This is your ultimate guide to issues you may face working in maintenance departments.
You’re not only going to learn about the 11 most common ones you will likely be challenged with but you’ll also learn practical strategies for overcoming each.
Ready to learn how to prevent downtime and save money in your operation?
Let’s dive in!
Finding Workers
The labor shortage is one of the key maintenance problems. The logic is simple: Maintenance relies on people to do the work; without the people, no work gets done.
First, the labor shortage issue has been an ongoing problem for a few years. COVID-19 only worsened it. Many Baby Boomers are retiring, and fewer workers from younger generations are coming in to fill their spots.
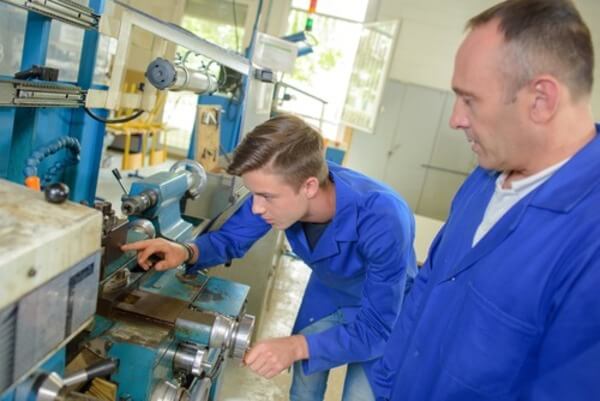
So, qualified workers for maintenance are increasingly harder to find. In fact, there are 11 million job openings but not enough workers to fill them because there are only 6 million unemployed workers.
Second, equipment maintenance has traditionally been seen as a blue-collar activity, which many children were dissuaded from pursuing in favor of white-collar positions. The result is now fewer people who can do mechanical activities.
Solutions
There are various solutions to cope with the labor shortage. We’ve documented them in our labor shortage post. Some include the following:
- A mentorship program for high school students. Allows students to come and work in your workplace for a few hours a day to get hands-on training and experience.
- Allow turning mentorship programs into internships and then permanent jobs.
- Provide scholarship opportunities or funding for technical schools and programs to attract more skilled workers.
- Do a big marketing push to get young people to see why a career in maintenance is good for them.
- Retain your current employees by reducing employee turnover.
- Improve wages.
- Invest in more workers’ training.
- Use referral bonuses for existing employees who refer skilled maintenance workers to your business.
- Employ more women and veterans.
- Automation solutions are becoming more popular in many companies, and maintenance hasn’t been left out. For example, you can automate many material handling tasks if you have trouble finding forklift operators.
Keeping Workers
Retaining workers is the other side of labor problems. If you can retain workers, a high worker turnover could affect your materials and overall business.
Retaining workers is as difficult as finding them today because of high turnover. Worker turnover in the warehouse industry is 46.1% higher than in many sectors. Many businesses onboard new hires, train, and equip them, only for them to leave right away for another opportunity.
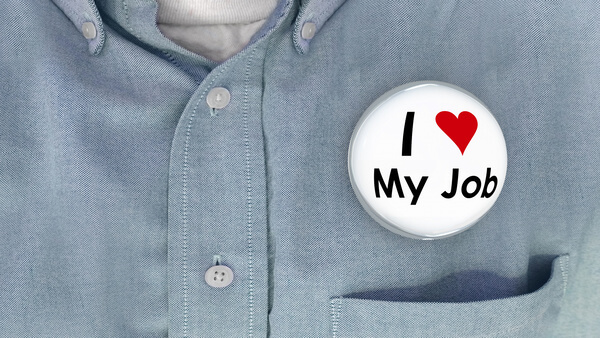
Moreover, if you value your existing staff and their contributions, you want them to continue. But this isn’t usually the case. Plus replacing an employee is difficult because they are difficult to find, and the process of hiring, training, and onboarding takes time and money.
The common factors driving high maintenance turnover rates are:
- New, better opportunities.
- Change of career.
- Understaffing leads to overworking and burnout.
- Unpleasant working environment.
- Little to no work incentives.
- Lack of clear objectives and goals.
Solutions
Fortunately, the majority of the reasons for worker turnover can be resolved.
