Want to learn about automatic replenishment?
Then you’re in the right place.
Because this article has everything you need to know!
Keep reading to find out:
- What automatic replenishment is
- How it works
- Who can benefit from it
- Its advantages and disadvantages
- The different types
- Best practices for choosing a system and vendor
- And lots more!
Let’s dive in!
What Is Automatic Replenishment?
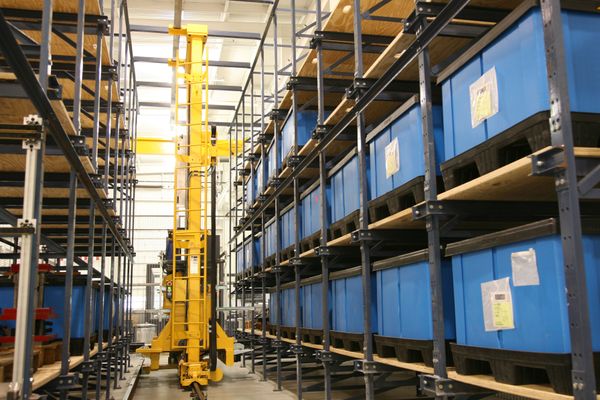
Let’s begin with the meaning of auto-replenishment.
Automatic replenishment is a computerized method of analyzing inventory levels, lead times, and sales requirements to create replenishment plans and automatically reorder stock as needed. It can consist of automated transportation, storage, and/or management systems that supply materials to warehouse locations or production lines.
By implementing automated replenishment systems, businesses can ensure they maintain an adequate level of inventory. This helps them serve customers without interruptions or delays and without the need for constant manual oversight and intervention.
Who Needs Automatic Replenishment?
Automatic replenishment systems automate the process of reordering items, supplies, or materials. This can benefit various types of industries/companies, most of which use warehousing solutions, including:
Manufacturing
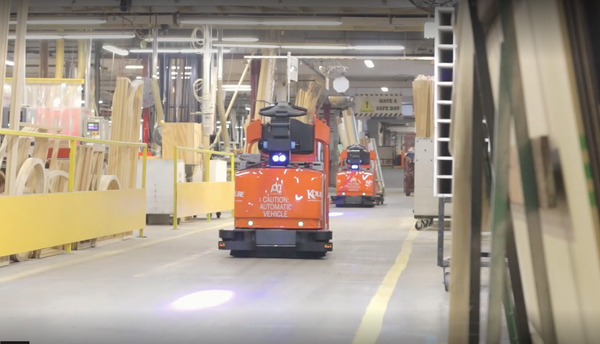
Manufacturers can use automatic replenishment by automating their raw materials or components reordering process.
This way, they’ll ensure to always have the necessary resources to keep production running smoothly.
Examples of manufacturers that can use automatic replenishment are electronic manufacturers, automotive, pharmaceuticals, textiles, and more.
Retail
Retailers – large and small – can benefit from automatic replenishment to ensure their warehouses and shelves are always stocked with popular products.
This can help avoid lost sales due to out-of-stock items. It can also improve their customer’s satisfaction by ensuring that the products they need are always available.
Examples of retailers that use automatic replenishment are Walmart, Dollar Tree, Target, Costco, and Tesco.
Food and Beverage
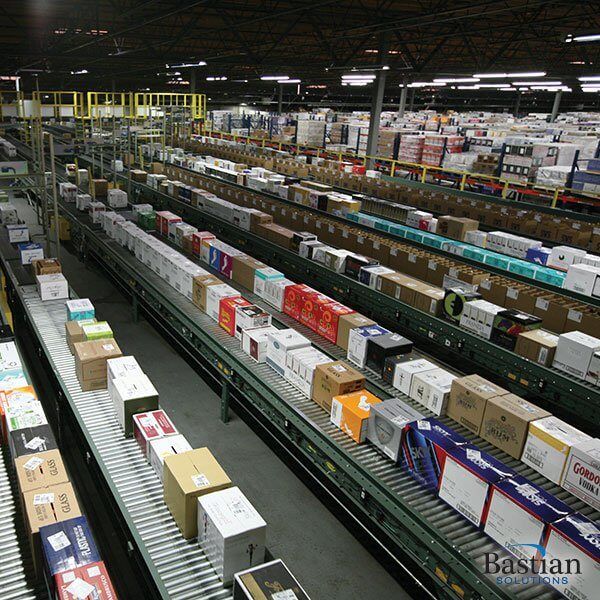
Restaurants and other food and beverage enterprises can use automated goods replenishment to automate their ingredient and supplies reordering process.
