Automated material handling (AMH) is transforming logistics, warehousing, and manufacturing. Businesses are replacing manual processes with automated material handling systems to improve efficiency, reduce costs, and enhance accuracy.
From automated guided vehicles (AGVs) to robotic picking systems, these technologies streamline operations and minimize human intervention. As global supply chains grow more complex, automated material handling solutions are becoming essential for competitiveness.
This guide explores types of automated material handling systems, their benefits, industry applications, and key considerations for implementation.
What Is an Automated Material Handling System?
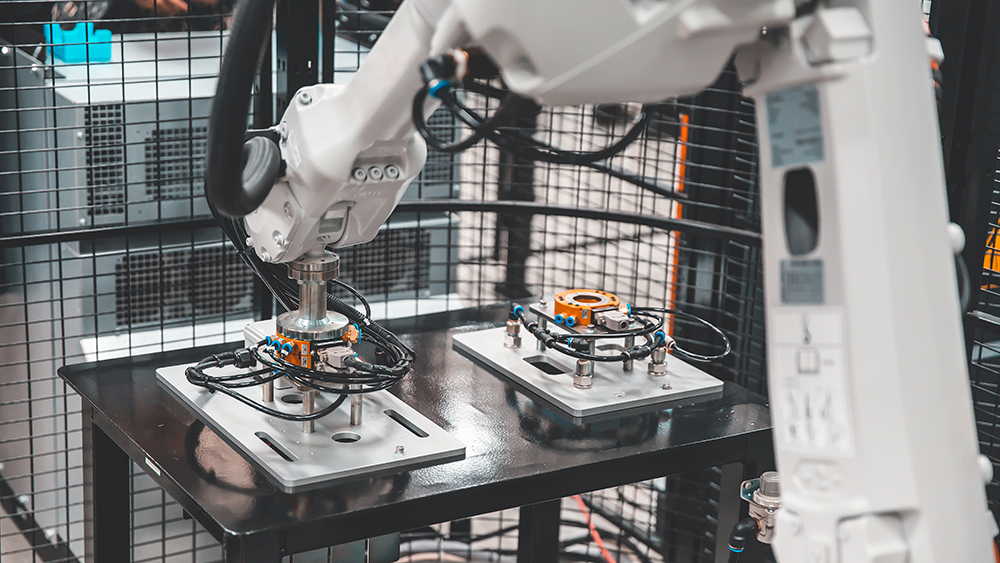
An automated material handling system (AMHS) uses machines, robotics, and AI-driven software to transport, store, and manage goods. These systems reduce labor-intensive tasks, enhance productivity, and optimize supply chain operations.
Key Components of Automated Material Handling Systems
- Automated Material Handling Equipment: Includes conveyor systems, storage units, and robotic solutions.
- Software & Control Systems: Warehouse Management Systems (WMS) and AI-powered analytics for tracking and efficiency.
- Material Transport Technologies: Automated guided vehicles (AGVs) and autonomous mobile robots (AMRs) for flexible movement.
AMHS can be fully automated or semi-automated, depending on business needs.
Types of Automated Material Handling Systems
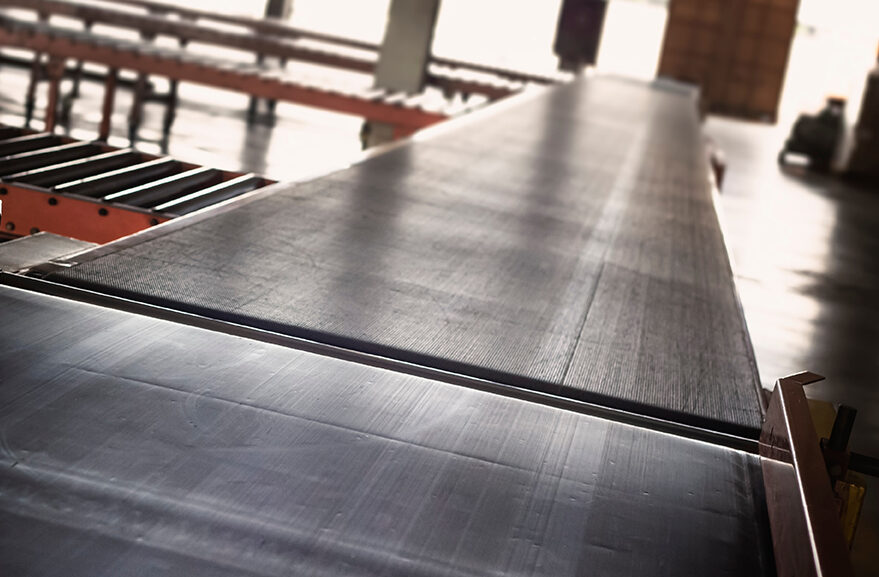
Businesses must choose the right types of automated material handling systems based on operational needs, product size, and warehouse layout.
