Blue Light on Forklift
Are you curious about enhancing safety in industrial environments? You are in the right place.
Welcome to our comprehensive guide on the role of blue lights on forklifts and their impact on workplace safety.
In this article, we will explore:
- The importance of forklift safety.
- Understanding warning lights.
- Blue lights on forklifts and their role in visibility.
- Navigating OSHA regulations.
- Additional safety measures.
- And More
Join us as we delve into forklift safety and the pivotal role of blue lights in fostering a secure work environment.
Let’s dive in!
Forklift Safety Concerns
Forklifts are powered small vehicles that lift and move heavy loads in industrial settings and expansive facilities. However, if not handled correctly, they can present some potential risks in the workplace.
Using new attachments, working in areas with poor ventilation, or operating on unstable ground can make forklifts even more risky.
According to the Occupational Safety and Health Administration (OSHA), forklift accidents happen more often, leading to severe injuries or even death. Some safety concerns may include collisions, overturns, tip-overs, or falls from a forklift.
Sadly, when these accidents occur, it is usually the driver who gets hurt or killed. To address these hazards, drivers must practice safe driving techniques and comply with safety protocols to remain secure.
Despite the power and functionality of forklifts to lift and move objects, they also come with risks. That is why it is crucial to comply with regulations and safety standards.
The Occupational Safety and Health Administration (OSHA) is a regulatory body that sets and enforces regulations and standards to protect the well-being of workers and minimize injuries.
Importance of Compliance with OSHA Regulations
Compliance with OSHA regulations is fundamental for maintaining a safe and healthy work environment for workers and forklift operators. OSHA defines specific guidelines and standards to protect workers and prevent accidents.
Another importance of complying with OSHA regulations is that it helps avoid accidents and injuries. The guidelines outline best practices for forklift operation, including training requirements, certification, equipment maintenance, and operational methods.
These regulations reduce the chances of accidents resulting from improper use, inadequate training, or negligence.
Blue Lights for Enhanced Safety
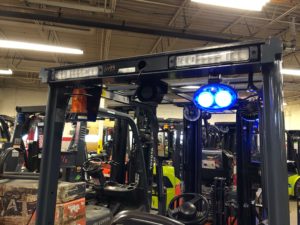
If you are a forklift driver, you may have seen these— blue lights. They are commonly known as ‘safety lights’ because their design enhances the safety of the area surrounding a forklift truck.
Blue lights are integrated into forklifts to enhance visibility and safety in busy work spaces. These lights emit a bright blue beam that projects onto the ground, alerting pedestrians and nearby workers to the presence of a forklift.
With their visual indicator, blue lights help reduce the risk of collisions, especially in places with limited visibility or high foot traffic.
Forklift Safety Basics
When operated by trained individuals, forklifts can contribute to the efficient handling of various items like boxes, crates, pallets, and more.
OSHA has set out specific requirements for ensuring the security of forklift operators.
OSHA Requirements for Forklift Operations
Here are some of the OSHA requirements when handling forklifts:
- Before operating a forklift, OSHA requires operators to receive training and certification.
- Forklifts must undergo regular inspections to identify any defects or malfunctions that could compromise safety. According to OSHA, operators should conduct a pre-shift inspection to check for visible damage or operational issues.
- Those operating forklifts must be aware of the load capacity of their equipment and adhere to it.
- OSHA regulations require operators to wear appropriate personal protective equipment, including high-visibility vests, hard hats, and safety shoes.
- Avoid driving lifts toward individuals who are sitting or standing nearby.
- Do not operate forklifts while standing or sitting in the work area.
- When navigating inclines or declines, forklift operators should keep a safe distance between their trucks and move at a reasonable speed.
Common Forklift Accidents and Their Impact
Forklift accidents can lead to devastating consequences. For this reason, operators must prioritize safety measures. So, what are the most common types of accidents? Let’s look at them and their impact:
1. Being Struck by Forklift
A forklift operator can unintentionally collide with a pedestrian or colleague. This accident type usually occurs when the operator becomes distracted or loses focus. Unsafe working conditions can restrict the ability of the driver to react on time and lead to such incidents.
2. Injury From Rollover or Forklift Tip-Over
Forklifts are heavy machines not built for sudden sharp turns. When operators attempt to make quick turns or exceed the load capacity, it can lead to the forklift tipping over, posing risks that can even be life-threatening.
3. Loads Falling from Forklift
When loads on a forklift are uneven or unbalanced, they can quickly shift and fall during movement, amounting to accidents or fatalities. Excessive speed while carrying a load can cause the load to tip over and fall.