- Make adjustments according to worker needs. First, find out what your workers lack and what they want. Then make adjustments according to their needs.
- Sort out workers’ pay. Pay and remuneration are big things in any employment scenario. Pay your workers appropriately to convince them to stay. This doesn’t mean overpaying.
- Employee benefits. Work with employees to determine how to give them worker benefits such as retirement benefits, pension funds, health insurance plans, and flexible work hours. Let employees understand that you mind them and their well-being.
- Shifts and flexible work hours. Let employees work in shifts, flexible to meet their needs. For example, you can try experimenting with schedules. If you have five eight-hour shifts, try switching to three 12-hour shifts.
- Training and improvement. Invest in career development programs and provide continuous training to keep workers abreast with current maintenance technologies and support their work growth and development.
- Implement a reward system. Offer bonuses, increase holiday days, publicly acknowledge hard work, and set milestones to reward employees accordingly and encourage them to stick around. People like working towards goals and rewards.
Managing Many Types of Equipment
Depending on your work environment, warehouse type, and the goods you handle, your maintenance teams may be responsible for managing various material handling equipment.
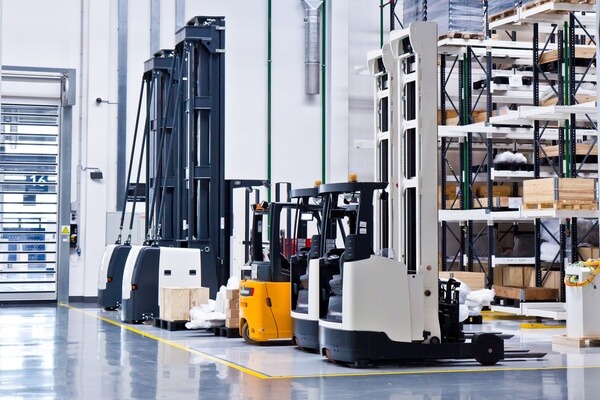
A maintenance team may have to work on many pieces of equipment, from forklifts to conveyor belts
There are three scenarios here:
- Multiple types of equipment. Your warehouse equipment may range from forklifts and conveyor systems to scissor lifts and production machinery like paper converters.
- Multiplicity. You’ll deal with different equipment manufacturers, models, and maintenance requirements.
- Lack of maintenance skills. Your maintenance team may have difficulty understanding what kind of attention to pay to what equipment, when, and how.
Solutions
In addition to your maintenance manager, consider hiring fleet management services like Universal Fleet Solutions (UFS). They can help determine your average spend on equipment maintenance and many other things, such as:
- Using data to understand fleet size & costs and recognize your most efficient fleet size.
- Track asset location anywhere, at any time.
- Streamline facility processes by increasing equipment efficiency to gain optimality.
- Schedule preventive maintenance and track maintenance cycles to reduce downtime.
If you can’t outsource equipment maintenance:
- Hire a skilled maintenance manager who understands the different equipment you use in the facility.
- Provide continuous training and updates on equipment technology to your maintenance workers.
- Create a guided maintenance schedule as recommended by equipment manufacturers.
Tracking Asset Life
Effective asset life tracking and management can extend its lifespan, reduce its maintenance costs, and make it more reliable or less likely to break down spontaneously.
When tracking asset life, distinguish between its economic life and useful life. This is what many people don’t understand.
- Asset useful life. The asset’s useful life is how long it can continue to operate.
- Asset economic life. An asset’s economic life is when it returns more value than it costs to own, operate, and maintain. When these costs exceed the return/value, the asset is beyond its economic life.
An asset that has exceeded its economic value becomes more expensive to continue to operate and maintain than it is to source a new or pre-owned one.
If you continue to use equipment simply because its useful life remains while ignoring its economic life, it may cost more to maintain in the long run.
Also, assets depreciate, and the longer you keep equipment, the less its value becomes.
Solutions
Since many people aren’t aware of this important distinction between useful and economic life, knowing is half the battle. Thankfully, if you didn’t already know it, you now have that part covered!
You can also learn more about it in our guide on forklift useful life.
