A well-designed warehouse racking system is the backbone of efficient inventory management. Whether you’re storing pallets, cartons, or long and bulky items, the right racking solution can drastically improve storage capacity, streamline operations, and reduce overhead costs. From selective pallet racks to high-tech automated systems, there are numerous options tailored to specific warehouse needs, layouts, and workflows.
In this guide, we’ll break down the most common types of racking systems, explain key design considerations, and help you understand pricing, components, and whether new or used racking is the right fit for your facility.
Let’s dive in!
What is a Warehouse Racking System?
Industrial shelving comes in many forms to suit different load types (pallets, cartons, long items) and storage structures, providing solutions for efficient storage in warehouses. Broadly, racking systems can be grouped into pallet racking (for palletized loads) and shelving systems (for individual items or cartons), among other specialized racks. Warehouse storage is crucial for organizing products and maximizing space efficiency. Below is a breakdown of the most common types of racking systems used in warehouses:
Types of Warehouse Racking Systems
Selective Pallet Racking
The most common and versatile racking type, allowing direct access to every pallet. It works with standard forklifts and is ideal for warehouses with many SKUs but lower pallet counts per SKU.
Pros: Highly accessible, easy to install, lowest cost per pallet position.
Cons: Lowest storage density, requiring more aisle space.
Double Deep Racking
An extension of selective racking that stores pallets two-deep, increasing storage density but requiring Last-In, First-Out (LIFO) retrieval. Specialized reach forklifts are needed to access rear pallets.
Pros: More pallets stored per aisle, cost-effective for added capacity.
Cons: Reduced selectivity, requires double-reach forklifts, and only works for LIFO inventory.
Drive-In/Drive-Through Racking (Compact Pallet Racking)
A compact, high-density system where forklifts drive into deep lanes of racks. Drive-in uses LIFO, while drive-through supports FIFO. Best for storing large quantities of the same SKU.
Pros: Maximizes space (up to 70-80% storage utilization), cost-effective for high-density storage.
Cons: Limited selectivity, slow forklift operation, higher risk of rack damage.
Push-Back Racking
Push back racking systems use rolling carts on inclined rails to store 2-6 pallets deep, pushing back pallets during the loading process and retrieving them from the front, with LIFO retrieval. Ideal for balancing density and selectivity.
Pros: High-density storage with better accessibility than drive-in racks, no special forklifts needed.
Cons: Expensive, LIFO only, slight loss of vertical space due to cart system.
Gravity Flow Racking (Pallet Flow Racks / Roller Racks)
A FIFO storage system using sloped roller conveyors that move pallets automatically by gravity. Common in high-volume, perishable goods warehouses.
Pros: High storage density, automated stock rotation, reduces forklift congestion.
Cons: Expensive to install, requires high-quality pallets, and needs ongoing maintenance.
Mobile Racking Systems (Mobile Pallet Racks)
Pallet racks mounted on motorized bases that move to open aisles on demand, maximizing space. Ideal for cold storage or small warehouses.
Pros: Doubles storage capacity while maintaining full pallet selectivity.
Cons: High installation cost, slow aisle access, requires maintenance.
Warehouse Shelving Systems (Static Shelving & Flow Shelving)
Used for non-palletized storage like boxes, bins, or small items, available in light-duty to heavy-duty shelving, carton flow racks, and mezzanine systems.
Pros: Efficient for small items, highly flexible for different SKUs.
Cons: Labor-intensive for picking, requires more aisles than high-density racking.
Cantilever Racking (for Long Items)
Designed for long and bulky items like lumber, pipes, or furniture, featuring open-front storage with horizontal arms.
Pros: No length restrictions, easy loading/unloading.
Cons: Not suitable for standard pallets, requires more horizontal space and specialized forklifts for long items.
Automated Racking Systems (AS/RS and Shuttle Systems)
High-tech storage using cranes or shuttle carts for automated pallet movement. Common in high-volume warehouses to reduce labor.
Pros: Maximizes density and speed, improves accuracy and safety.
Cons: High initial cost, complex maintenance, and less flexibility once installed.
Warehouse Racking System Design
Step-By-Step Pallet Rack Design Guide
Part 1: Plan Your Warehouse Racking Layout
Step 1: Measure Your Space
Determine the total square footage available for racking.
Step 2: Identify Obstacles
Account for columns, doors, mezzanines, and other obstructions.