To prevent such incidents from happening, ensure that loads are well centered on the forks and avoid excessive speed when transporting a pallet with a heavy load.
4. Mechanical Failures
Despite taking all the necessary precautions and following safety protocols, accidents occur because operator actions are just one aspect of the overall equation. The condition and maintenance of the forklift itself have to be effectively maintained and in good shape.
Mechanical malfunctions are a frequent cause of forklift accidents and personal injuries. Issues like leaky valves and hoses, worn-out or damaged tires, and faulty brakes can trigger accidents.
Therefore, quickly addressing mechanical problems is critical for stopping accidents before they happen and keeping forklift operators and those nearby safe. Forklifts are used frequently in busy environments, so maintaining safety while operating forklifts is paramount.
Overview of Forklift Safety Features
Equipping forklifts with the right features can reduce the risk of workplace accidents. But, forklift truck incidents are more prevalent than others in some environments. If you want to safeguard vehicles and drivers, it is worthwhile to go the extra mile.
The following are some of the best safety features for protecting against forklift accidents:
- Forklift seat belt: An operator should always wear the seatbelt that the manufacturer has installed on a forklift. Wearing a secured seatbelt can keep the driver safe in the case of an accident.
Additionally, adding an interlock system to many forklift models can enhance safety procedures, preventing the equipment from moving until the fastening of the seatbelt.
- Headlights: In dimly lit warehouses, LED or halogen headlights improve visibility for forklift drivers and pedestrians. These bulbs are long-lasting, simple to install, energy-efficient, and environmentally friendly.
-
- Proximity detection system: This system alerts the operator with audible and visual signals when the equipment gets close to objects or pedestrians within a specific range. The operator needs to check the functionality of this system as part of their daily inspection routine.
- Parking brake: Operators should engage in parking brakes every time they step out of the forklift, even if it is just for a short break. The parking brake is crucial for securing the forklift, especially when parked on a slope, to prevent unintended rolling or movement.
- Drive with a horn button: The rear-drive handle provides a secure hand placement for the operator inside the lift truck when they need to operate in reverse. The handle can be equipped with a horn button, enabling them to warn pedestrians and other equipment operators without having to turn around and press the horn on the steering wheel.
Understanding Warning Lights
Warning pedestrians about approaching forklifts is crucial to averting accidents and protecting lives. In warehouses, warning lights are highly effective in achieving this.
These warning lights guarantee the well-being of workers and those operating around forklifts. The following are some of the importance of warning lights:
- Visibility: Visibility limitations may exist for forklifts in busy work environments. Warning lights, such as strobe lights or flashing beacons, can boost the visibility of the forklift, making it easier for pedestrians, forklift operators, and workers to identify and recognize its presence. This action helps prevent collisions and accidents caused by a lack of awareness.
- Pedestrian awareness: These warning lights serve as a visual cue to pedestrians. They alert pedestrians to be careful of the presence of a forklift, allowing them to take appropriate precautions such as waiting for it to pass— lowering the risk of accidents and injuries.
- Clear communication: Warning lights communicate critical information to those around them. For example, a flashing red light may indicate that the forklift is carrying a heavy load and is about to reverse. This communication helps others anticipate the actions of the forklift and adjust their behaviors.
- Compliance with regulations: Most workplace safety regulations require warning lights on forklifts. Adhering to these regulations helps maintain a safe working environment, ensures compliance with legal requirements, and reduces the risk of penalties or fines.
While operating a forklift in reverse, operators should use the horn or alarm. Utilizing forklift warning lights is a good idea to extend safety measures. These lights come in various types, each designed to serve a specific purpose in promoting safety.
Different Types of Warning Lights
These are some of the different types of warning lights available for forklifts:
1. Blue Safety Lights
Blue safety lights, also known as blue spotlights, are installed on the overhead guard of a forklift. These lights project a concentrated blue beam onto the ground in front or behind the forklift. These lights create a visible boundary or warning zone, indicating to pedestrians or other forklift operators to keep a safe distance from the forklift.
Blue safety lights are very beneficial when navigating through narrow aisles because their distinct blue illumination grabs the attention of individuals nearby, alerting them of the forklift.
2. Red Safety Lights
Red safety lights are a visual reminder for pedestrians to maintain a safe distance. The light is mounted on the overhead guard and projects a red line, indicating that pedestrians should steer clear of the forklift. Red lights establish a designated no-go zone for both forklifts and pedestrians, minimizing the risk of accidents.
3. LED Lights
LED lights are energy-efficient and long-lasting. Whether used as headlights or taillights, LEDs provide bright illumination, improving visibility for the operator. They also help make the forklift more visible to others, decreasing the likelihood of collisions.