After knowing this difference, you need to make sure you have carefully-recorded data, including the year of manufacture and hours of use. You’ll use this information in calculating the economic life of your equipment.
If you outsource equipment maintenance providers like UFS, they can help you with this. Conger can also help you in sourcing new and used material handling equipment like forklifts.
You can also use asset tracking software to keep track of your asset and its useful life.
Keeping Up on Preventative Maintenance
Nearly everything with moving parts will require maintenance at some point. Otherwise, it’ll fail. This is where preventive maintenance comes in handy.
Preventive maintenance (PM) is the proactive monitoring and maintenance of assets, including adjustments, lubrication, cleaning, repairs, and replacement parts. It can reduce downtime, keep surprise repairs at bay, and improve productivity. Good maintenance will also give your equipment a longer economic/service life and higher resale value.

If you’re a facility manager, you must have heard a variation of the phrase, “If it’s not broken, don’t fix it.” This may work in the short term, but reactive maintenance may be more expensive in the long run. Plus, unplanned asset downtime or failure is stressful, time-consuming, and costly in terms of productivity.
Preventative maintenance can help catch problems before they balloon into bigger, more expensive problems.
But it can be hard to keep up with preventative maintenance for several reasons:
- Manufacturer recommendations vs. equipment use. Your equipment use may necessitate maintenance, but you will have to check with the manufacturer’s recommendation first.
- Service demands. The equipment may be unable to be taken out of service because production demands it.
- Many types of equipment. Keeping track of the different maintenance intervals for different pieces of equipment is difficult.
- Inadequate maintenance workers or lack of trained and qualified technicians. Having no or few workers available to complete maintenance tasks.
- Lack of planning. Lack of proactive/preventive equipment maintenance plan.
- Operating environment. Equipment used in corrosive or abusive environments may need more frequent maintenance beyond preventive maintenance.
Solutions
- Follow the scheduled preventive maintenance guide to keep your equipment in shape and maintain its economic life.
- Retire old trucks that have passed their economic value.
- Follow the preventive maintenance recommended by the manufacturer.
- Conduct regular inspections.
- Hire the right trained and qualified maintenance technicians for your equipment.
- Do not overwork your equipment beyond their working hours or use them in an abusive environment that exposes them to the need for frequent maintenance schedules.
You can also outsource preventive maintenance. If you don’t have trained and qualified technicians or simply don’t have the manpower to maintain your forklifts, hire a maintenance plan service center like Conger. A factory-trained technician can come in and service your equipment, track when maintenance is due, and alert you to any problems.
Forecasting and Sourcing Parts
Parts are what make a piece of equipment. Getting your equipment’s parts right can improve their efficiency and economic life. Lack of effective equipment parts keeps your machine down.
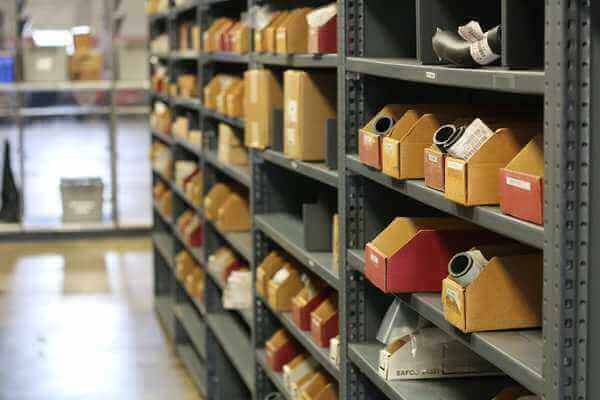
From bearings to forklift forks, many pieces of equipment feature different wearable items. These parts will eventually need to be replaced – or they become more likely to fail. But, with many different types of equipment and maintenance requirements, two important things may be difficult:
- Deciding what parts are needed at any given time.
- Knowing how many parts should be kept in stock.
Furthermore, tracking, managing, sourcing, and ordering parts from different places are difficult tasks, especially when different brands and models are involved.
The ultimate problem is that when a piece of equipment goes down, and you don’t have the part to fix it, the equipment stays down. This can negatively impact many other areas of the business.
