This is the complete guide to forklift forks.
We’ve put together everything you need to know about them, including:
-
What the standard forklift fork dimensions are
-
How forks are classified
-
The different types of forklift forks
-
How to inspect forklift forks
Let’s dive in!
Quick Summary
Don’t have time to read the entire article? Here’s a quick summary of the main points:
- The 3 main forklift fork dimensions are thickness, width, and length. Forklift fork sizes are also expressed in the same way (T x W x L)
- One of the most common forklift fork sizes is 1 1/2″ x 4″ x 42″
- Common fork thicknesses include 1 3/4″, 2″, and 2 1/2″
- Common fork widths include 5″ and 6″
- A standard forklift fork length is 42 inches, with 48-inch forks also common
- Forks can be categorized by ITA class, which corresponds to the distance between the bottom of the carriage fork bar and the top bar where the fork hooks mount. There 5 ITA forklift carriage classes
- Forklift forks are made from high-strength alloy steel and are heat-treated to improve their toughness (ability to absorb energy) and hardness (ability to resist indentation)
- There are dozens of different forklift fork types. Some include shaft-mounted forks, lumber forks, drum forks, scale forks, gypsum forks, and spark-resistant forks
- Forklift forks should reach at least 2/3 of the way into the load
- Replace forklift forks once they’re 10% worn
- Check forks before every use to ensure they’re in compliance with OSHA, ANSI’s guidelines, and any other relevant safety standards
- Inspecting forks should include measuring the blade wear, hook wear, straightness, angle, and tip level. You should also inspect for cracks, the locking hardware integrity, and for the presence and legibility of fork markings
What Are the Dimensions of Forklift Forks?
Thickness, Width, and Length: The Main Dimensions
Forklift fork dimensions are expressed in the order of thickness (T) x width (W) x length (L).
For example, 1 ½” x 4″ x 42″ forks are a common forklift fork size.
Thickness (T)
A forklift’s fork thickness can be measured along the shank.
What is a fork shank?
Also called the “shaft,” a fork shank is the vertical part of the fork.
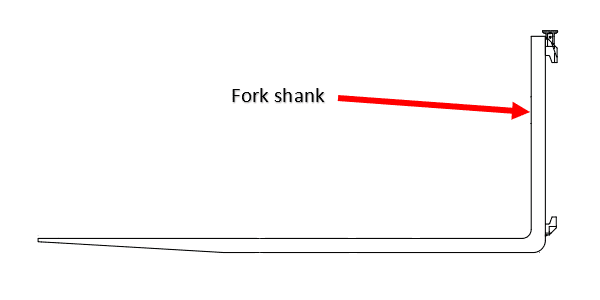
A shank has 4 surfaces:
- Front face: The part that makes contact with the load
- Top: The top surface
- Left flank: The left side of the shank
- Right flank: The right side of the shank
How Thick Are the Forks on a Forklift?
The most common forklift fork thickness is 1 ½ inches.
Other common fork thicknesses include:
- 1 ¾”
- 2″
- 2 ½”
Choosing the proper fork thickness comes down to the forklift’s capacity and the amount of weight it’ll be lifting.
Additionally, you can go thicker or thinner to compensate for more or less fork width to accommodate different loads.
For example, if you can only use 4-inch wide forks but need to maintain a higher weight capacity, you can increase the fork thickness.
Width (W)
Width is the measure of the fork along the shank face or blade at its widest point.
How Wide Are Forklift Forks?
The width of a forklift fork depends on its class.
For Class II forks, the standard forklift fork width is usually 4 inches.
Other fork widths include:
- 5 inches (Class III)
- 6 inches (Class IV)
Some jobs may need wider or narrower forks depending on the application.
How Wide Are Telehandler Forks?
The width of a telehandler fork depends on its capacity and model.
A 5,500 lb. capacity Genie telehandler (one of the most common models) uses 4-inch wide forks, in both heavy-duty and pallet fork styles.
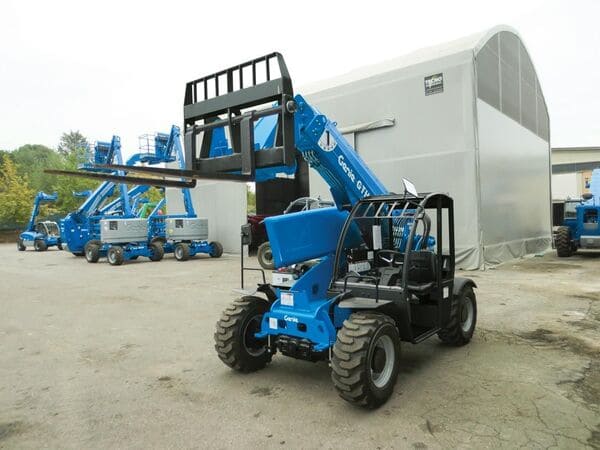
A 10,000 lb. capacity JLG telehandler (a common model in construction) uses 4-, 5-, or 6-inch pallet forks and 6- or 7-inch lumber forks.
Length (L)
A fork’s length is measured along the fork blade from the fork tip to the shank face.
What are forklift blades?
The forklift blade is the horizontal part of the fork that supports the load.
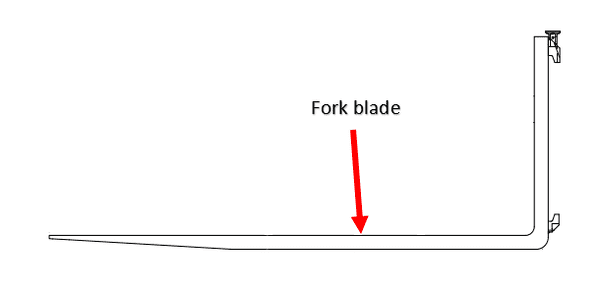
The blade has 4 parts:
- The upper face
- The bottom face
- Left flank (left side of the blade)
- Right flank (right side of the blade)
At the end of the fork blade is the fork tip.
This is the pointed part opposite the shank that first enters the load.
Tip flanks (also called “toe flanks”) are the sides of the tips and come in several styles:
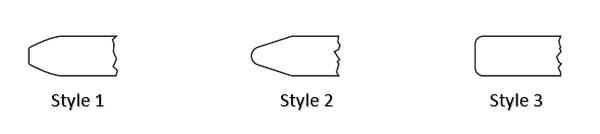
- Flat tip with slanted sides: This is the most common fork tip style for forks up to 7-inches wide
- Pointed tip: This tip is seen in block forks
- Flat tip: This tip is seen on forks 7-inches or wider
How Long Are Forks on a Forklift?
A standard forklift fork length is 42 inches (for both Class 2 and Class 3).