This can ensure they always have the necessary resources to prepare and serve their menu items or manufacture food products.
Examples of food and beverage companies that can use automatic replenishment are:
- Soft drink manufacturers
- Snack food manufacturers
- Dairy product manufacturers
- Meat packers
- Baked goods manufacturers
E-Commerce
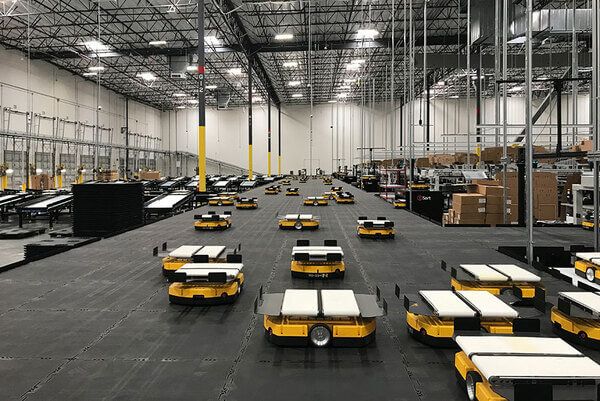
E-commerce businesses and warehouses commonly use automatic replenishment.
They use the solutions to automate the process of reordering products when inventory levels reach a certain threshold to avoid lost sales due to out-of-stock items
This also ensures that they can fulfill their orders quickly. For example, by using autonomous mobile robots (AMRs) or automated guided vehicles (AGVs).
Examples of e-commerce companies that use automatic replenishment are Amazon, Target, Walmart, Best Buy, and Costco.
Service Businesses
Service-based businesses that rely on consumable supplies, such as cleaning services or printer repair, can benefit from automatic replenishment.
By automating their supplies reordering process, they can always have what they need to provide quality service to their customers.
Healthcare
Hospitals, pharmaceutical companies, and healthcare providers are key users of automatic replenishment.
It helps them ensure that they always have the necessary medical supplies on hand or raw materials to produce the supplies.
Automatic replenishment helps them avoid stock shortages or supply delays.
How Does Auto Replenishment Work?
Automated inventory replenishment uses technology and real-world data to automatically manage reorder levels.
Here’s how it works:
1. Set Reorder Thresholds
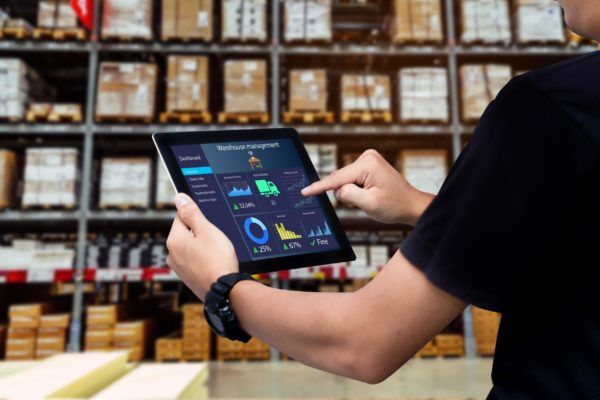
The operation first determines its reorder threshold. This is the minimum inventory level they need to maintain for each product or material in their inventory.
Planners can edit each item/material individually, or upload them into the system in bulk via CSV file.
When inventory levels fall below this threshold, it triggers an automatic replenishment order.
