This is the ultimate guide to forklift safety training.
By the end of this article, you’ll learn:
- Why forklift operator safety training is important
- OSHA’s training requirements
- Where to get forklift operator training
- How to develop your own in-house forklift training program
Let’s dive in.
Why Is Forklift Operator Training Important?
Training and evaluating your employees is costly and enormously time-consuming.
So why do we do it?
Your answers may range from “Because it’s required by OSHA”, to “Because we have employees working near forklifts and want to keep them safe.”
Either way, the good news is that all the time and money we spend on safety training will keep our personnel safer.
In 1984, a study was conducted by the National Institute for Occupational Safety and Health (NIOSH) to determine the effectiveness of a lift truck safety training program.
And the results indicate that better training reduces operators’ errors.
With a proper safety training program, NIOSH found that forklift operators can achieve a 61% improvement in their performance.
According to OSHA as well as many other experts, when errors are reduced, accidents are reduced as well.
Thus proper safety training is vitally important to our employees’ safety.
The trick is to provide the best possible safety training to your forklift operators and pedestrians.
Lucky for you, this article is here to help!
What are OSHA’s Powered Industrial Truck (PIT) Training Requirements?
While we don’t spend time and money on tow motor training just because it’s mandated by OSHA, their requirements are exactly that: requirements.
PIT training requirements are governed by OSHA’s standard 1910.178(l), which states:
“Training shall consist of a combination of formal instruction (e.g., lecture, discussion, interactive computer learning, video tape, written material), practical training (demonstrations performed by the trainer and practical exercises performed by the trainee), and evaluation of the operator’s performance in the workplace.”
Generally, forklift operator training should cover the:
- Types of lift trucks used in a specific work environment
- Hazards created by the use of those vehicles
- General safety requirements (such as pre-shift inspections)
- General principles of safe forklift operation
This training should be both formal and practical instruction, which we’ll cover in more detail below.
Do forklift operators need to be trained specifically on every forklift they operate?
Operators need to be trained on each type of lift truck they’ll be expected to operate.
That said, once trained on a specific type of lift truck, they don’t require additional training if operating the same type of fork truck from different manufacturers.
That’s unless the truck or the work-related applications are different from what’s required in standard 1910.178(l)(3).
What is the Formal Instruction Requirement?
The formal instruction component of forklift operator training is simply classroom education.
If you remember high school, then you’ll already be familiar with how this works.
The instructor may give a lecture, show a PowerPoint slideshow, play videos, or host a question-and-answer exercise to discuss training topics.
Overall, what’s taught in the classroom includes:
- Instructions, precautions, and limitations for different types of forklifts
- How to calculate forklift capacities
- How to load, transport, and unload materials safely
- How to perform forklift inspections before operating
- The different types of forklift fuel and how to safely work with them
- How to handle different driving surfaces
- Pedestrian safety principles
What is Forklift Practical Training?
Once the classroom instruction portion is complete, the next step is the practical training component.
OSHA states that:
“Prior to operating the truck in the workplace, the employer must evaluate the operator’s performance and determine the operator to be competent to operate a powered industrial truck safely.”
This is to ensure that operator trainees have some hands-on experience actually operating a lift truck according to proper safety procedures.
The practical training should be conducted according to the:
- Specific type of forklift the operator will use in the workplace
- Same conditions it’ll be used under
- Same types of tasks that the operator will be performing at work
What are the Certification Requirements?
Once the formal and practical training is complete, forklift operators can then be certified to operate a forklift in the workplace.
According to OSHA regulations, it’s the employer’s responsibility to certify that their operators have been trained and evaluated according to the OSHA standard.
The certification must include the:
- Operator’s name
- Training date
- Evaluation date
- Name of the person(s) performing the training or evaluation
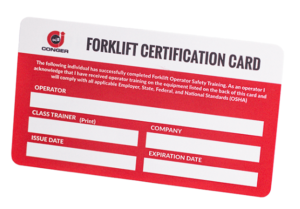
Alternatively, you can hire an outside consultant to perform your operator safety training.
If that’s the case, then you have a shared responsibility for ensuring that your operators complete both classroom and practical training before using any industrial equipment.