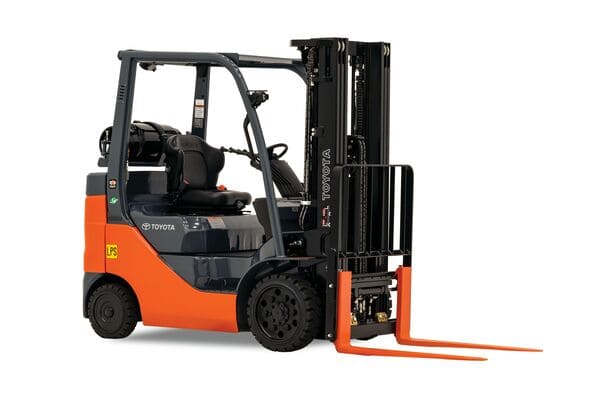
This allows them to fit into standard-size pallets without sticking through the back.
But 48 inch forklift forks are becoming increasingly common.
Also, 60-inch and 72-inch forklift forks are popular because of their long reach.
And finally, there are 96-inch and 120-inch forklift forks.
These are the longest forks you’ll see and are generally reserved for high-capacity (15,000 lbs.+) forklifts.
Forklift Fork Class Sizes: Another Key Dimension
Are All Forklift Forks the Same?
Yes and no.
Yes, because forks are designed to be interchangeable between different forklifts regardless of the manufacturer.
No, because forks must match the lift truck’s lifting capacity.
For example, you can’t use forks for a 3,000 lb. capacity forklift on a 6,000 lb. capacity forklift.
So this brings up the question:
How Do You Classify Forks?
The most basic way to classify forklift forks is by referring to the ITA carriage class.
What Is an ITA Carriage?
It’s any one of 5 forklift carriages with a standardized height between the bottom of the carriage fork bar and the top bar.
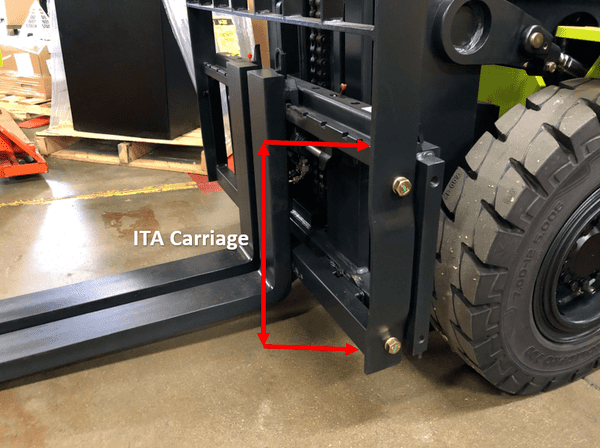
The ITA carriage size corresponds to ITA forks.
What Are ITA Forks?
Also called “clip” and “hook” type forks, ITA forks are the industry standard for forklift forks and the most common type.
These forks are designed to hang on the forklift carriage with opposing top and bottom “hooks” that engage the lower and upper carriage fork bars.
Fork Hooks: What You Need to Know
Fork hooks, also called “clips” or “hangers,” are the most common way of mounting forklift forks on ITA-style carriages.
They’re designed with an L-shape to hold the forks onto the carriage.
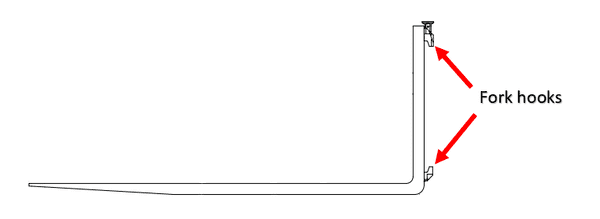
Hooks are usually welded to the back of the shank and have 2 faces:
- Retaining face: This is the inclined part inside the hook
- Suspension face: This is the outer part that sits on the carriage bar
How do these forks mount on a forklift carriage exactly?
The top hook hangs onto the top bar of the carriage and the bottom hook enters the carriage through a cutout in the bottom center.
Then, you slide each fork over to one side to complete the installation.
The distance between each hook corresponds to the distance between the top and bottom carriage fork bars.
Thus, what you have between ITA forks and an ITA carriage is a standardized measurement that allows forks to be interchangeable between various forklift manufacturers and models.
What Are the Classes of Forklift Forks?
The ITA carriage size is used to determine fork classes.
You’ll commonly see a fork’s class size noted following the measurements.
For example, 1 ½” x 4″ x 42″ Class II forks are a common size for 3,000 lb. capacity forklifts.
There are 5 forklift fork classes, which are classified by the carriage height and the forklift’s rated capacity.
Let’s go through each.
ITA Class 1 Forklift Forks
- Carriage height: 13-inches
- Forklift capacity: Less than 2,200 lb.
ITA Class 2 Forklift Forks
- Carriage height: 16-inches
- Forklift capacity: 2,200 to 5,500 lb.
ITA Class 3 Forklift Forks
- Carriage height: 20-inches
- Forklift capacity: 5,500 to 10,998 lb.
ITA Class 4 Forklift Forks
- Carriage height: 25-inches
- Forklift capacity: 11,000 to 17,600 lb.
ITA Class 5 Forklift Forks
- Carriage height: 28.66-inches
- Forklift capacity: 17,602 to 24,198 lb.
Forklifts with lifting capacities greater than 25,000 lb. tend to have shaft-style forks, which are different from ITA forks.
We’ll cover shaft-mounted forks in an upcoming section.
Forklift Fork Class Versions
Forklift fork classes can be further subdivided into versions “A” and “B.”
For example, for each class, there can be:
- 1A and 1B
- 2A and 2B
- 3 A and 3B
- 4A and 4B
- 5A and 5B
Each fork version is defined by the fork drop, which is the distance between the top of the bottom hook and the floor.
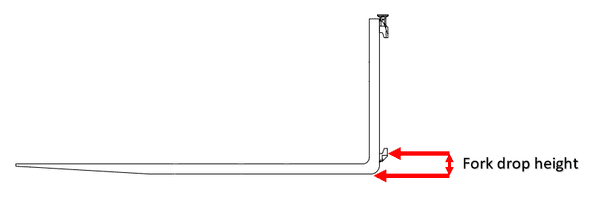
These types of forks are uncommon and most often found on articulating forklifts such as Flexi’s.
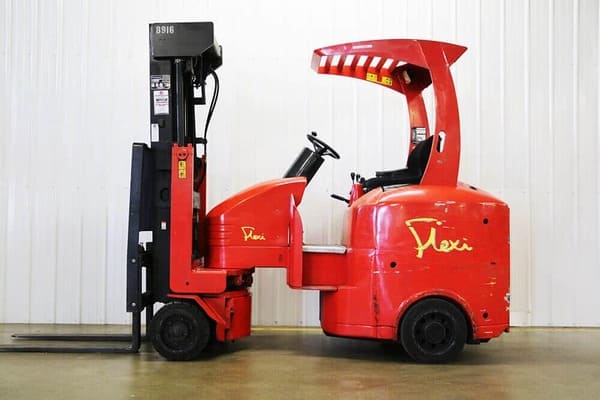
Other Forklift Fork Measurements
Besides the measurements we’ve talked about already, there are additional fork measurements to be aware of:
- Back Height: Distance from the top of the shank to the bottom of the blade
- Blade Length: Distance from the shank face to the tip
- Cross Section: Width multiplied by the thickness
- Angle: Measurement from the shank face to the upper blade face
Forklift Fork Terms & Measurements
How to Measure Forklift Forks
How do I identify a forklift fork?