Automated Material Handling Conveyors
Conveyors are one of the most common automated material handling products. They transport goods across facilities, minimizing manual lifting and improving efficiency.
- Belt Conveyors: Move products in a straight line for high-speed operations.
- Accumulation Conveyors: Allow controlled movement to prevent bottlenecks.
- Overhead Conveyors: Save floor space and move goods in complex paths.
Automated Storage and Retrieval Systems (AS/RS)
AS/RS uses robotics to retrieve and store items with precision. These automated material handling and storage systems reduce storage footprints and improve inventory accuracy.
- Unit Load AS/RS: Handles pallets or large loads.
- Mini-Load AS/RS: Ideal for small items like electronics or pharmaceuticals.
- Vertical Lift Modules (VLMs): Use stacked trays to maximize vertical storage.
Automated Guided Vehicles (AGVs) for Material Handling
AGVs in material handling transport goods within warehouses and manufacturing plants. They navigate using sensors, lasers, or magnetic strips, reducing reliance on forklifts.
- Pallet AGVs: Move heavy loads efficiently.
- Tugger AGVs: Pull multiple carts in warehouses.
- Unit Load AGVs: Transport individual totes or bins.
Autonomous Mobile Robots (AMRs) for Automated Material Handling
Unlike AGVs, AMRs in automated material handling use advanced AI for dynamic movement. They can reroute in real-time, avoiding obstacles and optimizing workflows.
- Goods-to-Person AMRs: Bring shelves or bins to workers for picking.
- Shuttle AMRs: Retrieve and transport cases or totes in high-density storage.
- Pick-Assist AMRs: Help human workers by carrying items during order fulfillment.
Robotic Picking and Palletizing Systems
Robotic arms improve speed and accuracy in warehouses. These systems include:
- Robotic Picking Systems: Use AI-powered vision to identify and grab items.
- Robotic Palletizers: Stack products onto pallets with precision.
- De-Palletizing Robots: Unload mixed pallets and sort items efficiently.
Sortation Systems in Automated Material Handling
Sortation systems classify and direct items to their correct destinations. These are critical in high-volume fulfillment centers.
- Tilt-Tray Sorters: Use tilting trays to sort items into chutes.
- Cross-Belt Sorters: Move items using small conveyor belts on a track.
- Bomb-Bay Sorters: Drop items into designated bins below.
Automated Material Handling for Different Industries
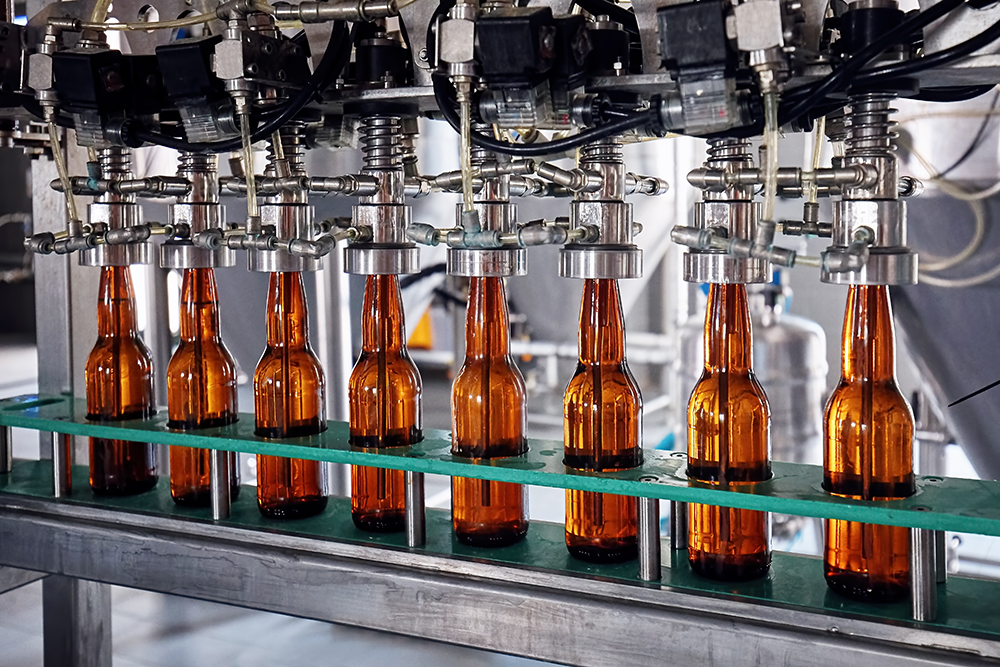
AMH is revolutionizing multiple industries. Each sector has unique needs for automated material handling integration.
