
-
Helps preserve goods by reducing how much water is lost, which helps reduce decay, mildew growth, and mold
-
Many types of climate-controlled and cold storage warehouses are available to store a wide variety of items with specific requirements
-
The best warehouse operators offer strict quality monitoring, control, and backups to ensure sensitive products remain stable
Cons of Climate-Controlled Warehouses
-
They are not as common as ambient temperature warehouses and thus may be harder to find in some areas
-
More expensive than regular dry storage due to higher operating costs
-
Outsourcing the storage and handling of very sensitive items (like expensive artwork) is high-risk and can drive up costs
11. Hazmat Warehouses
Hazardous materials warehouses are similar to temperature-controlled warehouses in that both have to maintain high storage standards.
But hazmat warehouses specialize in – you guessed it – storing hazardous materials, including things like:
-
Gasses and chemicals
-
Weapons, ammunition, and explosives
-
Radioactive materials
-
Biological materials, including viruses, bacteria, and communicable diseases
They’re often located away from major population areas to mitigate danger and have many stringent requirements, such as:
-
Climate-control (temperature and humidity)
-
Extra space to prevent items from contacting one another
-
Round-the-clock security
-
Hazmat-trained staff
These attributes also mean that hazmat warehouses are very expensive to store materials in and operate, which limits their use to large businesses or the government.
12. Reverse Logistics Warehouses
Reverse logistics refers to the process of deciding what happens to an item once it’s returned.
In some cases, the item may simply be repackaged and resold.
In other cases, it may be destroyed, recycled, repaired, or refurbished.
A reverse logistics warehouse can refer to either a facility solely dedicated to this process.
Or, it can refer to a general warehouse that handles reverse logistics activities along with normal warehousing operations like picking, packing, and shipping goods.
Pros of Reverse Logistics Warehouses
-
Offering returns helps companies improve customer satisfaction
-
Helps identify ways to reuse, recycle, or resell products and reduce landfills
-
Helps recapture the value of products by sorting those that can be resold or reused
Cons of Reverse Logistics Warehouses
-
Stand-alone reverse logistics warehouses are not as common as other warehouses and may be difficult to come by
13. Smart Warehouses
Smart warehouses – also called automated warehouses – make heavy use of automated technology to replace manual warehousing processes.
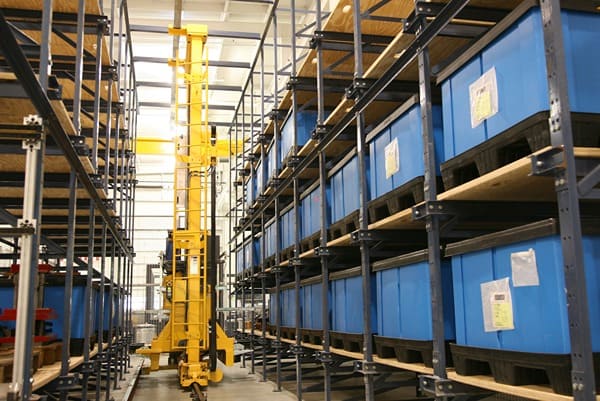
These technologies include:
-
Automated storage and retrieval systems (ASRS): Consist of racking, robotic cranes, carts, and software. Used to automatically place goods in storage racking or retrieve them for packing/shipping
-
Automated guided vehicles (AGVs) and autonomous mobile robots (AMRs): These can be programmed to perform tasks like transporting goods, replenishing stock, or even performing inventory counts without human intervention
-
Conveyor systems and accessories: Sortation conveyors, robotic document inserters, and automated digital scales are just a handful of smart conveyor technologies that can automate repetitive warehousing tasks
-
Warehouse management systems (WMS): Software applications designed to help manage day-to-day warehouse operations such as inventory tracking, picking, packing, and shipping
-
Collaborative robots: Also called “cobots,” they’re robots designed to work side-by-side with human workers and assist with tasks like packing and kitting
These systems are usually integrated into the overall warehousing process and help perform tasks like order picking, weighing, packing, and transporting goods and materials.
Technically, any type of warehouse can be a smart warehouse if it uses smart technology for warehouse automation.
But companies like Best Buy, Puma, and Amazon use warehouse automation more than most warehouses.
Pros of Smart Warehouses
-
High productivity and efficiency with little labor and supervision required since machines are doing most of the work
-
Less human error improves safety and reduces inventory issues
-
Higher return on investment in the long run
-
A wide array of automation technology available to accommodate many product types, material flows, and custom applications
Cons of Smart Warehouses
-
It can be expensive to fully automate a warehouse
-
Vulnerable to computer malfunctions and large-scale electricity blackouts
-
Some equipment and/or software systems may require specialized training for operators to be able to manage them
6 Questions to Ask to Find the Right Type of Warehouse
With all the different types of warehouses available, you might be wondering which is the best fit for you.
Let’s discuss 6 questions that can help make the decision clearer.
1. What Do You Handle?
You should first consider the characteristics of items you need to accommodate.