That means providing proper documentation and evidence that your employee completed their forklift operator training.
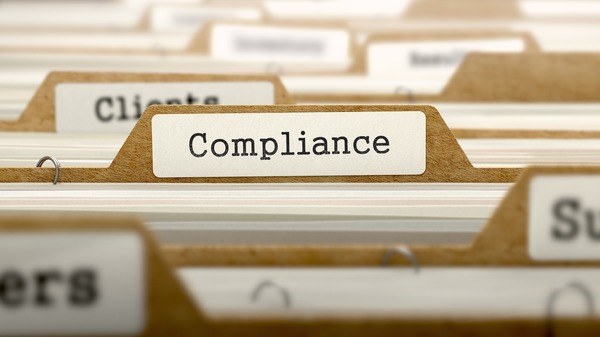
Unfortunately, OSHA doesn’t specify what the “proper documentation” or “evidence” should look like.
So what separates the good documentation from the bad?
If our years of experience have taught us one thing – it’s the type and quality of documentation your employees receive that can make all the difference during an audit.
After training, the employer still has a shared responsibility to certify that their operators are both competent and safe.
Determining this takes place in the form of a hands-on evaluation.
What Should a Forklift Operator Performance Evaluation Include?
During an evaluation, the training instructor will evaluate trainees on different forklift operating procedures.
Evaluation typically consists of obstacle courses, picking up sample loads, and in general, seeing how the operator trainee handles driving, turning, and reversing.
Specifically, operators should be evaluated on each of the following items:
Inspection
- Did the operator complete a pre-operational inspection?
Traveling Without a Load
- Is the operator’s seat belt on?
- Did the operator put the forks in the correct travel position (4-6 inches above the ground) before moving the lift truck?
- Did the operator perform a 360-degree check before moving?
- Did the operator sound the horn before moving?
- Is the operator facing the direction of travel?
- Does the operator’s body remain inside the operator’s compartment?
- Does the operator demonstrate the correct procedure for a blind intersection?
- Did the operator check their end swing when turning?
- Did the operator maintain a consistent distance from the corner/obstacle when turning?
Picking up a Load
- Did the operator square up to the load/is the load centered?
- Is the truck the correct distance away from the racking/stack?
- Did the operator elevate the forks to the correct height?
- Are the forks leveled for entry into the pallet?
- Did the operator drive the forks fully into the pallet?
- Did the operator apply the brake while using the hydraulic controls?
- Did the operator apply the correct amount of tilt to the load?
- Did the operator use the hydraulic controls in a smooth manner?
- Does the operator’s body remain inside the operator’s compartment?
- Did the operator perform a 360-degree check before reversing the load?
- Did the operator sound the horn before reversing the load?
- Did the operator lower the load to travel height (4-6 inches above the ground) before turning/traveling?
Traveling With a Load
- Are the forks placed in the correct travel position (4-6 inches above the ground)?
- Did the operator sound the horn before moving?
- Is the operator facing the direction of travel?
- Does the operator’s body remain inside the operator’s compartment?
- Does the operator travel with an unobstructed view? (Or if the load restricts their view, did they drive in reverse?)
- Did the operator maintain a consistent distance from the corner/obstacle when turning?
Depositing a Load
- Did the operator square up to the racking/stack before elevating the load? (No turning after they approached the location and elevated)
- Did the operator apply the brake while using the hydraulic controls?
- Did the operator level the load correctly for the deposit?
- Did the operator lower the load gently on the racking/stack?
- Is the pallet in the correct position on the racking/stack?
- Did the operator perform a 360-degree check before reversing?
- Did the operator sound the horn before reversing?
- Did the operator lower the forks to travel height (4-6 inches above the ground) before traveling?
Parking the Lift Truck
- Did the operator park the truck away from any doors, exists, or emergency routes?
- Did the operator lower the forks to the ground?
- Did the operator put the lift truck into neutral?
- Did the operator apply the parking brake?
- Did the operator shut off the lift truck?
What Are OSHA’s Forklift Refresher Training Requirements?
Forklift certification isn’t a one-and-done thing, like getting your regular driver’s license.
Instead, forklift operators must be re-evaluated periodically to ensure they maintain the necessary knowledge to operate safely.