You can identify forks by taking their measurements.
So, how are pallet forks measured?
Using a tape measure and 4 simple steps:
- Get the fork thickness by measuring from the shank back to the shank face
- Get the fork width by measuring across the shank from flank to flank
- Get the fork length by measuring from the shank face to the fork tip
- Get the fork/carriage class by measuring from the inside bottom of the upper fork hook to the inside top of the lower fork hook
Now, put it all together to get the full measurement (T x W x L + Class).
How Forklift Forks Are Made
Manufacturing forklift forks involves various materials and metalworking processes.
Let’s go through what’s all involved.
Forklift Fork Materials
What material are forklift forks made out of?
Forklift forks are made from high-strength alloy steel.
And what kind of steel are forklift forks made out of?
Answer: Chrome-manganese steel.
Other steel alloys include:
- 1045 to 1060 steel
- 4140 or 4340 steel
- A572 Grade 50 steel
These types of steel are preferred due to their toughness and ability to maintain a high tensile strength during forging.
The Forklift Fork Manufacturing Process
You can watch the whole process (for Bolzoni forks) below:
The main steps in the fork manufacturing process are:
- A single piece of high-strength steel is selected
- Saws or torches cut the piece down to size
- A stamp marks the fork with manufacturing data
- If tapered, the taper is created next
- The steel is heated and bent to create the blade, heel, and shank
- Hooks are welded onto the back of the shank
- The forks are dipped in an oil bath to improve hardness
- A “shot blast” procedure reheats the forks
- The forks are paired up
- The forks are inspected for manufacturing flaws
- The forks are painted
- The forks are fitted with a pin kit
- The finished forks are palletized for shipping
Forklift Fork Lock Pins
Lock pins also called “positioning pins,” “locking pins,” “latch pins,” or “pin assembly” are designed for fitting each fork into a particular spot on the carriage.
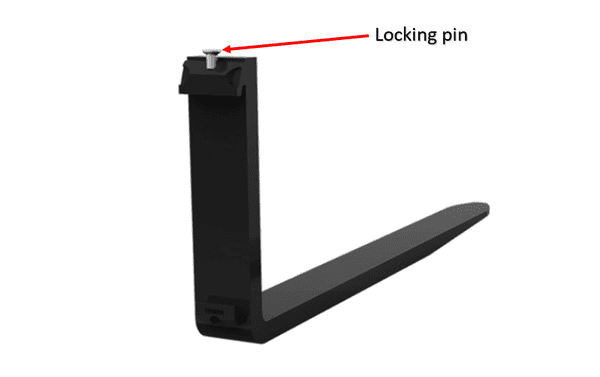
There are 2 types of pins:
- Button pins: Also called “mushroom” pins
- Latch pins: Also called “lever” pins
Once the forks are hooked onto the carriage, the pins on each fork lock the fork into place using the notches on top of the carriage bar.
This helps to prevent the forks from shifting and from losing the load.
Other Questions About the Forklift Manufacturing Process
Are Forklift Forks Heat-Treated?
Forklift forks are heat-treated to increase the forks’ toughness, which is their ability to absorb energy without fracturing.
Are Pallet Forks Hardened?
The heat-treatment process also improves the forks’ hardness, which is their ability to resist indentation and abrasion.
Types of Forklift Forks
There are dozens of forklift fork types depending on applications, forklift type, and the loads handled.
Let’s go through some of them.
Shaft-Mounted Forks
We’ve said that ITA forks are the most common type of fork style.
Shaft-mounted forks are a different style from ITA forks in both their design and application.
Whereas ITA forks use top and bottom hooks to mount on the carriage, shaft-mounted forks consist of a collar mounted to the top of the shank.
The collar attaches to the lift truck with a long shaft that connects to both sides of the carriage.
Shaft-style forklift forks are commonly found on:
- Forklifts with fork positioners
- Older forklifts
- High-capacity forklifts
- Skid steers
- Telehandlers
Some of the types of forks covered below are shaft-style, while others are ITA-style.
Block Forks
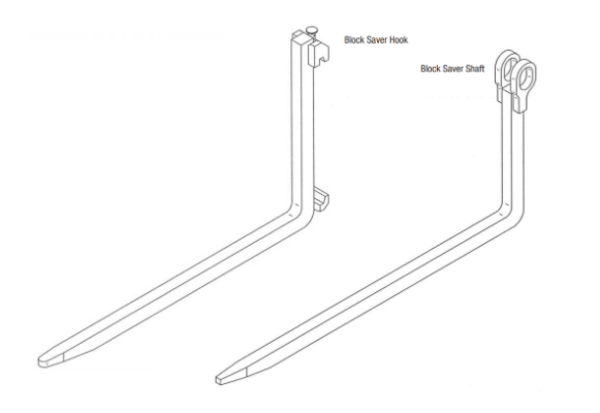
Block forks are very thin with an enlarged heel for more strength.
They’re used for lifting concrete and cement blocks and are available in different hook/mounting styles.
Lumber Forks
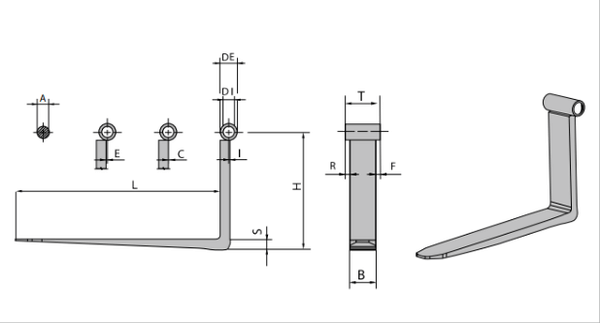
What are lumber forks?
Lumber forks for forklifts have wide, thin blades used for getting underneath lumber and boards without damaging them.
They’re especially useful for “scooping” un-palletized loads directly off of the ground.
Drum Forks
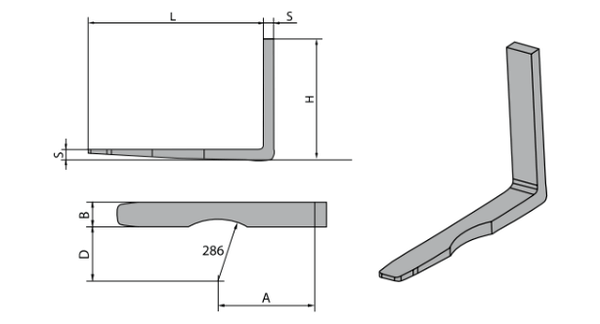
Drum handling forks are used to lift barrels – either the standard 55-gallon types or custom-sized barrels.