Solutions
There are different solutions to equipment parts:
- Work with a parts vendor that handles various brands and models for both OEM and aftermarket parts. If you’re getting parts from one source, you have to do much less work going to different vendors to source them.
- Keep accurate records. All maintenance departments should strive to keep accurate records. Because the better count of the parts you use in equipment history, the easier you can determine what parts you need and how often you need them.
- Use preventative maintenance. Look into the Operator’s Manuals for each piece of equipment you work on and find out when they need replacement, then source in advance.
- Outsource parts sourcing to a maintenance service provider like Conger to help you source parts without hassle.
Minimizing Equipment Downtime
Downtime is bad for business. When downtime is a result of equipment failure, recovery may be difficult. Minimizing downtime is important, especially unplanned downtime.
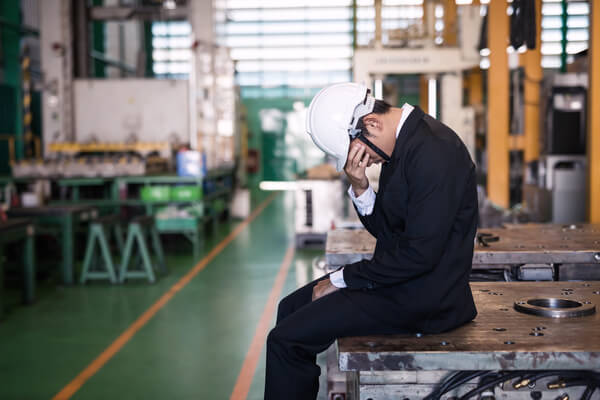
There are 2 main types of downtime:
- Planned downtime.
- Unplanned downtime.
You should prevent how often unplanned downtime happens. And in both cases, you must strive to get the equipment back up and running as fast as possible. One of the root causes of unplanned downtime is disregarding preventive maintenance and putting off repairs to avoid production slowdowns.
For example, if an operation needs to process material within a certain amount of product, shutting down a forklift truck would severely reduce its ability. In this case, the forklift truck keeps on running. You’ll be pushing the machine and risking its failure. This can result in unplanned downtime, which will offset your production gains.
Solutions
There are ways to minimize equipment downtime:
- Employ predictive maintenance and keep up on planned preventative maintenance.
- Use predictive analysis tools to get ahead of events such as equipment failures and transform unplanned downtime into planned downtime.
- Outsourcing maintenance when you can’t keep up helps ensure that your equipment is always maintained.
- Renting equipment like forklifts can be very helpful when trying to minimize the effects of planned or unplanned downtime.
Avoiding or reducing unplanned downtime will benefit the company financially, reducing plant worker injuries, maintaining sustainability compliance, and meeting customers’ commitments.
Keeping Consistent Records
An important maintenance aspect is collecting equipment data consistently and keeping records. Easier said than done.
There are two key problems in maintenance record keeping:
- Poor record keeping.
- Lack of process records or documentation.
Even with only a few pieces of equipment, tracking what gets done each time they’re maintained can be difficult. Poor recordkeeping can obscure your understanding of important things like economic vs. useful life and forecasting parts. Furthermore, poor recordkeeping can result in excessive unplanned downtime and costly maintenance.
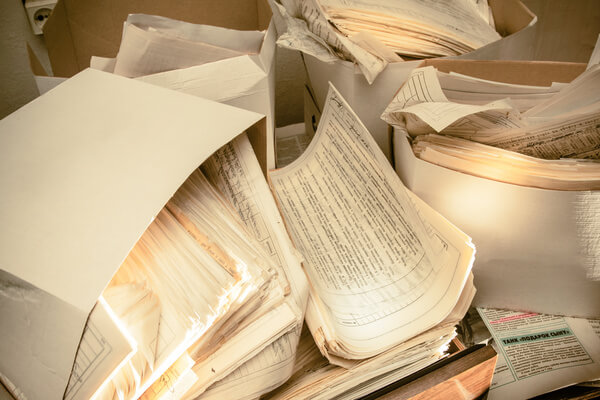
If you can’t establish a pattern, for instance, that a particular piece of equipment fails in the same way in regular intervals, it will cost you a lot of time, money, and hassle.