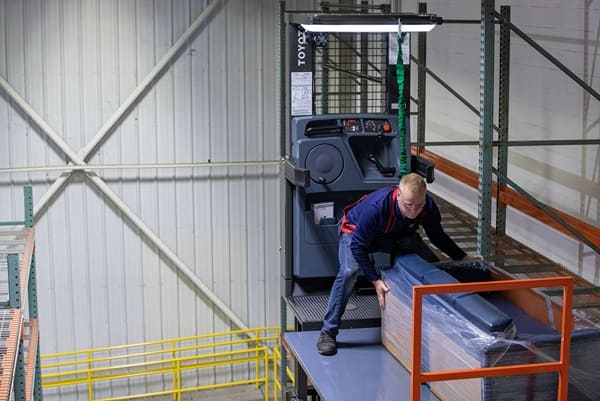
For example, are your items:
- Relatively small and easy to handle, like novelty toys or clothing?
- Large, like furniture, electronics, or appliances?
- Perishable, like meat or flowers?
- Extremely sensitive, like vaccines or hazardous materials?
You’ll also need to identify whether you’ll need any government licenses, permits, or authorization.
For instance, will your goods be internationally-traded?
And if so, will you need to deal with import/export or duty fees?
2. How Close Is It to Your Customer Base?
The proximity of your chosen warehouse to your customer base and delivery points is an important factor when selecting a warehouse.
Put simply, shorter distances from customers mean faster delivery.
And that translates to more efficient order fulfillment and better customer satisfaction.
3. How Close Is It to Transport Modes?
Consider how close the warehouse is to your preferred delivery and transport modes.
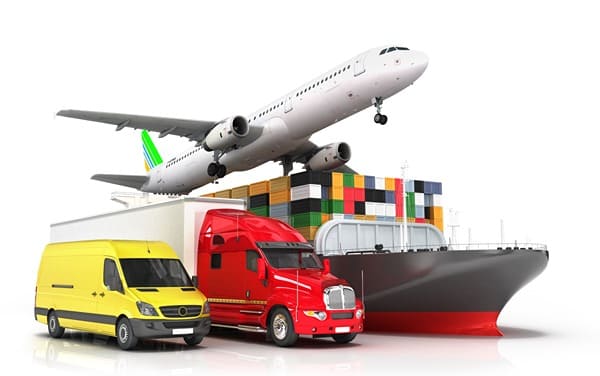
The closer the warehouse is, the faster your customers will receive their goods, and the happier they’ll be.
So, find out if there’s easy access to highways, railways, airports, and/or seaports and judge the warehouse accordingly.
4. What Is Their Software and Hardware Sophistication?
The more sophisticated a warehouse’s systems are, the better insight you’ll have into your inventory levels and product flows.
And that will afford you a better ability to communicate important information to customers, such as shipment updates.
For instance, a basic public warehouse may not have that level of sophistication.
But, a fulfillment center might – so ensure you take this into account when choosing your warehousing partner.
5. What Is Security Like?
The security of your products depends on the liability agreement you have with the warehouse proprietor.
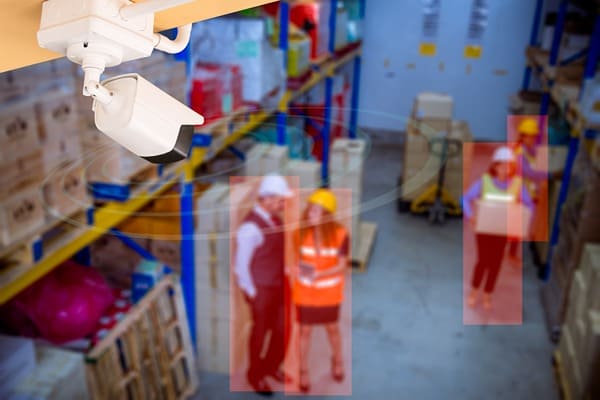
But in any case, you don’t want to lose merchandise to theft or vandalism.
Thus, warehouses should have robust security measures like 24/7 security staff, cameras, and controlled access to keep goods safe and secure.
6. How Good Is Their Customer Service?
It’s always good to be able to talk to someone if there’s a problem.
If you haven’t already, give them a call and ask a few questions about their operation (use the questions in this section as your guide).
Just a short conversation with their support or sales staff can give you a good idea of how they care for potential customers.
You can also check their online ratings, or – better yet – speak to a current or former client of the warehouse to get their opinion before proceeding.
9 Frequently Asked Warehouse Questions
1. What Is Warehousing in Logistics?
Warehousing refers to the storage of goods and materials until they can be used or consumed by another party.
2. Why Is Warehousing Necessary?
At its core, a warehouse provides a way to cope with differences in supply and demand for products and materials.