They have a contour cut out on the blades that fit around the barrel.
Depending on the application, they can lift 1 or 2 drums at a time.
They also have the advantage of being multipurpose, as the forks can be used to lift regular pallets too.
Telescopic Forks
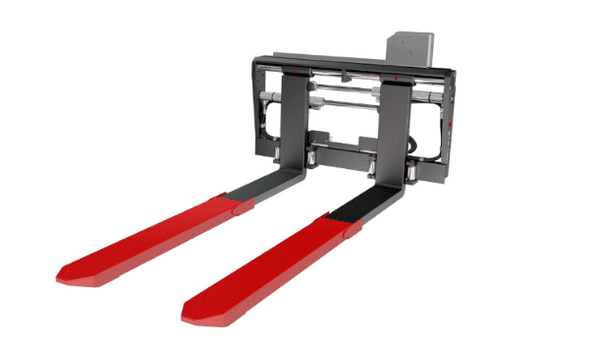
These are high-tech alternatives to fork extensions.
They use hydraulics to extend an outer fork shell that fits over the inner fork, extending the lift truck’s reach.
And after use, they can retract back to normal fork size.
Scale Forks
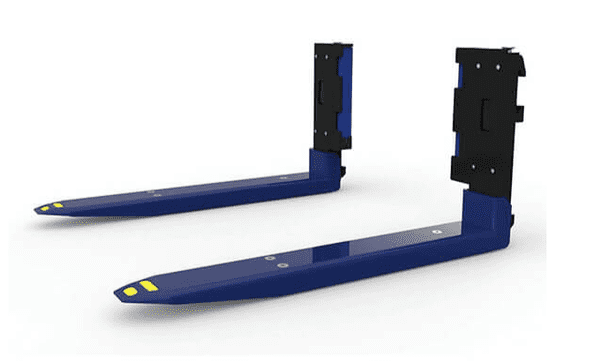
Scale forks are designed to allow operators to weigh loads without having to stop at a scale.
Cascade weigh forks, for instance, use integrated Bluetooth technology to transmit the load’s weight to an LCD screen that the operator can read.
They’re commonly used for tasks such as incoming goods control, dosing, filling, and overload prevention.
Bolt-On Forks
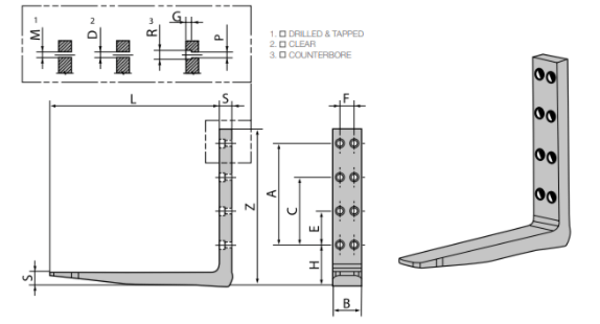
These are rare and normally used on large forklift trucks.
Holes in the shank allow the forks to be bolted onto the fork carriage, instead of being hung using hooks or a tube.
They’re best for handling loads that are all the same size since the forks can’t be moved around once installed.
Coil Forks
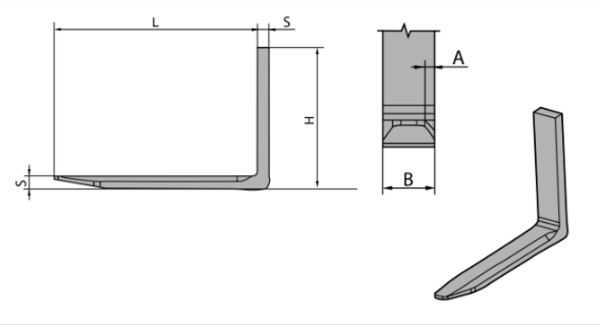
Coil forks are designed to straddle steel coils, concrete piles, reels, wire rolls, sheet polythene, and paper rolls.
They feature a chamfer or radius on the inner or outer blade flanks to cradle rounded loads.
The radius or chamfer can be customized to fit particular loads.
Tire Forks
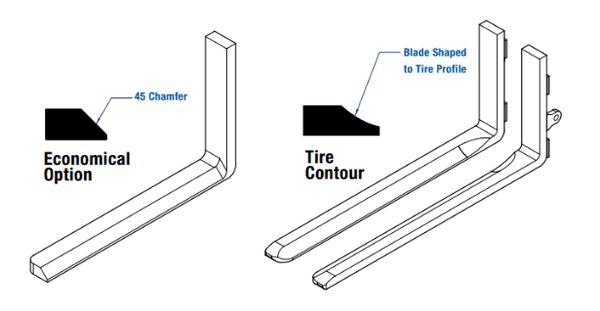
Tire forks are like coil forks but are specially designed to carry tires of different shapes and sizes without damaging them.
They accomplish this by using either a chamfer or custom contour on the top inside of the blade to cradle the tire.
Corrugated Forks
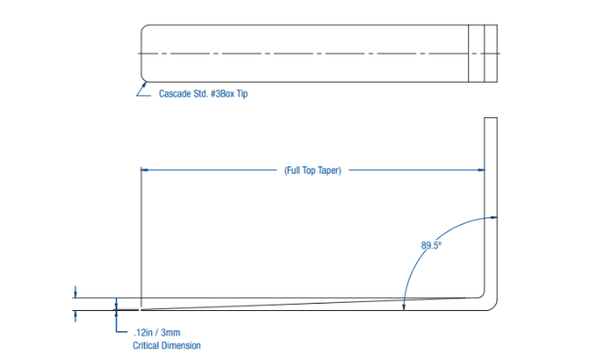
Also called “box tip” forks, these are tapered forks with a very thin 3 mm tip.
They’re used to get under and lift thin materials such as corrugated sheets, cardboard boxes, and steel sheets up from flat surfaces.
They have a polished and fully-top-tapered blade, which allows for a gradual transition in thickness.
Offset and Inset Forks

Offset forks are designed to go wider than the fork carriage.
Inset forks are the exact opposite – they go narrower than the fork carriage.
How wide or narrow they go can be customized based on the application.
Peek-a-Boo (PAB) Forks
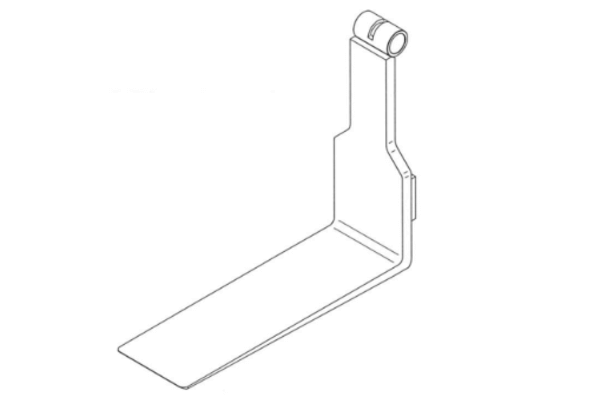
Peek-a-boo forks are designed to allow for better operator visibility – mostly in the lumber industry.