2. Roles and Permissions
Depending on your auto-replenishment system, you may need to set roles and permissions for roles to limit access to the replenishment system. For example, reordering may require permission to be activated. That way, you can limit who can change what within the system.
3. Inventory Monitoring
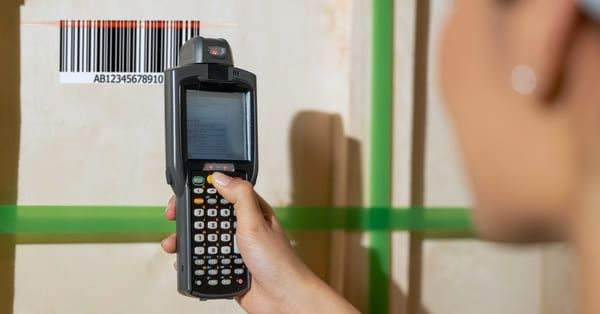
Businesses can use various methods to monitor inventory levels, such as barcode and RF scanners, RFID tags, or inventory management software. This tracks each product or material’s level and gives the auto-replenishment solution real-time data on inventory levels.
4. Reorder Triggers
When inventory levels fall below the reorder threshold, the auto-replenishment system automatically generates a reorder trigger.
5. Order Placement
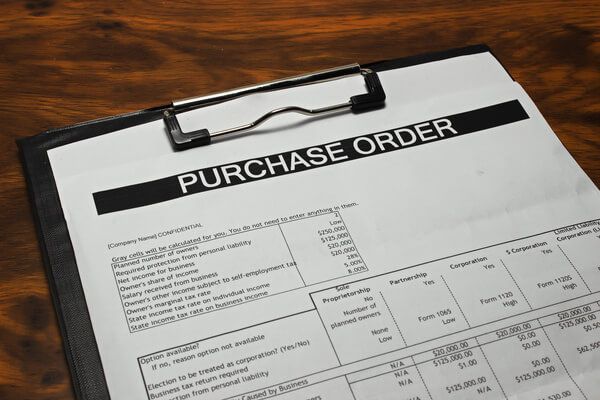
In addition to calculating quantities, the system can automate physical tasks such as stock transfers and the generation of purchase orders for efficient order placement. After generating the reorder trigger, it can be sent to the business’s purchasing department. The auto-replenishment system can also place an order if configured to do so.
6. Delivery and Receiving
After receiving the order placement, the supplier arranges to fulfill it and deliver the products or materials to the business. The business then receives the shipment, updates its inventory levels, and the automatic replenishment system is reset until the next reorder threshold is reached.
Advantages of Automated Replenishment
Automatic replenishment ensures the uninterrupted movement of goods to storage systems, production lines, and/or pick stations, enabling a seamless flow of inventory.
Let’s take a look at some of the main benefits of implementing an automated replenishment solution:
Operational Efficiency and Accuracy
- Complete, Real-Time Inventory Control: Automating replenishment with warehouse management software leads to more accuracy in goods handling, especially in the areas of stock turnover and product traceability.
- Higher Stock Availability or Reduced Stockouts: Automated replenishment helps businesses maintain optimal inventory levels, ensuring that they don’t run out of stock. This means that they can meet customer demand without delays or backorders. And fewer delays mean happier customers, which means more sales.
- Improved Accurate Recording and Fewer Inventory Errors: Automated replenishment is less prone to human error than manual methods. This allows businesses to reduce errors and risks, such as over-ordering or under-ordering, ensuring that they have the right amount of inventory at all times.
- Increased Efficiency: Automated replenishment streamlines the supply chain process, reducing the need for manual labor, paper-based tracking, and other time-consuming activities. This can increase efficiency, lower costs, and boost productivity.
- More Time for Value-Added Work: Automated replenishment processes use advanced algorithms to minimize the time spent on manual purchasing and administration significantly – perhaps by up to 50%. This frees up manpower to zero in on more value-adding activities in the warehouse.
- Less Waste: Overstocking of goods is as problematic as running out of stock. It creates a risk of loss and waste as goods may not be sold before their expected period. Overstocked goods also risk damage or expiry. Using auto-replenishment software eliminates these risks.