Another issue with records is not having documented maintenance plans or instructions. For example, if a maintenance issue arose in the past and it was solved, but the solution wasn’t documented, and the technician moved away from the company, that solution process may never be found. If the problem reoccurs, you will have to start from scratch.
Solutions
You can use different solutions to ensure you keep proper maintenance records:
- Use an equipment maintenance log to record all equipment maintenance actions of each piece of equipment, including service provided, dates, technician name, description, etc.
- Use an established software system. If you’re using paper files, try to get to a digital file system that can be more easily searched, analyzed, and have reports drawn from.
- Use fleet management like UFS for effective equipment maintenance tracking.
Reducing Equipment Damage
Anytime there is equipment damage, there is an associated cost and risk of injury to the operators or ground personnel in the area.
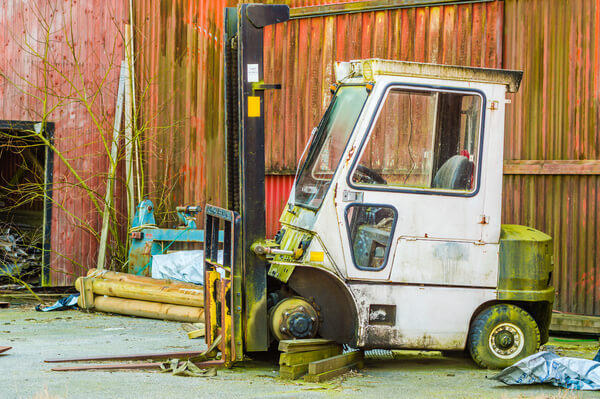
Damage is a leading cause of equipment failure. Damage can come from many sources, including:
- Rough work environments with lots of debris or harsh conditions.
- Workers who were rushed, poorly trained, or simply careless in equipment operation.
- Equipment wear and tear.
Solutions
The best practices to prevent equipment damage are:
- Operate heavy equipment within its design limits. Pushing the equipment past its limits leaves you at risk for injury and equipment damage.
- Don’t complete tasks outside the normal operation schedule unless it’s an emergency. If it’s an emergency, follow the right procedures.
- Involve the right personnel. For instance, only qualified technicians should operate a machine or undertake inspection and maintenance procedures.
- Improve operator safety training. OSHA has shown that you can reduce accidents by improving operator training.
- Keep down the speed in the operating environment. For example, you can use speed-limiting devices on forklifts. You can also use radar to detect speed.
- Install equipment monitoring and accountability systems that tie operators to their equipment. In case something goes wrong, you can employ maintenance troubleshooting techniques to determine the root cause of it and investigate ways to prevent it from happening again.
Working With Specialist Technologies
Electrical systems require specialized knowledge of electricity. The same is true for mechanical and hydraulics systems. A maintenance team might have to deal with technical, mechanical, hydraulic, and electrical systems in complicated operations. It’s more likely that one person may not have all the specialist knowledge required.
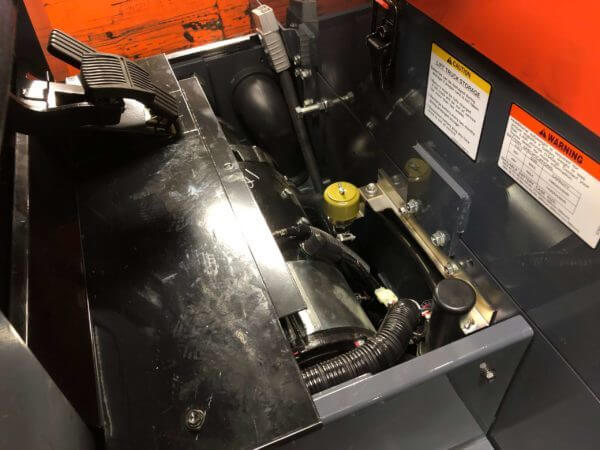
For example, a forklift uses a hydraulic system to raise and lower the forks. Electric forklifts operate on a battery, a series of controllers, and drive motors. Furthermore, forklifts are mechanical objects with wheel bearings, axles, and linkages. Each system requires specialist knowledge.