They have a wide, thin blade (less than 50 mm thick) and a shank width that reduces towards the top.
Because of this design, less shank material is in the way of the operator’s vision.
Quick-Detach Forks
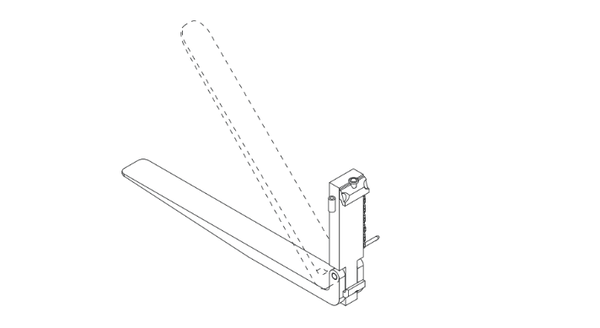
Quick detach (QD) forks are designed to be quickly and easily detached and removed from the carriage.
Their key feature is an open upper hook or lower pin-release-style hook that allows for attaching and removing the forks without having to lift them off the carriage bar.
They’re best for applications that require frequent detaching or switching of the forks without incurring downtime.
Folding Forks
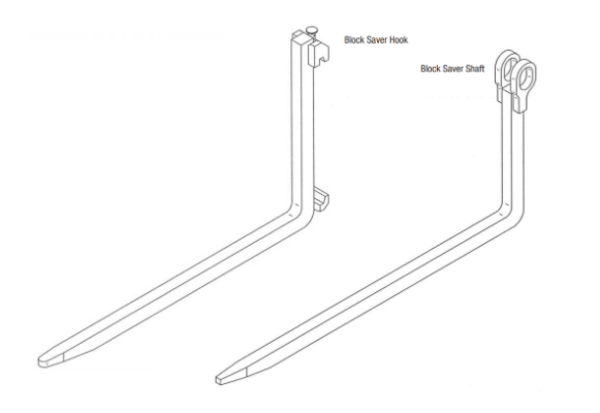
These forks have a hinge near the heel that enables the fork to fold up.
Additionally, there’s a chain and pin that secures the fork vertically in place.
They’re most useful for forklifts that are used in confined spaces or frequently transported via truck and trailer.
Gypsum Forks

These are designed with product protection in mind to handle sensitive gypsum and other wallboards.
They use a replaceable polyurethane or neoprene pad that covers the shank.
This pad won’t mark, dirty, or damage the wallboard.
Furthermore, the blade is polished, all sharp corners are removed, and the heel is squared – all to prevent damage.
Tip Plate Forks
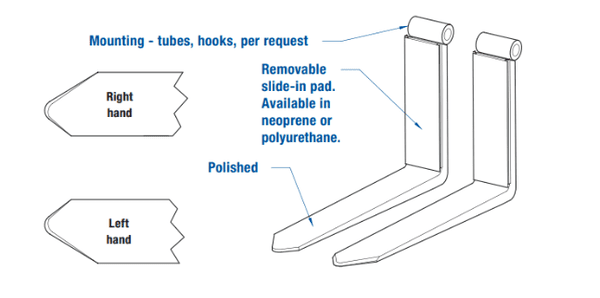
These are designed primarily for loading metal sheets in tin can-forming plants.
Their tapered and offset tips allow for easier entry into small skids, and their polished blades reduce resistance.
Additionally, a replaceable polyurethane or neoprene shank pad prevents the dimpling of metal sheets.
Anti-Slip Forks
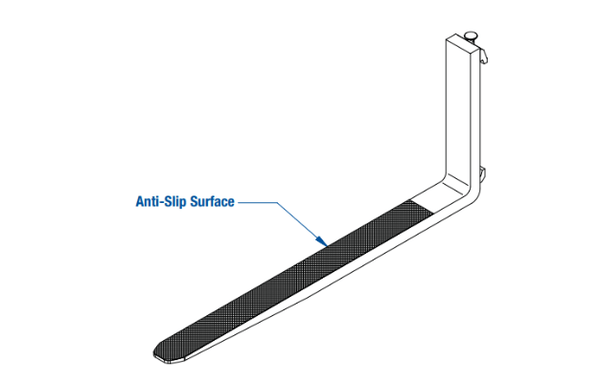
Anti-slip forks are primarily used to handle plastic pallets and cold storage loads.
But they can also be used for general applications, including handling wooden pallets.
What makes them anti-slip?
They have an abrasive metal surface on the top of the blade that grips the load and prevents it from coming off the forks while moving, stopping, or changing direction.
Spark-Resistant Forks
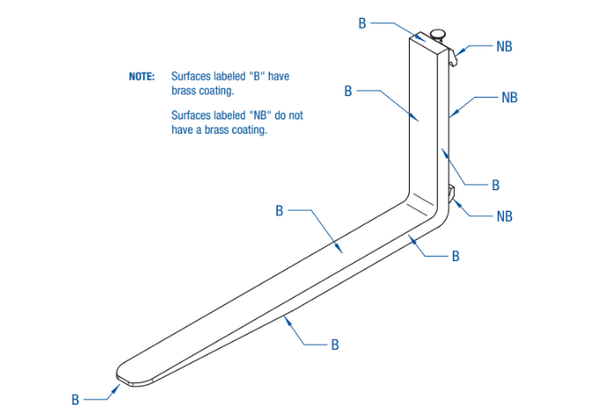
Also called “spark-retardant” forks, these are designed to work in environments at risk of explosions like grain mills, chemical plants, and munitions factories.
Their blade, shank face, and flanks have a brass cladding that prevents sparking if the forks collide with another metal.
Stainless Steel Forks
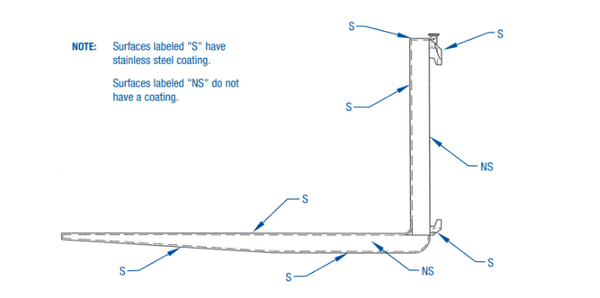
These are used in wet environments, like food, beverage, pharmaceutical, and chemical applications.