Cost Savings and Financial Optimization
- Better Forecasting and Resistance to Seasonality: Automated replenishment technology provides real-time data on inventory levels, which can help businesses forecast demand more accurately. This means that they can plan for seasonal trends, promotions, and other factors that affect inventory levels. Also, having an automatic stock replenishment system software ensures the availability of safety stock to cope with changing demand for goods.
- Lower Labor Costs: Auto replenishment solutions help businesses to reduce costs associated with inventory management, such as excess inventory, stockouts, labor costs, and emergency orders. Also, by maintaining optimal inventory levels, businesses can reduce waste, improve cash flow and minimize the need for emergency orders.
Customer Satisfaction and Sales Growth
- Higher Customer Satisfaction and Experience: Auto replenishment can help businesses improve customer satisfaction by ensuring that they have the products that customers want when they want them. This means that businesses can fulfill orders faster, reduce lead times, and increase customer loyalty.
- Higher Sales: Installing an automated replenishment solution can maintain a healthy inventory. You’ll reduce the risk of overstocking or understocking and service your customers right. By ensuring effective order fill rates there is a higher chance of increasing than losing sales.
Drawbacks of Automated Replenishment
While automated replenishment solutions may have many advantages, they also have some drawbacks that businesses should be aware of:
- Higher Capital Cost: Implementing auto-replenishment is expensive and potentially disruptive to operations. It can require a significant upfront investment in hardware, software, and training staff. This can be a barrier for small businesses or those with limited budgets.
- Ongoing Costs: Automated replenishment systems require regular maintenance and upgrades. The required costs may include equipment maintenance and staff re-training for updated systems. Businesses may need to hire additional staff or purchase additional software or hardware to keep the system running smoothly.
- Glitches Can Cause Downtime: Automated replenishment systems rely on technology and data, which can be prone to glitches, system failure, and overall downtime or delays. This can result in incorrect inventory levels, missed reorder triggers or poor customer experience.
- May Not Be Quickly Adaptable: Adapting to automated replenishment solutions may require a lot of work, including efforts to accommodate new products or retire old products to fit the reorder thresholds. If the reorder thresholds are inflexible and demand suddenly spikes or falls, the system may not adjust quickly enough, resulting in over- or under-ordering.
- Not Universally Applicable: Auto replenishment systems may not work in all industries and with certain product types. For example, products with short shelf lives or products that are highly customized may require manual inventory management in the warehouse.
Types of Automatic Replenishment
There are many types of automatic replenishment systems. Let’s take a look at the most common ones:
Minimum/Maximum Replenishment
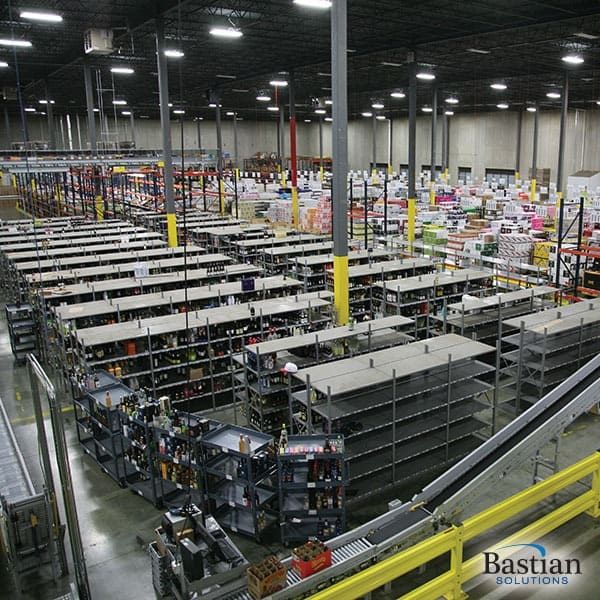
As the name suggests, this type of inventory replenishment system sets the minimum and maximum inventory levels for each product.