Overall, reevaluations must be completed every three years.
However, certain circumstances can arise that require operators to be reevaluated before that three-year mark.
In standard 1910.178(l)(4), OSHA lists the scenarios that will require forklift operator refresher training:
-
The operator has been observed to operate the vehicle in an unsafe manner
-
The operator has been involved in an accident or near-miss incident
-
The operator has received an evaluation that reveals that the operator is not operating the truck safely
-
The operator is assigned to drive a different type of lift truck
-
A condition in the workplace changes in a manner that could affect the safe operation of the fork truck
These evaluations can be a discussion with the employee, written documentation of previous training, performance testing, or simply observing the employee.
What Are the Top OSHA Forklift Violations?
OSHA is very serious about following its rules.
Unfortunately, not everyone does follow the rules.
And that’s why forklift-related violations are the 7th most frequent violations that OSHA sees, which is pretty consistent from year to year.
In their latest report, OSHA notes that there were 1,932 forklift-related OSHA violations in the fiscal year of 2020.
According to Patrick Kapust, deputy director of OSHA’s Directorate of Enforcement Programs, here were the top forklift violations in 2020:
Violation #1: Operator Training and Safe Operation
-
Standards Cited
- 1910.178(l)
- 1910.178(l)(1)
-
Specifics
- Failure to provide appropriate training
- Failure to ensure operators have been properly trained on the type of truck they’ll be using
Violation #2: Refresher Training and Evaluation
-
Standard Cited
- 1910.178(l)(4)
-
Specifics
- Failure to provide refresher training when an operator is observed operating unsafely
- Failure to provide refresher training every 3 years
Violation #3: Certification
-
Standard Cited
- 1910.178(l)(6)
-
Specifics
- Failure to ensure that forklift operators possess proper certification (improper documentation)
Violation #4: Operation of the Truck
-
Standard Cited
- 1910.178(p)
-
Specifics
- Failure to remove from service industrial trucks that need repair, are deficient or unsafe
Violation #5: Maintenance of Industrial Trucks
-
Standard Cited
- 1910.178(q)
-
Specifics
- Failure to ensure that those repairing forklifts are competent to ensure repairs are made properly
Where Is OSHA Seeing the Most Violations?
OSHA reported that some of the top sectors where violations took place were:
- General warehousing and storage
- Product manufacturing
- Recycling plants
What Are OSHA’s Fines for Forklift Violations?
OSHA’s website lists the penalties for different types of violations:
Type of Violation | Penalty |
---|---|
Serious | $975 – $13,653 per violation |
Other-Than-Serious | $0 – $13,653 per violation |
Posting Requirements | $0 – $13,653 per violation |
Failure to Abate | $13,653 per day beyond the abatement date |
Willful or Repeated (Serious) | $9,753 – $136,532 per violation |
Willful or Repeated (Other-Than-Serious) | $390 – $136,532 per violation |
Who Provides Forklift Operator Training?
Now that you’re an expert in forklift training requirements, let’s cover the different providers of forklift operator training.
According to OSHA standards, training can be provided by an outside consultant.
However, the employer must provide evidence of classroom and practical training.
And, they’ll have to confirm that their operators are competent and safe in the workplace.
Overall, there are three different options for getting forklift operator training:
- 1 Employer-provided training
- 2 Online courses
- 3 In-person courses
Let’s cover each option.
Employer-Provided Training
Some employers – especially larger companies that use lots of forklifts – will provide in-house operator training to new employees.
For those looking to get certified as a forklift operator, this is the easiest and cheapest way to go.
After all, the company provides the training to the employee and the employee is not responsible for the costs.
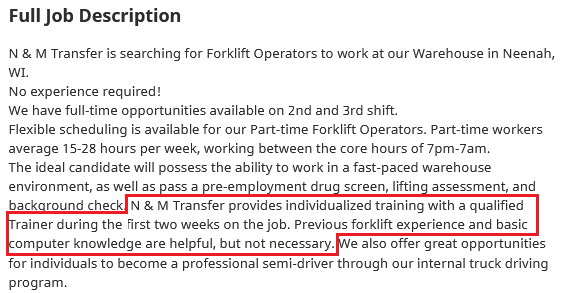
The downside of employer-provided training is that not many companies offer this option.