The main benefits of stainless steel forks are:
- Resistant to corrosion
- Bacteria-resistant
- Easy to clean
Rotator Forks
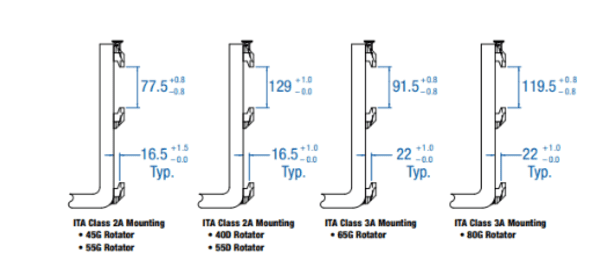
Rotator forks fit on a rotator attachment, which can invert the forks and tip loads into other containers.
For example, apple orchards use them to dump bins of apples into hoppers.
They’re basically regular forks, but with an extra hook installed upside-down just under the top hook.
Roller Forks
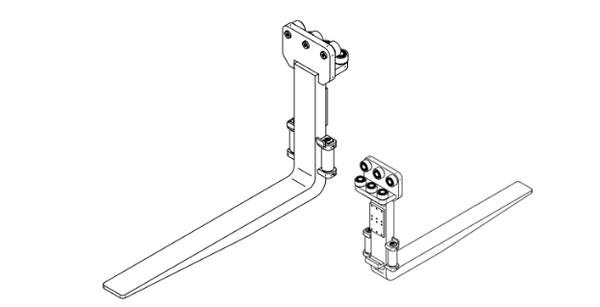
These are special forks designed for high-capacity lift trucks, like those used in ports and rigging.
They use a roller-guided mounting arrangement, which enables heavy forks to be easily moved side-to-side on the carriage.
Boat Forks
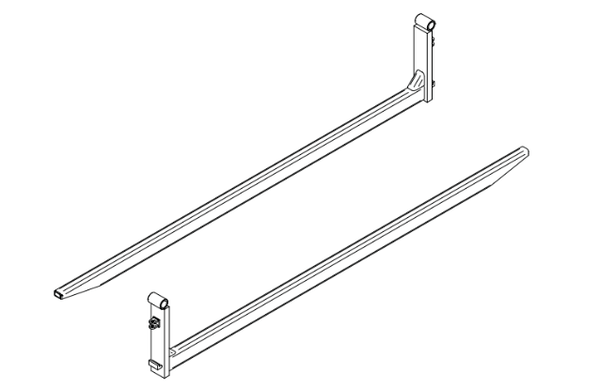
Boat forks are used in marine applications to transfer boats between the water and storage.
They have a rubber coating on the blade to protect the delicate hull of boats.
They’re also usually coated to prevent corrosion from exposure to seawater.
Tow Hitch Forks
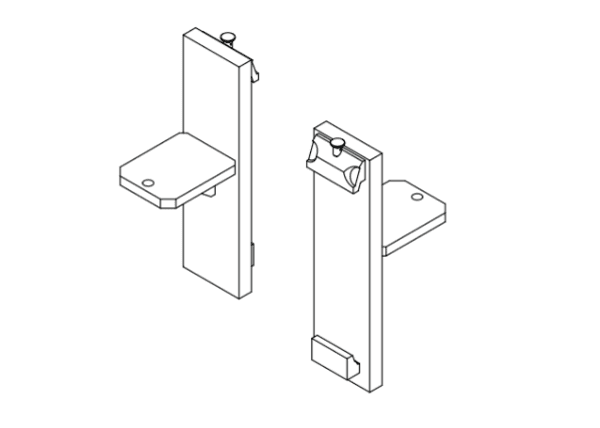
Tow hitch forks have load-bearing top and bottom mounting hooks which allow them to be used for pulling and pushing loads.
They mount to standard ITA carriages and can be installed alongside existing forks, eliminating hassle and downtime.
Inverted Forks
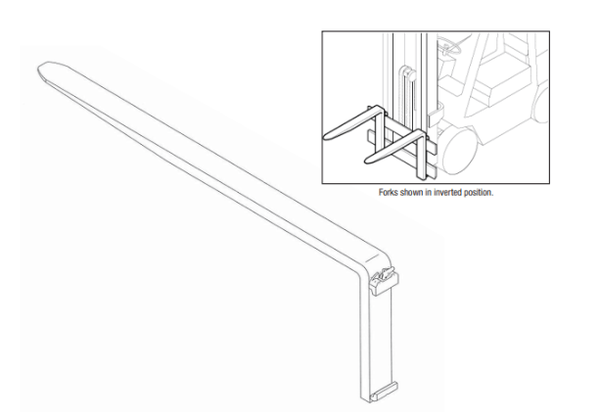
These forks are permanently mounted upside-down and designed to lift suspended loads, like bags and sacks.
The main disadvantage of inverted forks is that they lose 15% lifting capacity compared to regularly-hung forks.
Fork Extensions
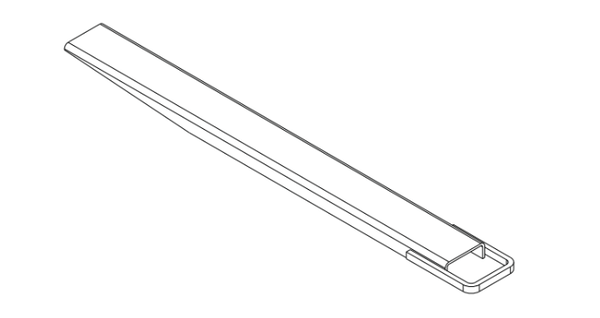
If you only occasionally need long forks for a forklift, fork extensions are a cost-effective option.
For example, many companies like to keep a pair of 60- or 72-inch fork extensions around to handle the one-off long load.
We cover fork extensions in more detail in a later section.
How to Choose Forklift Forks
Selecting the right forklift forks helps prevent injury to your employees along with damage to goods, equipment, and infrastructure.
But how do you choose the right fork for both your forklift and operations?
Let’s go through the key considerations.
The guidelines below are general considerations. It’s always best to have a qualified forklift professional help you choose the right forklift forks.
Identify the Carriage and Fork Class
Recall that the most basic way to categorize forklift forks is by their carriage size.
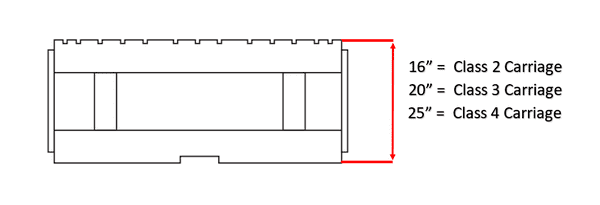
This is by design, to allow forks to be used across multiple manufacturers and forklift models – so long as the carriage sizes are the same.
Also, remember that the carriage size corresponds to the ITA fork class.
So, you’ll need to find out what your forklift’s carriage size is to get the right fork class.
If you don’t know your forklift’s carriage class, measure the carriage from the top bar to the bottom bar.
Then, compare it to the ITA specifications listed at the beginning of this article.
For instance, a Class 2 forklift carriage height is 16 inches.
So if your carriage is 16 inches as well, you know you’ll need Class 2 forks.