When the minimum level is reached, the auto-replenishment system generates a purchase order to replenish inventory up to the maximum level.
It’s a simplistic auto-replenishment model with relatively easy implementation. The model is best used for SKUs with predictable throughput and seasonal demand whose prediction can be based on historical data. But it can result in excess inventory if demand is lower than anticipated.
Forecast-Based Replenishment
Also called demand replenishment, this automatic replenishment type uses historical sales data to forecast future demand and generate purchase orders.
Automatic reordering limits should be set just high enough to fulfill a pending order or group of orders without leaving behind extra stock.
It provides better accuracy in ordering and the ability to quickly adapt to changes in demand. But it requires accurate data and can be more complex to implement.
Vendor-Managed Automatic Replenishment
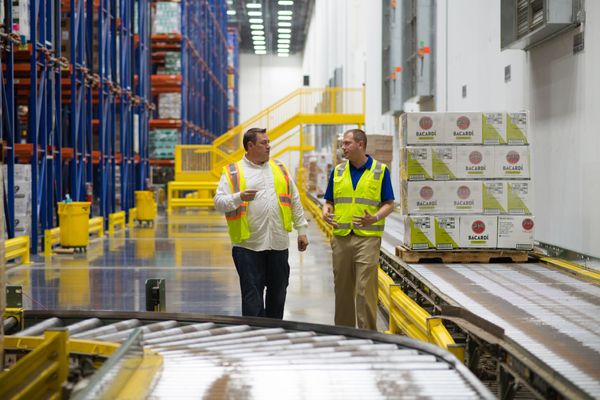
Also called vendor-managed inventory replenishment (VMI), in this arrangement, the supplier is responsible for managing inventory levels at the customer’s location.
The supplier uses the customer’s data to determine when to restock inventory, and the customer is billed only for the inventory used.
The model has reduced inventory holding costs and improved supply chain visibility. But it requires close collaboration and trust between the customer and supplier.
Continuous Replenishment
Continuous replenishment works like vendor-managed replenishment.
The supplier continuously monitors inventory levels and automatically replenishes them as needed (when they fall below the threshold).
The replenishment type provides the advantage of reduced stockouts and improved supply chain visibility. But the warehouse must form a close collaboration and integration with the customer and the supplier.
Just-in-Time (JIT) Replenishment
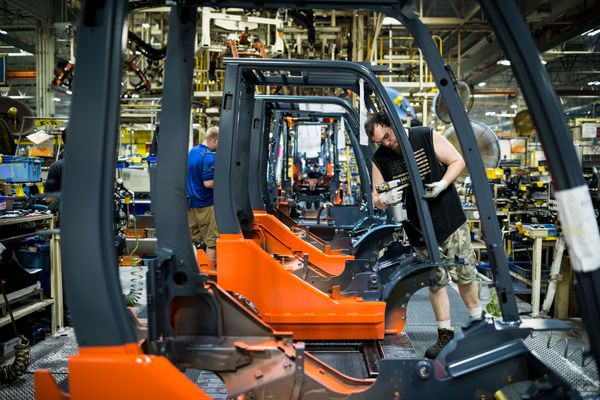
A Just-in-Time auto-replenishment system aims to minimize inventory levels by triggering the ordering of products only when they are needed.
It’s ideal for specialty products that can go bad or risk damage. It results in lower inventory holding costs and reduced waste. But JIT requires a high degree of coordination and reliability in the supply chain.
Automatic Top-Off Replenishment
The automatic top-off replenishment model is similar to min/max replenishment thresholds.
It runs on a set schedule or batch released (by area, line, or product). The auto-replenishment system automatically triggers products to “top-off” inventory for a specific product to acceptable levels in picking areas. The data used to reorder is based on projected demand or a shift in the number of available staff.
This type of replenishment works well when the warehouse expects large waves of picking work or picking volume. It’s ideal in less active picking operations or when there are work shortages.