Step 3: Optimize Product Placement
- Place fast-moving products near shipping lanes to optimize the warehouse layout. Factors like aisle width and docking locations can significantly influence the choice and arrangement of racking systems, ultimately affecting storage efficiency and inventory accessibility.
- Store production materials close to the production line to minimize pick times.
Part 2: Design Your Pallet Racking Sizes
Step 4: Measure Your Pallets
Identify the largest pallet’s height, depth, width, and weight to determine storage space needs.
Step 5: Select Frame Depth
Common depths: 42”, 48”, and 36”. To calculate: Pallet Depth – 6” = Frame Depth. (e.g., 48” pallets require a 42” frame).
Step 6: Choose Beam Sizes
Beam sizes range from 4’ to 12’. Consider:
- Pallet width + spacing (3” between frame, 4” between pallets).
- Beam capacity based on height and length. (See reference chart or consult a professional).
Step 7: Determine Upright Height
Standard sizes: 8’ to 20’. To optimize space, consider the importance of vertical stacking to improve storage capacity and enhance operational workflows. To calculate: (Pallet load height + pallet height) × number of pallets stored high + beam height + 3” clearance. Ensure 18-24” clearance from the ceiling for fire safety. Also, verify forklift lift height compatibility.
Part 3: Choose Your Aisle Width
Aisle Types:
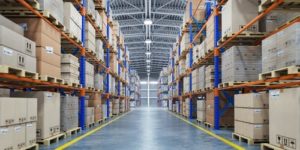
Wide Aisles (10.5’-13’) – Works with standard forklifts, but reduces storage density.
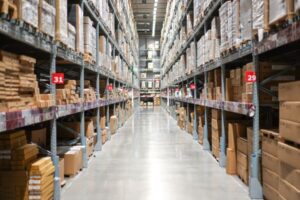
Narrow Aisles (8.5’-10.5’) – Increases storage but requires forklifts with tight turn radius (e.g., three-wheel forklifts, reach trucks).
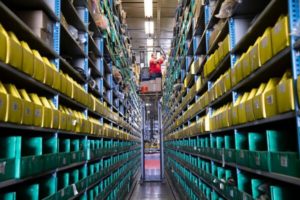
Very Narrow Aisles (5’-7’) – Maximizes storage but requires specialized VNA forklifts and additional training.
How to Calculate Aisle Width
Use this formula:
Basic Right Angle Stack (from forklift specs) + 12” clearance + Load Length (typically 48”)
Example: Right Angle Stack (82”) + 12” + 48” = 142” (~12’ wide aisle).
Warehouse Racking System Components
Understanding the components of a racking system is crucial for safe design and use. Industrial pallet racking is composed of many parts that together ensure the structure’s stability and load-bearing capacity. The basic components common to most pallet rack systems include:
Structural Components
- Upright Frames – Vertical steel posts that bear weight and connect to beams, with bracing for rigidity. Pallet racking systems utilize these upright frames to provide comprehensive storage solutions for warehouses and industrial facilities.
- Horizontal Beams – Load-bearing members that connect uprights, available in step beams (support crossbars/mesh decks) or box beams (compatible with wire mesh/safety bars).
- Braces – Horizontal and diagonal supports welded to uprights for extra strength.
- Baseplates – Footplates that anchor the uprights to the floor for stability.
Support & Safety Elements
- Crossbars – Support bars placed between beams to prevent pallets from falling. The use of appropriate material handling equipment is crucial in ensuring efficient inventory management and safety in the warehouse.
- Clips (Beam Locks) – Small fasteners that secure beams to uprights, preventing dislodging.
- Decking (Shelf Panels) – Wire mesh, wood, or metal panels placed on beams for storing smaller items or loose materials.
- Row Spacers & Overhead Bracing – Used in back-to-back racks to increase stability and alignment.
- Anchor Bolts – Secure uprights to concrete floors, ensuring stability.
Safety Accessories
- Column Protectors & End-of-Row Guards – Steel guards protecting uprights from forklift damage.
- Wire Mesh Backing – Prevents pallets from falling off the back of racks.
- Pallet Support Bars – Prevent pallets from falling through gaps between beams.
- Load Stops – Prevents pallets from being pushed too far off racks.
- Signs & Labels – Indicate load limits and safety instructions.
- Shims & Levelers – Used to level racks on uneven warehouse floors.