Determine Your Forklift’s Weight Lifting Capacity
Every forklift is rated to handle a particular weight capacity.
And it’s important to ensure your forks are rated for at least what your lift truck can handle.
For example, if your forklift is rated to lift 5,000 lbs., your forks must be rated to handle at least 5,000 lbs.
You can find your fork truck’s weight capacity rating on the data plate.
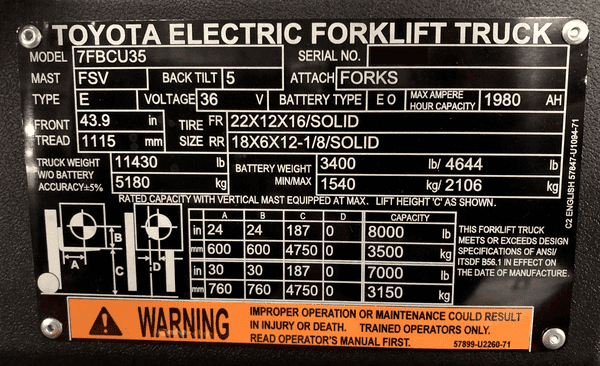
Then, use a forklift fork size chart to compare the weight capacity to the required fork dimensions (thickness and width).
You can reference Cascade’s fork capacity chart on page 2 of this PDF.
Will You Use a Forklift Attachment?
Attachments like rotators have specific fork requirements you must abide by.
Check the attachment’s operator manual for specifics.
What Types of Loads Will You Be Working With?
The type of loads your forklift will be carrying dictates the type of forks you should mount.
Are the loads palletized?
Or are they non-palletized and stacked, like cardboard or steel sheets?
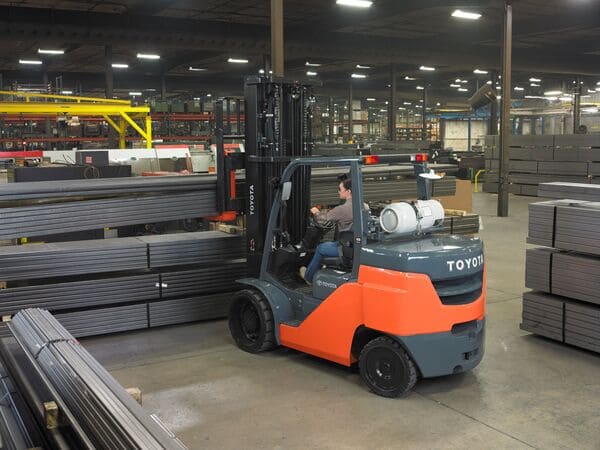
This helps you determine the fork style, such as the taper and tip types.
For example, picking up non-palletized loads where you have to slip in between layers of material may work best with fully-tapered and polished forks.
Forklift Fork Taper Styles
Forklift forks can have several different taper styles:
Taper refers to the degree of slant between the shank and the blade tip.
Most forks are tapered along the bottom of the blade, with a flat space left near the tip.
Fully-tapered and polished forks, on the other hand, have a full taper from the heel to the tip.
For a more detailed breakdown of fork tapers and tip styles, reference page 19 of Cascade’s Fork Facts document.
How Long Are Your Loads?
What length pallet forks do I need?
The first step in answering this question is to determine how long your loads are.
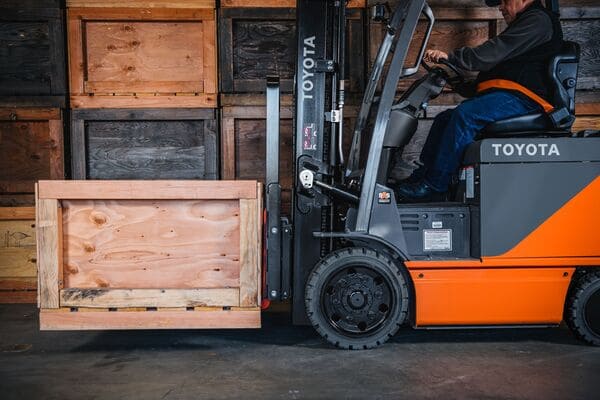
Why?
Because you don’t want to have your forks too long.
Using forks that are too long can cause problems like:
-
Striking pedestrians
-
Hitting racking
-
Damaging products
But you also don’t want your forks to be too short.
Otherwise, the load could become unstable and unsafe.
So, how far should the forks extend into the load?
Forks should reach at least 2/3 of the way into the load.
Using Forklift Fork Extensions
If you only occasionally handle long loads, you probably don’t want to have long forks on all the time.
What’s the solution?
Fork extensions.
4 Quick Facts on Fork Extensions
-
They come in thicknesses of up to 7-inches and lengths up to 96-inches
-
They’re prone to wearing out quickly, so they should only be used occasionally
-
They increase the load center, which reduces the forklift’s lifting capacity
-
It’s important to use the manufacturer’s guidelines for calculating the new lifting capacity to avoid lift truck instability
What Size Fork Extensions Do I Need?
If you’re wondering “How long can my fork extensions be?” the answer is that they can’t be more than 150% of the length of your installed forks.
For example, if you’re using 48-inch forks, fork extensions should be a maximum of 72 inches.
And just as with regular forks, fork extensions should reach at least 2/3 the length of the load but not all the way through it.
How Much Weight Can Fork Extensions Handle?
You’ll want to reference the manufacturer’s guidelines for how much weight their fork extensions can handle.
For an example of what their fork extension capacity chart may look like, you can review the one provided by Horizon Attachments:
Forklift Fork Inspections: What You Need to Know
During forklift maintenance and inspection, don’t forget about the forks.
You should always ensure that your forks are well-maintained and in compliance with OSHA, ANSI’s guidelines, and any other relevant safety standards.
Here are the basics of forklift fork inspections.
Why Do You Need to Inspect Forklift Forks?
For one, worn, cracked, and damaged forks can fail, causing injuries or fatalities to workers and causing damage to infrastructure, equipment, and product.
For another, forklift fork inspections are required by OSHA as part of the pre-trip forklift inspection.
What Rules Govern Forklift Forks?
OSHA, ANSI, and ISO provide the industry standards for forklift forks.