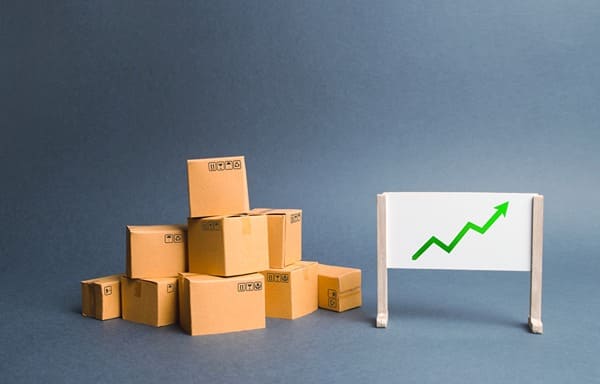
This is necessary because manufacturers can produce their goods at a lower cost when they do so in bulk.
But if there isn’t enough consumer demand for those goods, they’ll sit.
Thus, warehousing provides a safe means of storage for produced goods until they can be sold or otherwise used.
3. What Are the Functions of Warehousing?
Warehousing serves many important purposes including:
-
Facilitating the process of receiving, storing, and distributing bulk goods from manufacturers or wholesalers to retailers or customers
-
Helping stabilize prices by providing a buffer against differences in supply and demand
-
Helping reduce transportation and distribution costs by combining items from different sources before they’re sent to end-users
-
Making products available for consumption at the right time and in the right place
-
Supporting the handling of a variety of products with different sizes, shapes, weights, longevity, handling requirements, etc.
-
Allowing manufacturers to maintain a steady supply of raw materials for production
-
Helping protect goods from damage due to the environment like sunlight, wind, rain, snow, and pests
4. What Are the Benefits of Warehousing?
Four key benefits of warehousing are:
-
Provides safe storage. Warehouses allow businesses like E-commerce start-ups to safely store goods somewhere other than their office, home, garage, etc.
-
Helps cope with spikes and troughs. Warehousing allows businesses to cope with seasonal spikes and unanticipated growth. Thus, they don’t have to take on lots of extra inventory while still being able to meet customer demand
-
Stabilizes prices. Warehousing helps stabilize prices by making up for the differences between supply and demand
-
Enables greater focus on higher-impact business activities. Warehouses that provide services like kitting, labeling, and packing orders allow businesses to focus on higher-impact tasks like product development, customer service, and marketing
5. How Do Warehouses Work?
Warehouses work by carrying out tasks within a 3-part operational framework:
-
Processes: Everything that happens to items between when they enter the warehouse and when they leave, like receiving, placing, picking, and loading
-
Resources: The equipment and people who perform the warehouse processes, and can include warehouse teams, material handling equipment, and computer systems
-
Organization: The ongoing management activities to check processes and resources and facilitate an effective warehouse workflow
6. What Are the Two Basic Types of Warehouses?
The 2 basic types of warehouse storage are:
- Production warehouses
- Distribution warehouses
Production warehouses (also called “manufacturing warehouses”) are used by factories and other producers for storing raw materials, work-in-progress (WIP) goods, and finished goods that are ready for shipping.
Distribution warehouses, on the other hand, are facilities designed for storing goods temporarily until they’re routed to retailers or end-users.
7. What’s the Difference Between a Warehouse and a Factory?
The basic difference between a warehouse and a factory is that warehouses store goods while factories produce goods.
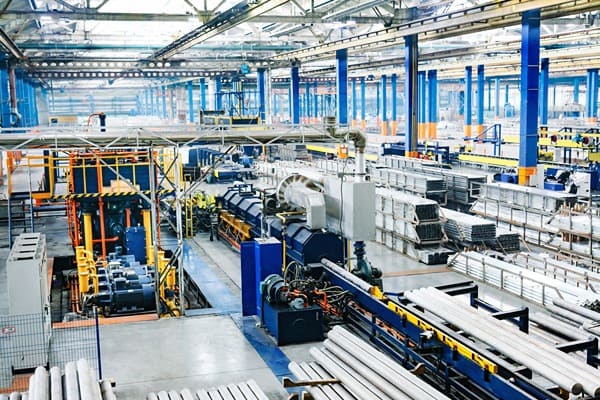
That said, both functions can take place in a single facility, in which case it’s called a production warehouse.
8. What Are the Main Problems in Warehousing?
Common issues in warehousing include:
-
Keeping costs low despite labor shortages
-
Making the best use of available space to increase the value of each pallet position
-
Devising strategies for handling an increasingly greater variety of products and higher throughput while maintaining order fulfillment accuracy
-
Keeping up with customer demand for fast delivery times
-
Coping with new production methods, like Just-in-Time (JIT) and lean production
-
Staying current with advanced technologies like warehouse automation (AS/RS, WMS, predictive maintenance, etc.)
9. What Does the Future of Warehousing Look Like?
Predicting the future is impossible, and it’s no different for warehousing.
But here are some trends we’re likely to see going forward:
-
Greater warehouse automation and the use of robotics
-
Increased demand for warehousing space due to more online ordering
-
More conversion of out-of-business retail spaces into warehouses and storage spaces
-
More warehouse value-added activities, including all-in-one repair and service centers
-
Increases in the popularity of cross-docking warehouses
-
More reverse logistical operations
-
Integration with new information technologies, like RFID, barcode scanning, and warehouse management systems
-
Greater inventory visibility and control using tracking software
-
Improved communication between the various supply chain components
Conclusion
That’s it: The 13 warehouse types.