Warehouse Racking Materials and Construction
Warehouse racking systems are typically constructed from high-quality materials, including:
- Steel: This is the most common material used in warehouse racking systems, due to its strength, durability, and affordability.
- Aluminum: This is a lightweight and corrosion-resistant material that is often used in warehouse racking systems.
- Wood: This is a sustainable and cost-effective material that is sometimes used in warehouse racking systems.
Warehouse racking systems are designed to be durable and long-lasting, with a typical lifespan of 10-20 years or more. Regular maintenance and inspection can help extend the life of a warehouse racking system and ensure its continued safety and efficiency.
Warehouse Racking System Price
When it comes to the cost of warehouse racking, the rule of thumb is the higher the storage density, the higher the cost. Various types of industrial racking solutions, such as high-density, pallet, and picking storage systems, are designed to enhance warehouse efficiency by accommodating specific materials and workflows.
So selective racking – since it offers less density – will cost less than pallet flow racking, for example.
Drawing from TranSystems’ Rules of Thumb: Warehousing & Distribution Guidelines, here are the prices you can expect to pay for warehouse racking:
Selective Pallet Racking
Storage Capacity | Cost |
---|---|
One Pallet Deep | $50 – $75 |
Double Deep | $65 – $90 |
Drive-In Pallet Racking
Storage Capacity | Cost |
---|---|
2 Pallets Deep | $80 – $105 |
3 Pallets Deep | $75 – $105 |
4+ Pallets Deep | $75 – $100 |
Drive-Through Pallet Racking
Storage Capacity | Cost |
---|---|
2 Pallets Deep | $80 – $120 |
3 Pallets Deep | $80 – $115 |
4+ Pallets Deep | $80 – $110 |
Push-Back Racking
Storage Capacity | Cost |
---|---|
2 Pallets Deep | $110 – $140 |
3 Pallets Deep | $130 – $170 |
4 Pallets Deep | $155 – $200 |
5 Pallets Deep | $175 – $220 |
Pallet Flow Racking
Storage Capacity | Cost |
---|---|
2 Pallets Deep | $135 – $260 |
3+ Pallets Deep | $250 – $400 |
Cantilever Racking
Storage Capacity | Cost |
---|---|
8′ Height, Single – Sided Cantilever (four sets of arms) | $465 – $750 |
Double – Sided Cantilever (eight sets of arms) | $610 – $950 |
12′ Height, Single – Sided Cantilever (6 sets of arms) | $550 – $900 |
Double – Sided Cantilever (12 sets of arms) | $950 – $1,400 |
16′ Height, Single – Sided Cantilever (8 sets of arms) | $1,000 – $1,500 |
Double – Sided Cantilever (16 sets of arms) | $1,600 – $2,200 |
New vs. Used Warehouse Racking Systems
When purchasing warehouse racking, managers must choose between new and used pallet rack systems, considering factors like cost, availability, and long-term needs. Planning and designing efficient storage systems is crucial, and this includes both new and used pallet racking options for maximizing space.
- New Racking Systems: Purchased from manufacturers or dealers, new racks come with warranties, are built to current safety standards, and can be customized to warehouse specifications. They typically include design services, but they are more expensive and involve additional costs like freight and installation. However, they are a long-term investment with high durability.
- Used Racking Systems: A cost-effective alternative, used racks can save 30-50%, are more sustainable, and can be available immediately. However, buyers must inspect for structural integrity, ensure component compatibility, and verify load capacities. Hidden costs, such as transportation and reassembly, may reduce savings. Safety and compliance are critical, and permits may be required.
- Finding Suppliers: Both new and used racks can be sourced from material handling dealers, online marketplaces, auctions, or local businesses. Buying locally can reduce freight costs and allow for inspections before purchase.
- Final Considerations: New racks offer reliability and longevity, while used racks provide upfront savings but require thorough inspection and potential modifications. A combination of both may optimize costs and performance. Proper documentation and maintenance are crucial for long-term safety and efficiency.
Conclusion
Choosing the right warehouse racking system is essential for maximizing space, improving safety, and enhancing operational efficiency. Whether your priority is selectivity, density, or automation, there’s a solution suited to your warehouse’s unique requirements.
By carefully planning your layout, selecting the appropriate components, and weighing the pros and cons of new versus used systems, you can build a storage solution that supports your business today and scales with it tomorrow. Investing in the right racking system isn’t just about storage—it’s about setting your warehouse up for long-term success.