E-Commerce & Retail
- Automated order fulfillment ensures rapid picking, packing, and shipping.
- Sortation systems speed up inventory movement in warehouses.
- AMRs and robotic picking increase efficiency in high-demand environments.
Manufacturing & Industrial Automation
- AGVs and conveyors move raw materials and finished products efficiently.
- AS/RS systems optimize warehouse space and reduce storage costs.
- AI-powered robotics improve precision in production lines.
Pharmaceutical & Healthcare
- Temperature-controlled AS/RS maintains the integrity of sensitive materials.
- Automated guided vehicles (AGVs) transport medical supplies with high accuracy.
- Robotic dispensers ensure precise medication packaging and handling.
Food & Beverage Industry
- Cold storage automation improves efficiency in frozen food distribution.
- Automated palletizing ensures secure stacking for fragile items.
- Sanitary robotics enhance food safety in handling and packaging.
Automotive & Heavy Industry
- Industrial AMRs transport heavy components on production floors.
- Automated material handling solutions improve just-in-time (JIT) manufacturing.
- Smart inventory tracking reduces waste and increases throughput.
Third-Party Logistics (3PL) & Warehousing
- Automated storage and retrieval systems (AS/RS) maximize warehouse space.
- Scalable AGV fleets improve adaptability for changing logistics demands.
- IoT-enabled automation enhances real-time tracking of goods.
Benefits of Automated Material Handling Systems
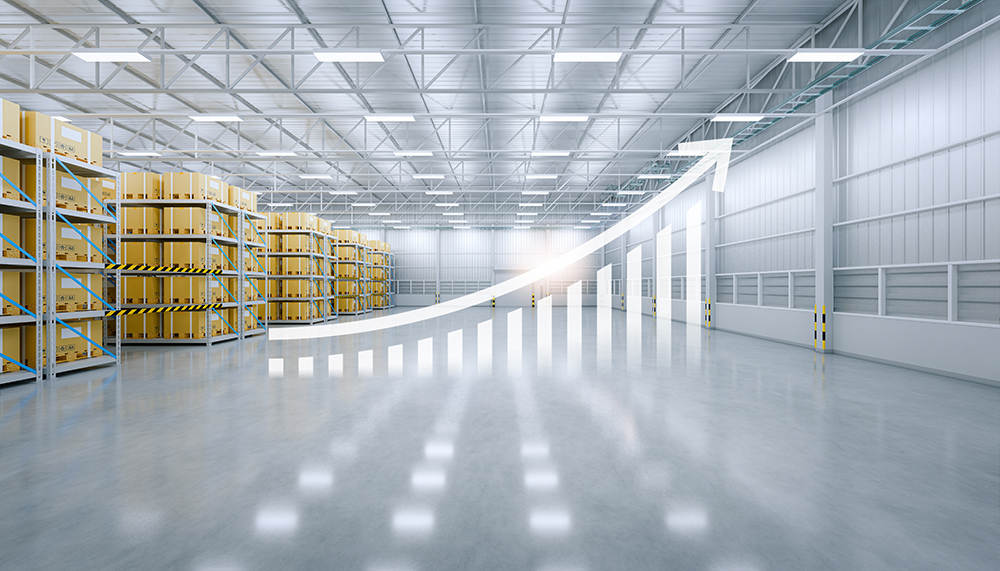
Businesses implementing high-end automated material handling gain several advantages.