Periodic Inventory Replenishment
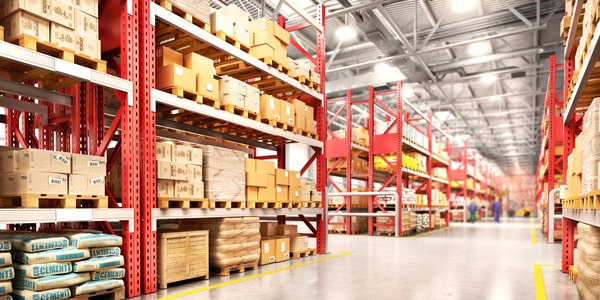
Periodic replenishment is similar to forecast-based replenishment.
In warehouses that use periodic replenishment type, the inventory quantities needed for the intervals (based on demand forecast) are moved to picking locations.
The end of these intervals provides review points and a time to check the amount of inventory in stock. If stock levels fall below the warehouse’s minimum threshold, the auto-replenishment system triggers reorders.
Otherwise, any reorder is skipped until the next review point.
This model is ideal for longer lead times and warehouses with large storage areas. It also incurs negligible carrying costs compared to ordering costs and the ordering costs are independent of order volume.
8 Best Practices for Choosing and Implementing an Automatic Replenishment System
Ensuring a seamless supply chain requires warehouses to adhere to the following best practices when choosing and implementing automatic replenishment systems:
Pre-Implementation Planning
- Assess Your Current Inventory Management Situation: The first thing to do before settling on an automatic replenishment system is to assess your current inventory management situation. The assessment should help you know what you’re currently doing efficiently, as well as find gaps, and problem areas in your current system, and how the new system should solve the problems.
- Set Your Goals: Clarify what you want out of your automatic replenishment system. These should be the solutions to your current inventory management situation, considering your business’s unique needs. So, once you’ve assessed and clarified your issues, your goals will simply be the solution to your pain points.
- Choose a Reputable Partner: Implementing an automatic replenishment system is a complicated undertaking. Realistically, you’ll need an experienced partner to help you. That’s why it’s critical to assess who you want to work with when implementing the system. Your partner will also likely be your partner throughout the life of the auto-replenishment system and perhaps beyond. That’s why it’s important to assess their history, experience, and reviews. Tip: to gauge their level of service beforehand, all their customer service and talk to a representative.
- Settle on an Auto Replenishment Solution: Collaboratively, you and your automation partner will consider your operation, budget, needs, and range of systems available to settle on the optimal solution. Consider the specific needs of your business, such as industry, product type, and supply chain structure, when choosing an automatic replenishment system. Make sure you’re comfortable with the cost, training requirements, resources required, and performance.
Implementation and Post-Implementation
- Implement the Solution: Your automation partner should handle most of the implementation process for you. After all, their job is to ensure the overall implementation process goes smoothly. That may include drawing up plans, contracting with designers and engineers, pulling permits, coordinating logistics, training staff, and supporting ongoing maintenance.
- Train Employees: During implementation, insist on staff training on how to use the automatic replenishment system effectively. Also, provide training on key activities, such as how to monitor and adjust inventory levels, how to interpret performance metrics, and how to troubleshoot issues. This will help ensure that your operations run smoothly and prevent downtimes.
- Start Small and Test: Start with a small subset of products and test the automatic replenishment system before full-scale implementation in your operation. This can help identify any issues and fine-tune the system for maximum effectiveness.
- Refine, Monitor, and Maintain: Once the system has been implemented, you and your partner will need to monitor it to make adjustments as necessary. Monitor the system for accuracy and any problems. Review key metrics such as inventory turnover, stockout rates, and order lead times to assess its effectiveness. Also, keep up on regular maintenance (software and hardware) to ensure everything runs as smoothly as possible. This is also where your partner comes in to help maintain the system and troubleshoot any issues that may come up.
Top 13 Automatic Replenishment Vendors
Automatic replenishment systems help companies manage inventory supply levels, helping ensure consistent and timely replenishment.