Additionally, it can be hard for those without previous operating experience to get hired by these companies.
Online Courses
Online forklift certification courses have become extremely popular in recent years.
A quick Google search reveals dozens of companies offering these services for a low cost, often between $50 and $200.
These courses generally consist of slideshows and videos, with quizzes after each section, and a final exam.
And at the end of the course, you’ll be able to download a certificate of completion.
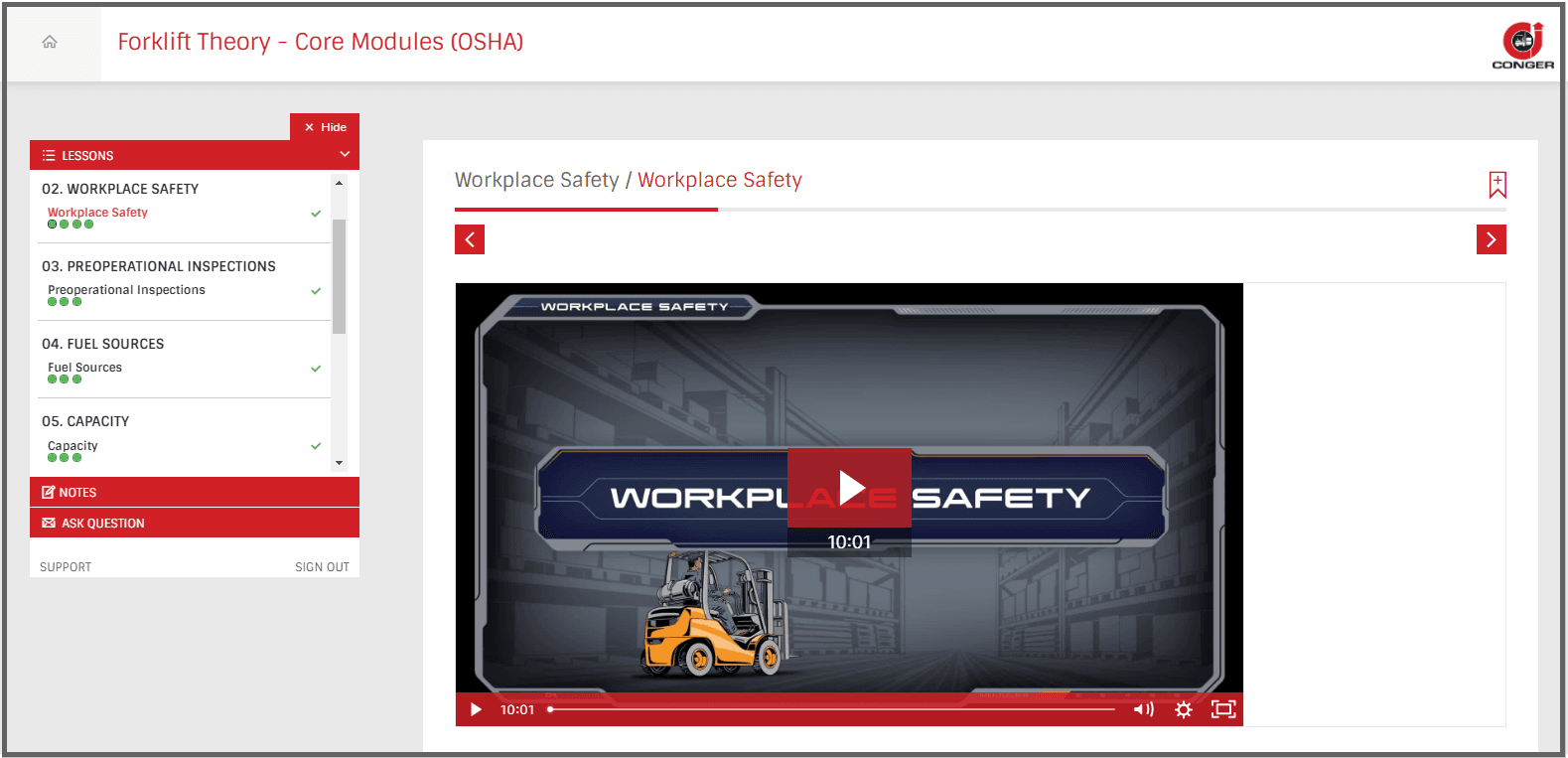
The downside of these courses is that, while they can fulfill OSHA’s requirement for formal instruction, they cannot fulfill the practical requirement.