- Efficiency Gains: Faster processing with reduced errors.
- Labor Savings: Reduces dependence on manual work.
- Accuracy & Inventory Control: AI-powered tracking minimizes mistakes.
- Safety Improvements: Robots handle hazardous materials, reducing workplace injuries.
- Scalability: Systems adjust to business growth and seasonal demand.
Challenges and Considerations in Automated Material Handling
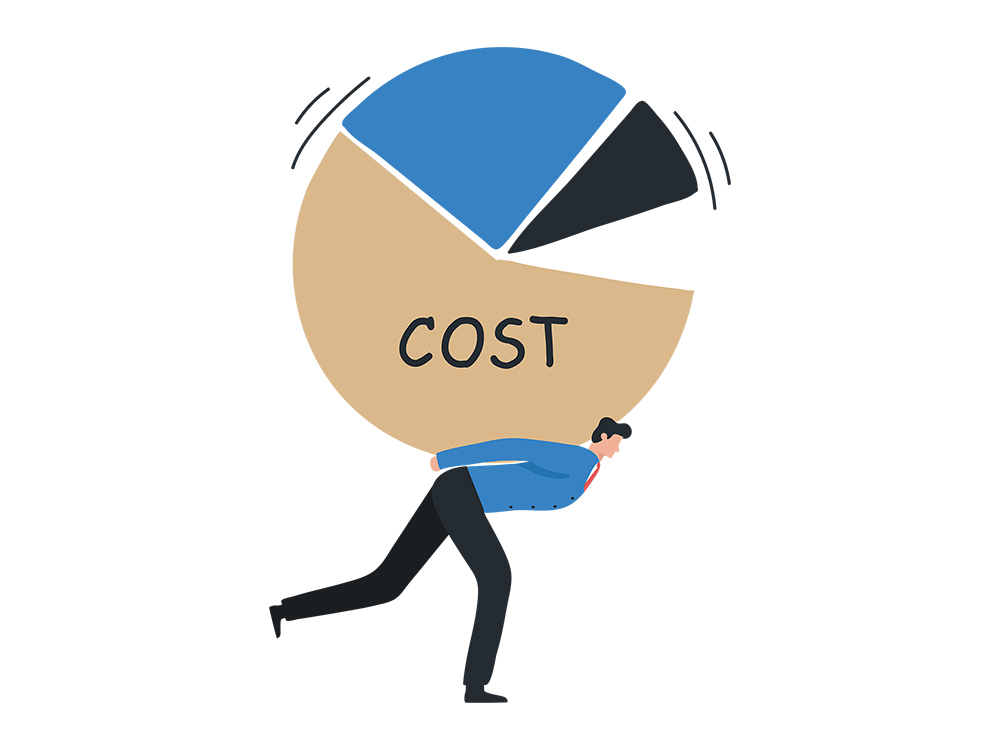
Despite the benefits, automated material handling integration comes with challenges.
- Initial Investment: High upfront costs, but long-term savings.
- System Compatibility: Requires seamless integration with WMS and ERP.
- Employee Training: Workers need new skills to operate automation technologies.