Halo zone
A halo zone refers to a scheduled area around a forklift that is marked by a visual indicator, such as a painted line or striping.
The halo zone creates a unique separation between pedestrians and forklifts. It creates a visible boundary, reminding pedestrians to maintain a safe distance from the forklift. This separation lowers the chances of accidents and injuries.
While halo zones improve visibility and alertness, they are even better when working with warning lights or audible alarms. When these measures are combined, the halo zone encourages a safer work environment.
Moreover, a halo zone can minimize the risk of collisions, play the role of a visual guide for pedestrians, and promote pedestrian safety in forklift operations areas.
Blue Light on Forklifts
In industrial areas and warehouses, workers may face multiple risks daily, and even the slightest amount of carelessness can result in terrible injuries or even loss of life. Emphasizing workplace safety with blue lights can guarantee the security of workers in busy operational areas.
Purpose and Benefits of Blue Safety Lights
Blue safety lights on the front or back of a lift truck serve as a warning sign for pedestrians, alerting them of the presence and speed of a coming forklift.
These spotlights emit a powerful blue light that projects approximately eight feet in front of or behind the forklift, depending on the placement of the light.
The visual cue helps pedestrians gauge the proximity and movement of the forklift, empowering them to take actionable precautions and ensure their safety.
Although forklifts usually operate at a moderate pace, they can sometimes accelerate when not carrying any loads. This sudden increase in speed makes it difficult for machines to come to an abrupt stop if they encounter a pedestrian in their surroundings.
By providing forklifts with blue safety lights, pedestrians can receive warnings and take evasive actions to avoid the path or the forklift and stop accidents.
Blue safety lights can promote safety and productivity in workplaces. Even a minor forklift incident can disrupt operations and contribute to financial losses. Hence, it is vital to install blue safety lights as a safety measure to stop accidents and bolster a smooth workflow.
Blue lights mounted on forklifts project a beam of blue light onto the ground, creating a visible coverage area. The exact projection and coverage may change depending on the type of blue light used and its position on the forklift.
Projection and Coverage of Blue Lights
Generally, the blue lights project a focused beam intended to extend a certain distance in front of or behind the forklift. This coverage area typically spans several feet, offering a clear visual indication to pedestrians and nearby workers, usually around eight to ten feet in distance.
The primary purpose of this projection is to establish a visible boundary or safety zone around the forklift. This visible boundary goes a long way in alerting individuals about approaching forklifts and helping them maintain a safe distance.
Despite the tremendous benefits of blue safety lights, they must operate within defined regulations. That is where OSHA comes in. Their goal is to ensure employee safety and healthy working conditions. It enforces a couple of safety regulations regarding the use of forklifts. Installing blue safety lights is a thoughtful idea for any organization that uses forklifts.
OSHA Regulations Related to Blue Safety Lights on Forklifts
In addition, OSHA is committed to ensuring the well-being and safety of employees in the workplace. Since OSHA does not have specific regulations solely focused on blue safety lights, it has emphasized several regulations when using forklifts;
1. Headlight Usage
As stated by OSHA regulation 1910.178(h)(2), it is required to use headlights on forklifts once the lighting conditions in the workspace drop below 2 lumens per square foot. This requirement is crucial, particularly during nighttime operations or when obstacles impact visibility.
Having adequate illumination not only improves the productivity of the forklift operator but also fulfills the visibility requirements of various individuals. For example, older operators might require more light to operate a forklift safely.
2. Tail/Brake Lights
Another OSHA requirement outlined in its forklift safety rules is the inclusion of tail/brake lights, which are typically already built into forklifts. These lights boost visibility and decrease the probability of accidents in crowded work environments.
While not mandatory for forklifts operating in less congested areas, OSHA strongly recommends installing them on forklifts that operate in high-traffic zones with numerous pedestrians. With tail/brake lights in place, employers can increase the safety measures for their forklift operations and lessen the risk of collisions or accidents.
3. Lights and Horns Requirement
Under the OSHA requirement, forklifts must be equipped with lights and horns when workplace conditions require them. This requirement ensures that audible and visual warnings are readily available to prevent potential hazards and promote safety.
Additional Safety Measures
In industrial settings where forklifts and pedestrians cross paths, safety is not just a factor; forklift safety is necessary. The consequences of accidents in these hectic environments can be detrimental.
In an environment where even the slightest mistake can lead to serious injury, it is crucial to have the most advanced and accurate forklift pedestrian safety system ready for your team.
Ensures consistent security is prioritized in your operations, offering your team the protection they desire at every step with a reliable and effective proximity detection system.