Thus, online courses only get operators partially qualified.
Operators will still need to be evaluated operating a forklift in actual workplace conditions.
In-Person Courses
In-person courses are generally provided by forklift dealerships and technical colleges.
Operator-trainees will sit through classroom-style instruction, then be taught how to operate an actual forklift by the instructor.
These courses usually last anywhere from 8 hours to 2 full days.
Watch this short video to get an idea of what in-person forklift training classes are like:
Overall, in-person classes are an excellent way to get certified by an authoritative trainer.
The downside is that they’re generally more expensive than online courses.
You can read more about forklift operator training programs in our forklift license guide.
How to Start Developing Your Own Forklift Safety Training Program
If you have many forklift operators in your business, it may make sense to handle all safety procedures and training in-house rather than hire an outside contractor.
Some of the benefits of doing so include:
-
The convenience of working around your schedule and needs
-
Saving money on training costs
-
Develop a curriculum that’s specific to your equipment and operation
That said, making sure your in-house trainers are knowledgeable and skilled, along with complying with OSHA is not necessarily a walk in the park.
And a successful forklift safety training program will do both.
So here’s how you can craft a training program that hits all those targets.
1. Enroll in a Train-The-Trainer Program
To ensure their training programs meet OSHA’s recommended practices, many companies send their training personnel to specialized Train-The-Trainer classes.
These classes help trainers develop the skills to teach safety guidelines and protocols.
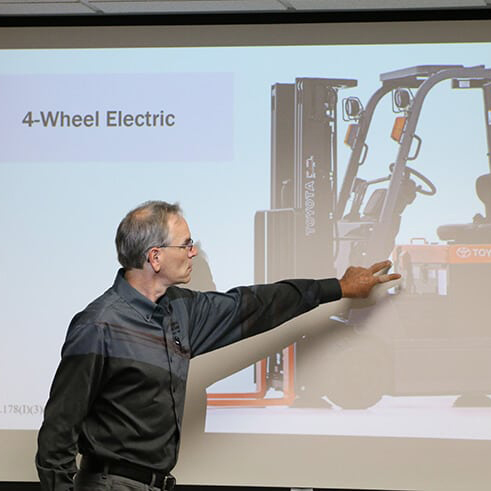
But having knowledgeable trainers won’t (by itself) make your safety training program a success.
You’ll also need to carefully evaluate your facility, your equipment, and your employees – both operators and pedestrians – to create a comprehensive forklift equipment safety awareness program that protects your employees and your assets.
The rest of the steps below will guide you as you begin developing your program.
2. Identify the Equipment in Your Workplace
Your operators will need to be trained on each type of equipment they’ll have to operate.
So go ahead and identify what types of equipment your operators currently use.
This will help you refine your training curriculum.
3. Evaluate Your Facility’s Hazards
If you’re new to safety training you may not realize just how many hazards are present in the workplace.
Many hazards differ depending on the type of forklift and your application.
For example, a sit-down rider lifts loads much higher than a walkie pallet jack.
Therefore the sit-down rider is more likely to be involved in an accident with a falling load.
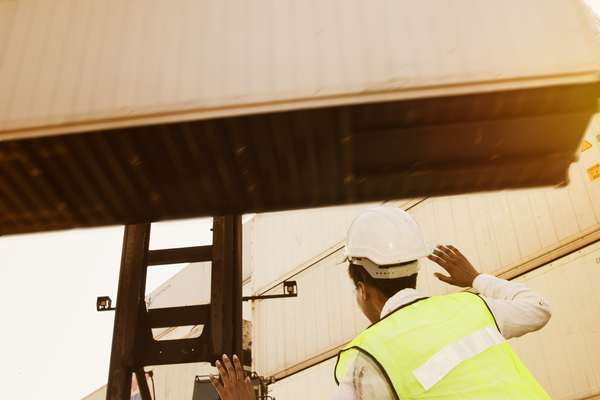
Likewise, pedestrians can be at greater risk in retail applications due to the high frequency of pedestrians working near forklift operations.