Below is a list of the top automatic replenishment vendors you can choose from (in no particular order):
PathGuide Technologies
PathGuide Technologies’ Latitude WMS software features real-time inventory control, RF and voice support, and integration with other warehouse equipment (including carousels, conveyor systems, and pick-to-light and put-to-light systems).
LEAFIO
The LEAFIO inventory optimization system is an inventory management solution for retail, with automatic replenishment and allocation solutions as a core feature. LEAFIO provides a complete ordering process at all levels of the supply chain without manual intervention.
With a forecasting module and consideration for atypical and seasonal demand fluctuations, LEAFIO can autonomously forecast, plan demand, automate replenishment and balance the supply chain for different warehouse types.
Blue Yonder
Founded in 1985, Blue Yonder is a leader in supply chain and omnichannel commerce fulfillment, which includes automatic replenishment. The platform provides auto-replenishment, manufacturing planning, retail planning, store operations, and category management automation.
TrueCommerce
TrueCommerce provides supply chain visibility and collaboration tools for supply chain operations. It does this “via business point-to-point (P2P) connectivity, order management, collaborative replenishment, and intelligent fulfillment.”
GMDH Streamline
Founded in 2008 and based in the US, GMDH Streamline offers advanced warehouse analytics and forecasting tools for businesses. The platform uses AI and machine learning algorithms to forecast demand and optimize inventory levels.
They offer a range of products, including demand planning software and inventory optimization tools, as well as automatic replenishment capabilities to ensure optimal stock levels.
Relex Solutions
Relex Solutions provides cloud-based supply chain management software from its headquarters in Finland. Their software includes demand forecasting, inventory management, and automatic replenishment capabilities for retail, wholesale, and manufacturing companies.
The platform uses AI and machine learning to optimize inventory levels, automate replenishment and distribution, and reduce waste. Relex Solutions caters to a variety of industries, including grocery retail, fashion, and fresh products.
Handifox
Founded in 2006 and based in the US, HandiFox offers inventory and sales management software for small and mid-sized businesses.
Their platform includes features such as barcode scanning, inventory control, tracking, management, automatic replenishment, warehouse, stock, and sales management, real-time monitoring, and more. HandiFox focuses on providing easy-to-use solutions for businesses in a variety of industries, from manufacturing to distribution.
eTurns
eTurns is an automatic replenishment vendor that provides inventory management software for enterprises. Their software includes features such as barcode scanning, automatic replenishment, and mobile inventory management.
It helps businesses reduce stockouts and improve their order fulfillment process. It supports anyone who wants to streamline and optimize the inventory replenishment process, including wholesale, distributors, manufacturers, service contractors, and healthcare.
MarginPoint
MarginPoint is a US company that offers inventory management software for service contractors, like plumbers, HVAC, electricians, and facility maintenance. Their platform includes features such as mobile inventory management and automatic replenishment, as well as integration with popular accounting software like QuickBooks.
AGR Dynamics
UK-based AGR Dynamics offers supply chain planning software for businesses. Their software includes features such as demand forecasting, inventory management, automatic replenishment, and advanced analytics. AGR Dynamics caters to a variety of industries, including food and beverage, pharmaceuticals, and retail.
IBM Sterling Supply Chain Suite
IBM Sterling Supply Chain Suite is a cloud-based platform that offers end-to-end supply chain management solutions for businesses of all sizes. It includes a range of tools for order management, inventory optimization, and supplier collaboration, as well as advanced analytics and AI capabilities.
It promises businesses real-time visibility into their supply chain operations, enabling them to make faster, data-driven decisions. The suite includes an automatic replenishment that uses predictive analytics and ML to optimize inventory levels.
Logility
Founded in 1996, Logility is a subsidiary of American Software. The Logility platform is a cloud-based system for multi-stage inventory optimization (MEIO). This includes a “dynamic allocation algorithm” that provides businesses with automated replenishment functionality.