OSHA’s key forklift guidance and requirements include:
- Employers are responsible for ensuring forks are in good order before use – failure to do so may be a violation of the general duty clause
- Inspect forks during the pre-operation forklift inspection and remove forks that are not in good working order from service
- Don’t use forks that show any defects such as surface cracks, bent shanks or blades, uneven tips, or excessive wear
- Never operate a forklift that has a missing, inoperable, or removed positioning lock. These help prevent the forks from sliding during travel and the possible loss of the load
ANSI’s forklift fork standards and requirements include:
- B56.1-2012 – Safety Standard for Low Lift and High Lift Trucks. Sets general rules for both users and manufacturers of lift trucks, along with specifics on forklift forks
- B56.11.4 – Hook-Type Forks And Fork Carriers For Powered Industrial Forklift Trucks. Sets design, dimensions, operation, testing, and maintenance requirements for forklift forks
The ISO’s forklift standards and requirements include:
- ISO 2328 – Industrial trucks – Hook-on type fork arms and fork arm carriages – Mounting dimensions. Standardizes the mounting dimensions between the fork hooks and carriages to make it easier to switch different forks
- ISO 2330:2002 – Fork-lift trucks – Fork arms – Technical characteristics and testing. Defines manufacturing, testing, and marking requirements of forklift forks
- ISO 5057:1993 – Industrial trucks – Inspection and repair of fork arms in service on fork-lift trucks. Defines how to perform fork inspections along with repair and testing requirements
Forklift Fork Wear: Limits, Causes, and Prevention
Forklift forks should be replaced once they’re 10% worn.
A fork that’s 10% worn out experiences a 20% reduction in lifting capacity.
And this can make using the forks dangerous.
How Often Should You Check Your Forks for Wear?
Before every use.
As mentioned, this is part of the pre-trip inspection required before operating a forklift.
What Causes Forklift Forks to Wear?
Several factors often act in combination to wear forks out:
Dragging the Forks on the Ground
This is one of the biggest factors and also one of the reasons why you should drive with the forks 4 to 6 inches off the ground (the other being to increase stability).
Alternatively, you can use fork heel protectors to guard against wear and extend the life of the forks.
Frequently Sliding the Forks Back and Forth on the Carriage
In particular, this causes the fork hooks to erode.
And it’s amplified when using a fork positioner since these forks are often constantly moving back and forth throughout the entire shift.
That’s why it’s important to keep both the upper and lower carriage bars regularly greased to reduce friction and wear.
Moreover, sliding can increase locking pin wear, requiring them to be replaced more frequently.
Other Fork Wear Causes
-
Everyday wear and tear
-
Collisions with walls and columns
-
Improper forklift chain tension
-
Overloading
-
Improper forklift attachments
How Do You Inspect Forks?
Some of the fork inspection items can be done visually.
Others will require a fork caliper:
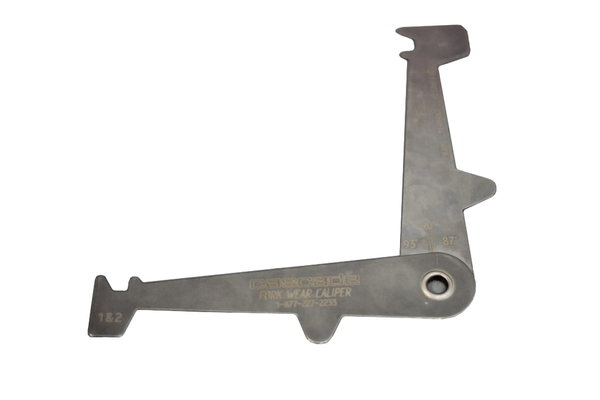
Don’t have one?
Check with your local material handling dealer – they’ll be able to get you one.
Now, let’s go through how to perform each forklift fork inspection action.
Measure the Blade Wear
- With a fork caliper, close the caliper so the outer teeth are as thick as the shank (The shank typically experiences little wear, so it should be the initially manufactured thickness. You’ll use this to compare to the heel, which experiences the most wear)
- Move the caliper to the blade, between 1 ½ and 3 ½ inches away from the shank
If the heel passes over the inner teeth, the fork is worn 10% or more and must be removed from service.
Note: This procedure does not apply to tapered forks. You’ll need to know the factory thickness of the fork, then consult the manufacturer for allowable wear.
Measure the Hook Wear
- Use the class markings on the caliper knobs to match your fork class:
2. Insert the knob into the fork hook:
If the caliper arm makes contact with the hook lip, remove the forks from service.
Check for Cracks
When checking for fork cracks, pay particular attention to the following areas:
- The heels
- Any welds (such as those attaching the hooks to the back of the shank)
Remove forks with cracks from service.
Check the Straightness
This is required for both the blade and the shank.
- Use a straightedge and measuring tape to measure any height difference between the blade-and-tip and shank-and-top
- Measure the shank height
- Measure the blade length
- Multiply the shank length by 0.005
- Multiply the blade length by 0.005
- Compare any height differences to your shank length and blade length calculations
If either is more than 0.5% off, remove the forks from service.
Measure the Angle
Check the angle between the blade and the shank:
- Open your forklift fork caliper so the knobs are pointed outward
- Place the caliper in the fork heel so that all the knobs touch both the shank and the blade
- Use the markings on the caliper to measure the angle
The angle must be within +/- 3 degrees of 90 degrees.
That means if the angle isn’t between 87 and 93 degrees, you’ll need to remove the forks from service.
Check the Tip Level
Check the alignment between both tips of the forks:
- Measure any difference in the tip height between each fork
- Measure the blade length
- Multiply the blade length by 0.03
If one tip is higher than the other by more than 3% of the blade length, remove the forks from service.
Check the Locking Hardware
Checking the locking hardware is simple.
Make sure the pins or latches are in place, working as they should, and free from damage and wear.
If any deficiencies are found, remove the forks from service.
Check the Fork Markings
Fork markings are usually stamped on the side of the shank.
All markings must be present and legible.
If neither is the case, remove the forks from service.
Forklift Fork Dos and Don’ts
Here’s a quick summary of the dos and don’ts of forklift forks:
Do…
- DO inspect forks at least daily and before each shift for wear and damage
- DO replace forks in pairs
- DO use the locking pins to secure the forks before using
- DO ensure the load is within the safe lifting capacity of the lift truck and the forks
- DO use both forks for lifting – never lift with a single fork
- DO keep the load as close to the shank face and load backrest as possible. This helps reduce the risks of tip-overs and falling loads
- DO monitor how quickly your forks wear and devise a replacement schedule
- DO inspect the forks for bends and damage if they strike something
- DO destroy worn forks so they aren’t used again by mistake
Don’t…
- DON’T use forks for pushing – they’re designed for lifting only
- DON’T use forks to open doors or break loads apart
- DON’T lift a load very far out on the forks
- DON’T lift a load that’s heavier than the fork truck and fork load ratings
- DON’T switch forks between trucks without verifying the rated capacity
- DON’T let passengers ride on the forks
- DON’T attempt to repair forklift forks
- DON’T attempt to straighten forklift forks
- DON’T weld forks – applying heat to the forks diminishes their strength
- DON’T cut forklift forks
- DON’T drill holes in a fork
On Modifying Forks
Many people ask the following questions:
- Can you repair forklift forks?
- Can pallet forks be straightened?
- Can forklift forks be drilled?
- Can you cut forklift forks?
And the answer is that it’s prohibited to do any of the above without approval from the manufacturer.
So, if you want to make modifications to your forklift forks, consult the manufacturer or your local authorized material handling dealership first.
Conclusion
There you have it: Everything you need to know about forklift forks.