Regardless of your forklift type, your forklift operators and pedestrians should be aware of the hazards associated with your worksite and application.
To get you started, just a few of the hazards that may apply are listed below:
Walk through your facility and identify hazards that both operators and pedestrians will encounter during their daily activities.
Any hazards that may affect your worksite and application must be covered in your operator safety training as work site-specific instruction.
Make sure you train employees on safety protocols for navigating these areas.
4. Establish Your Training Methods
You’ll need to determine when and how your operators and pedestrians will be trained and what type of training they’ll receive.
Recall that training can include videos, slideshows, lectures, discussions, and the like.
Just be sure to include both in-class and practical components for operators.
5. Create Your Training Program Content
Your training program should be comprehensive enough to cover everything an operator needs to know to safely operate a forklift.
We’ve put together the following forklift training checklist to ensure you don’t miss a topic that should be covered:
Workplace Safety
- What is the employer responsible for?
- What is the supervisor or manager responsible for?
- What is the forklift operator responsible for?
- What are the rights of the forklift operator?
- What are the penalties for forklift-related violations and accidents?
- What are the best practices for pedestrian safety for forklift operators?
Forklift Inspections
- When are forklift inspections required?
- What are the two parts of a forklift inspection?
- What items should be checked during each part of a forklift inspection?
Download These Free Forklift Inspection Checklists
Print and reuse this free daily/weekly forklift inspection checklist template as often as you need to. Chose whichever format you’d prefer below and click to instantly download.
Fuel Sources
- What are the different fuel sources for forklifts?
- What are the steps involved with inspecting, watering, and charging forklift batteries?
- How can you detect a propane leak?
- How do you change a forklift propane tank?
- How do you inspect a forklift propane tank’s integrity?
Capacity
- How can you tell how much weight your truck can lift?
- How can you tell how high you can lift the load
- What does “de-rate” mean and how can you calculate it?
- How do you read a data plate?
- What does capacity mean?
- What is the rated capacity?
- What does load center mean?
- What is the rated load center?
- What does the center of gravity mean?
- What is rated lifting height?
Stability
- How can you avoid forklift tip-overs?
- What are the most common causes of lift truck tip-overs?
- What should you do if your lift truck tips over?
- What are the principles of stability?
- What affects the stability of a lift truck?
- What are the different types of momentum?
Material Handling Basics
- What are the main elements of basic forklift driving safety?
- What is the proper way to pick up loads?
- How do you properly transport loads?
- How do you transport barrels, drums, and kegs?
- How do you deposit a load?
- How do you properly secure your load?
- When should you use a spotter?
- What is the procedure for entering and exiting a semi-trailer?
- What is the procedure for parking and securing a lift truck?
- What are the different lift truck classifications?
Also, make sure pedestrians know safety procedures concerning forklift operation.
6. Determine a Valid Employee Evaluation
Evaluations should include a written test combined with a visual evaluation of the operator’s skills using the equipment.
Use our free practice test below along with the evaluation checklist provided in the “What Should a Forklift Operator Performance Evaluation Include?” section as inspiration for your forklift training materials.
7. Develop a Documentation System
Remember: As the employer, you’re responsible for certifying that your operators have been trained and evaluated.
So make sure that you keep detailed records of the training, in case of an audit.
8. Prepare Refresher Training
Whether one of your operators is involved in an incident, conditions change in your facility, or it’s simply been 3 years since the last one, refresher training is inevitable.
So be prepared for it.
Review the section titled “What Are OSHA’s Forklift Refresher Training Requirements?” to ensure you know when it’s required and how to perform one.
Conclusion
There you have it: The complete guide to forklift safety training.
Now, we’d like to turn it over to you.
Are you an aspiring forklift operator?
If so, what did you learn about forklift training that surprised you the most?
Are you in charge of your own company’s forklift safety training?
What did you learn that you can use to create, revise, or strengthen your operator training program?