Detection Systems for Forklifts
Proximity detection systems utilize advanced technology, such as sensors and alarms, to detect the presence of pedestrians or other vehicles near the forklift. Once the system detects a person or object within a specified range of the forklift, it activates an audible or visual warning to alert the operator.
These detection systems help to turn down accidents by providing real-time awareness of collisions and enabling the operator to take quick action. They are essential in busy work environments with a high risk of interactions between forklifts, pedestrians, or other vehicles.
Forklift Pre-Check Procedures
Before using a forklift, first conduct pre-check procedures to ensure safety. These procedures involve a series of checks and inspections to verify that the forklift is in better working order and ready for operation.
Here are some specific steps to take in the pre-check procedures for forklifts:
- Visual inspection: Operators should inspect the forklift for any visible signs of damage, such as leaks or worn-out tires.
- Fluid levels: Ensure the fuel, oil, and coolant are at the recommended levels.
- Battery: For electric forklifts, operators should inspect the battery for any visible damage, leaks, loose connections, or charge level.
- Controls and gauges: To ensure accuracy, operators should test all the controls, such as the steering wheel, brakes, accelerator, horn, gauges, and indicators.
- Safety features: Forklift operators should also inspect and test the forklift safety features like seat belts, lights (headlights, brake lights), and backup alarms.
Incorporating LED Lamps for Better Visibility
Most forklifts are now incorporated with LED lamps to strengthen visibility and safety. These lamps offer many advantages over traditional lighting.
LED lamps produce bright and intense illumination that boosts visibility under various lighting conditions. Their focused lighting makes it easier for operators to see their surroundings and lowers the possibility of accidents.
LED lamps are energy efficient, consuming less power compared to conventional bulbs. Because of their efficient energy provision, costs are reduced and put less strain on the electrical system.
With a longer lifespan than traditional bulbs, LED lamps require fewer replacements, saving time and money on maintenance.
These lamps are highly durable and resistant to shocks and vibrations, making them well-suited for the demanding operating conditions of forklifts. They can withstand rough handling and are less likely to break— providing dependable lighting for extended periods.
Unlike traditional bulbs that require warm-up time, LED lamps provide instant brightness. With LEDs, operators have immediate visibility when the forklift starts or when transitioning between areas with varying lighting conditions.
Workplace Safety Practices
Safety culture means the collective beliefs, attitudes, and values of employees in the place of work. Creating a conducive environment for working is one way of dealing with accidents involving forklifts and achieving operational excellence.
Importance of Fostering a Safety Culture
A positive safety culture fosters an environment where employees actively prioritize safety, report any potential hazards, and participate in safety initiatives. This collective commitment to safety helps to decrease the accidents associated with forklifts.
Developing a safety culture starts with leadership. The management should demonstrate dedication to safety by investing in training, maintaining equipment, and implementing safety programs. Leaders must model safe behaviors and hold themselves and others accountable for maintaining a safe work environment.
A culture that prioritizes safety reduces workplace accidents, injuries, or fatalities. Forklift accidents can cause damage, bringing about human suffering and financial losses. Industries should work to protect their employees, reduce accidents, and improve productivity.
Putting safety first does not just promote well-being—it also has a positive impact on productivity. When employees feel safe and secure in their work environment, they develop a sense of trust and confidence. As a result, they are more likely to be fully engaged and effective in their tasks.
Training for Forklift Operators
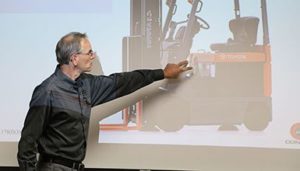
OSHA mandates that for operators to maintain safety, they should first obtain appropriate forklift training. Operators wishing to further their skills can enroll in an in-person or online course that aligns with OSHA standards.
Enrolling in training equips the operators with the knowledge and skills needed to operate forklifts properly.
Many individuals opt for online forklift training as it allows them to enhance their careers at their convenience. With that said, let’s explore the components of forklift operator training:
- Classroom instruction: Training begins with classroom instruction, where operators learn about the principles of forklift operation, safety regulations, and best practices. They learn about load handling, stability, maneuvering techniques, and interpreting warning signs and symbols.
- Practical training: Hands-on training for forklift operators is crucial to acquire the necessary skills. It involves handling a forklift under the guidance of a qualified instructor. Operators practice basic maneuvers, such as starting, stopping, turning, and reversing. They also learn how to handle loads, stack and unstack materials, and ways to operate in confined spaces.