Future Trends in Automated Material Handling Technology
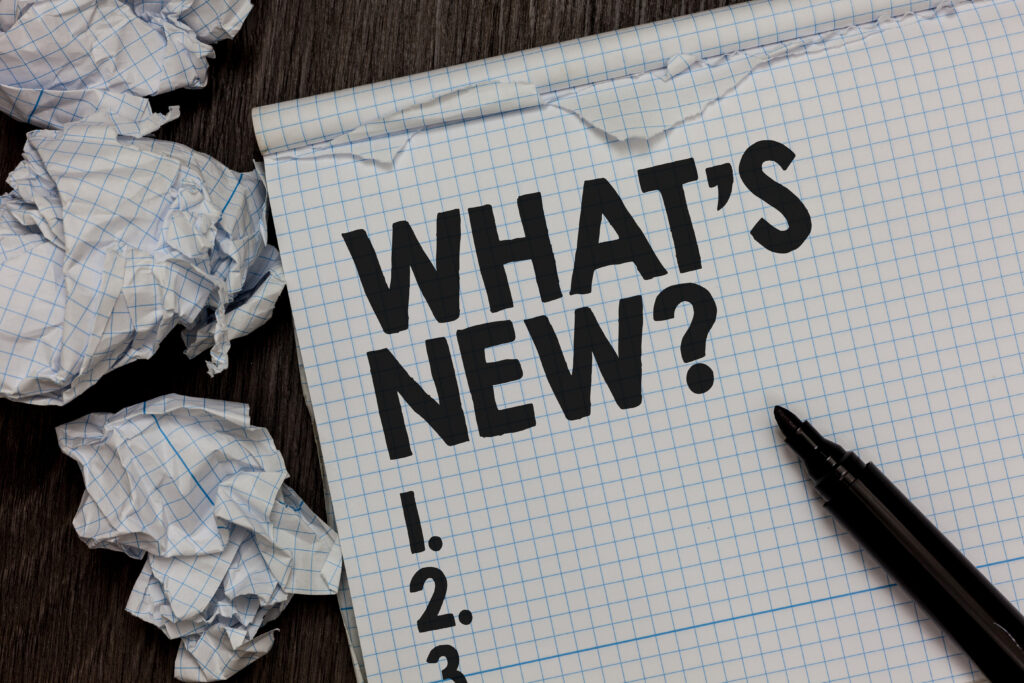
Innovation continues to push AMH forward. Future trends include:
- AI-Driven Optimization: Predictive analytics for smarter operations.
- 5G & IoT Connectivity: Faster data transmission for real-time decision-making.
- Robotics-as-a-Service (RaaS): Subscription-based automation models.
The Future of Automated Material Handling
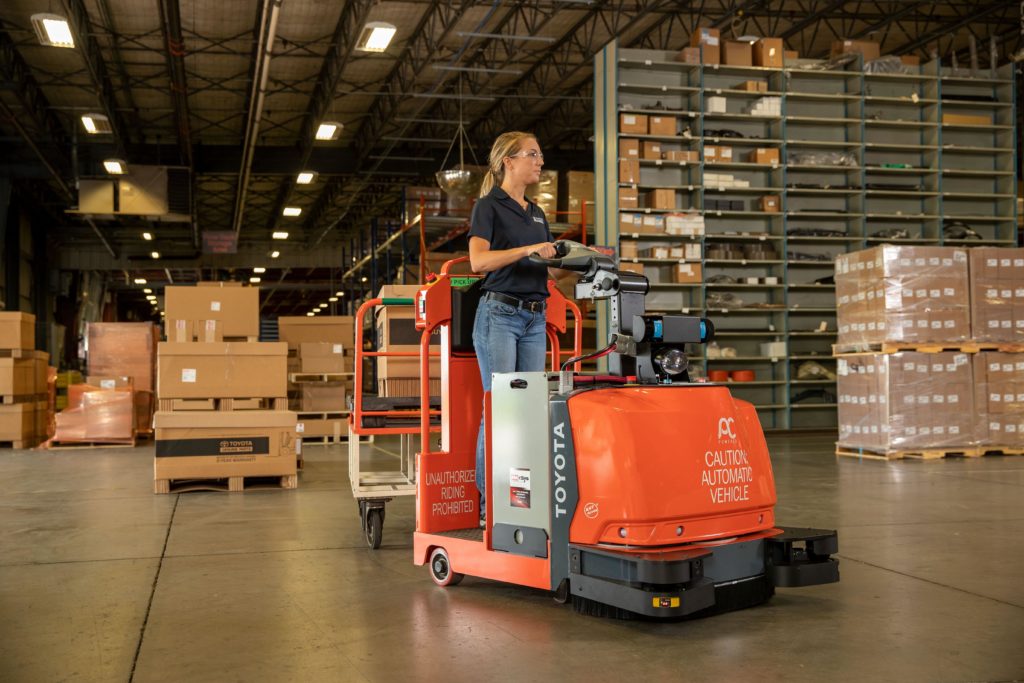
As industries grow, automated material handling systems will remain crucial for efficiency, accuracy, and scalability. From AGVs in material handling to AI-powered robotics, businesses must adopt automation to stay competitive.
Investing in automated material handling solutions today ensures a smarter, faster, and more profitable future.