Even if you have an operations team, one person may not possess all that knowledge. So, in case of equipment downtime, you could potentially have two or three people with different technical knowledge bases working to solve problems on one piece of equipment. This can take time and increase equipment downtime.
Solutions
- Maintain specialty equipment in-house. But this is expensive, difficult to do (e.g., labor shortages), and may have a low return on investment.
- Outsource equipment maintenance to specialists. For example, Conger’s factory-trained and authorized technicians possess the electrical, mechanical, and hydraulic specialty knowledge to work on electric forklift trucks.
Maintaining Safety Standards
Maintenance teams have much higher-risk jobs than office workers do. Maintenance workers work with dangerous equipment almost daily.
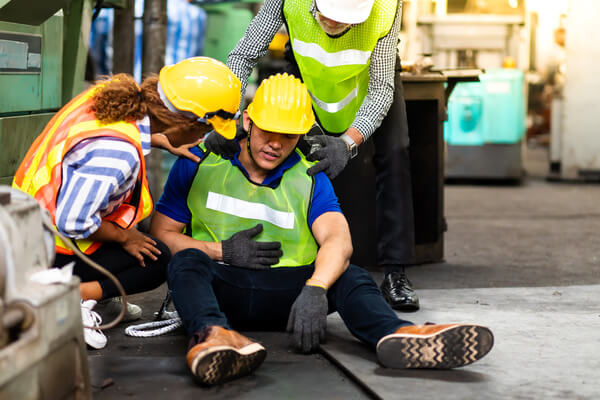
Employers have a legal and ethical obligation to protect workers from inherent dangers. But complying with OSHA’s standards can be a real challenge:
- Expensive or difficult to find PPE. For example, ensuring everyone wears the correct personal protective equipment (PPE) might be challenging because maintenance PPE can be expensive or difficult to find.
- Not following safety processes. Guarding against commonly known hazards, like falls, or ensuring that lock-out/tag-out (LOTO) procedures are followed to protect people from being injured or killed by energized equipment.
- Lack of or inadequate safety training. Workers may lack regular safety training to protect and guard against hazards and improve safety.
Solutions
Have a strong commitment to facility safety. This includes:
- Making safety a business-wide agenda.
- Provide safety equipment (PPE) for different work environments.
- Reinforce safety through meetings, notices, labels, and more.
- Material handling operation and safety.
- Manage worker stress and fatigue by providing workers with scheduled time off for rest and ensuring they take safety measures in changing forklift propane tanks.
- Mitigate electrical hazards. Ground all power supply systems, ensure sufficient clearance in front of electrical panels, and affix signage near electrical systems.
- Have a facility emergency plan outlining how to respond to emergencies, including exit options.
- Recruit emergency responders among workers.
You can read more about safety standards in our warehouse safety guide.
Frequently Asked Maintenance Questions
What Are the 4 Types of Maintenance?
The types of maintenance to choose from are:
- Corrective maintenance (breakdown maintenance).
- Preventive (scheduled) maintenance.
- Predictive maintenance.
- Condition-based maintenance.
What Are Some Examples of Maintenance Activities?
- Routine maintenance includes cleaning, lubrication, visual inspection, functional tests, oil tests, etc.
- Preventive maintenance activities, such as performing regular forklift inspection maintenance, prevent costly breakdown incidents from occurring.
- Installing a maintenance system on your equipment to predict maintenance needs and remind you in time.
- Replacement of equipment parts.
- Maintenance documentation in a maintenance log.
Why Is Maintenance Important?
Well-maintained equipment is less likely to break down, which leads to increased uptime, more working hours, fewer repair and maintenance costs, and increased revenue. Maintenance improves the equipment’s economic life, lifespan, and overall productivity.
What Are the Major Causes of Maintenance Problems?
The 5 common causes of equipment maintenance problems are:
- Improper equipment operation.
- Lack of knowledge or skill in equipment technology.
- Failure to perform or adhere to preventive maintenance.
- Disregarding continuous equipment inspection.
- Lack of equipment maintenance record keeping.
Conclusion
That’s it: 11 equipment maintenance issues and their solutions.