- Safety procedures: Forklift operator training emphasizes safety procedures and protocols. Operators learn to conduct pre-shift inspections, identify risks, and respond to emergencies. They receive training on seat belts, mirrors, and horns, maintaining visibility, and avoiding distractions while operating the forklift.
- Load handling techniques: During training, operators learn proper techniques for handling various load types. This training includes understanding load capacities, securing loads using appropriate methods (e.g., pallet usage, straps, or attachments), and ensuring proper weight distribution for stability and balance.
- Refresher training: Regular refresher training is essential for reinforcing knowledge and skills, addressing any issues or changes in regulations, and ensuring continuous improvement in safe forklift operations.
Promoting Pedestrian Safety in the Workplace
Where forklifts are involved, pedestrian safety is a necessity. Dealing with a forklift that weighs over 10,000 pounds can be a huge responsibility that requires careful attention.
Safeguarding the safety of pedestrians starts by establishing appropriate safety methods and educating forklift operators on safe practices.
Below are some practical methods and strategies that you can implement to promote pedestrian safety in the workplace.
1. Giving Way to Pedestrians
As outlined by OSHA, forklift drivers are required to yield the right of way to pedestrians. Establishing this principle lays a strong foundation for warehouse pedestrian safety, promoting cautious navigation by operators and encouraging vigilance for the presence of pedestrians.
2. Be Cautious When Moving Around the Workplace
As mentioned earlier, pedestrians have the right of way in the workplace. However, this does not mean that they should now assume that every forklift operator sees them. While operators should exercise caution at all times, distractions can still occur, potentially jeopardizing the safety of forklift operations.
Imagine a pedestrian crossing the street. Even if the crosswalk signal indicates it is safe to cross, the pedestrian should still look both ways before proceeding. There is always a possibility that a driver might not notice the crosswalk.
Some drivers may turn right at a red light without checking or even drive through the intersection without stopping at the light.
The same principle applies to your workplace as well. Pedestrian safety in the warehouse not only relies on the attentiveness of the forklift operator but also the awareness and caution of the pedestrians themselves.
3. Regularly Utilize Forklift Hand Signals
Design clear hand signals for effective communication between forklift operators and pedestrians. For instance, a pedestrian can point in the direction they plan to walk when they spot a forklift, while a forklift operator can use hand gestures to indicate the direction of a turn. Employing these hand signals can enhance transparency in the workplace through employing these hand signals. Doing this helps in ensuring better communication and understanding between operators and pedestrians.
Lack of communication can lead to injury and death when handling equipment. But, you can avoid injuries by training your employees on forklift hand signals.
Miscommunication, especially when it involves material handling equipment, can have dire consequences, including accidents and fatalities. To protect pedestrian safety in the workplace, provide thorough training on forklift hand signals to mitigate such risks.
4. Operators Should Comply With OSHA Laws
To ensure the safety of both forklift operators and pedestrians, OSHA has established guidelines for forklift driving safety. Everyone in your workplace must comprehend and adhere to these guidelines.
Make it a routine to have regular safety discussions with your employees concerning forklift safety. Use this opportunity to remind them of the established guidelines.
Consider creating flyers or cheat sheets to display throughout the facility as quick and handy reminders for everyone.
5. Mark Walkways for Smooth Traffic Flow
Floor markings can be an ideal safety navigation. OSHA standards emphasize the importance of marking permanent aisles and passageways. Use a tape way to indicate the designated path for navigation throughout the facility. To avoid confusion, consider blocking off areas that forklift operators should not access.
6. Create Hazard Audio Indicators
Leveraging forklift hand signals to ensure pedestrians’ safety requires additional measures. In noisy work environments, audible warnings can be more efficient. If you’re unsure about the specific areas or situations that need audible warnings, seek feedback immediately.
Additionally, pedestrians should ask about the areas where they feel the least safe and voice their suggestions on how to address and improve those concerns.
Conclusion
Forklifts are compact, engine-powered vehicles commonly utilized for lifting and transporting heavy loads. However, failure to handle them with care can amount to huge risks.
The Occupational Safety and Health Administration states that most forklift accidents lead to collisions, overturns, tip-overs, or falls.
OSHA establishes and enforces regulations and standards aimed at safeguarding the welfare of workers and reducing risks.
Improving forklift safety is significantly enhanced by incorporating blue lights, which are purpose-built to enhance visibility and alertness in the workplace.
When turned on, these lights emit a strong and clear beam, serving as a visual indication of a forklift’s presence.
By prioritizing safety measures, businesses not only safeguard their employees but also maintain their reputations, reduce liabilities, and enhance operational efficiency.
Remember, prioritizing workplace safety is a responsible and morally imperative choice that businesses should never underestimate.