Logility claims its system is powerful enough to allow retailers with several multi-distribution centers to automatically distribute and restock each store or channel from any combination of distribution centers.
iVend Retail
Founded in 2012 in India, iVend Retail provides omnichannel retail management software. Their software’s features include inventory management, order management, automatic replenishment, and integration with popular accounting and ERP systems.
iVend also provides a unified view of inventory and sales across all channels, helping businesses improve their customer experience and increase sales. The company serves businesses in various industries, from food and beverage, to fashion, and electronics.
Common Automatic Replenishment Questions
Who Is Automatic Replenishment For?
Automatic replenishment is for businesses that want to optimize their inventory management processes and reduce the costs associated with overstocking or stockouts.
It is particularly useful for companies with high inventory turnover, seasonal demand fluctuations, or complex supply chains. Different businesses can benefit from automatic replenishment such as retailers, manufacturers, suppliers, distributors, and ultimately their customers.
What Are the Benefits of Automatic Replenishment?
Automatic replenishment provides various benefits, including:
- Improved business efficiency
- Improved inventory accuracy
- Reduced inventory holding costs and warehouse operational costs
- Increased customer satisfaction
- More accurate data analysis
- Better supply chain visibility
- Streamlined purchasing processes
- Reduced risk of stockouts or overstocking
What Are the Risks of an Automated Inventory System?
The risks of an automated inventory system include:
- High capital costs and ongoing maintenance and upgrade costs can cause financial strain
- Training needs can drain already-low staffing levels
- System glitches may cause downtime
- Accommodating new products or retiring old products may require extensive modification
What Are the Types of Automatic Replenishment?
The types of automatic replenishment include the following:
- Minimum/maximum stock level.
- Order point replenishment.
- Forecast-based replenishment
- Vendor-managed replenishment
- Automatic top-off replenishment
- Just-in-time (JIT) replenishment
- Periodic replenishment
- Continuous replenishment
How Does Automatic Replenishment Integrate with Other Inventory Management Systems?
Automatic replenishment can integrate with other systems, such as warehouse management systems (WMS), inventory management systems (IMS), and demand forecasting tools, to improve supply chain visibility and optimize inventory levels. They can also integrate with procurement systems to automate purchasing processes and reduce manual data entry.
What Level of Customization Is Possible with an Automatic Replenishment System?
Some systems may offer extensive customization options, such as the ability to set unique stock level thresholds. Other systems may have limited customization options that only allow changing basic configuration settings.
The customization of an automatic replenishment system depends on the user, the vendor, and the specific features of the system.
How Does an Automatic Replenishment System Handle Sudden Spikes in Demand or Disruptions?
Automatic replenishment systems can handle sudden spikes or disruptions in demand by automatically adjusting stock level thresholds based on historical data or real-time demand signals.
Some systems may also have the ability to generate alerts or notifications when inventory falls below a threshold or when there are disruptions in the supply chain.
This can allow human intervention during critical times to handle situations that are beyond the capability of computerized systems.
How Can Businesses Measure the Success of Their Automatic Replenishment System?
To measure an automatic replenishment system’s success, businesses can track key metrics like inventory turnover, order lead time, stockout rates, and customer satisfaction levels.
Businesses can also compare these metrics to industry benchmarks or their own historical data to determine if the system is providing a positive return on investment (ROI).
What Factors Should Be Considered When Implementing an Automatic Replenishment System?
When implementing an automatic replenishment system, businesses should consider various factors, such as:
- Inventory turnover rate
- Supply chain complexity
- Their products’ historical demand patterns
- The level of customization required
- Vendor ability and reliability
- Need for Integration with existing inventory management and procurement systems
- Training needed
- Ongoing maintenance and future upgrades
Who Are Some Top Automatic Replenishment Vendors?
Some top automatic replenishment vendors include:
- Logility
- Latitude WMS
- LEAFIO AI
- Blue Yonder
- TrueCommerce
- GMDH Streamline
- Relex Solutions
- HandiFox
- eTurns
- MarginPoint
- AGR Dynamics
- IBM Sterling Supply Chain Suite
Conclusion
That’s it: Everything you need to know about automatic replenishment.